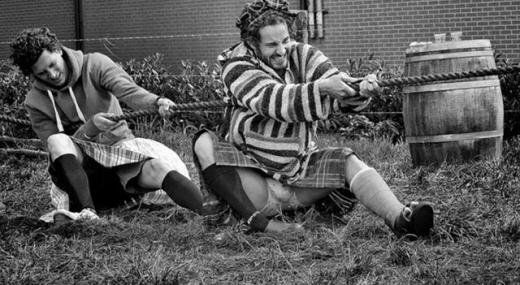
In 1996, the TSSC (Toyota Production System Support Center) began working with my company to create one-by-one production capability in our product assembly. Previous to TSSC’s assistance, we’d moved the furniture and machines into cells, creating the appearance of flow production, but we lacked the problem-solving know-how and management discipline to create real flow.
ADVERTISEMENT |
Remarkably, after several months of focusing on our pilot line, it appeared that all of the pieces of the puzzle had been identified and matched, and that impediments to flow had been remediated. Our kaizen support team and assemblers had worked daily to simplify, standardize, levelize, balance, and mistake-proof assembly operations. Conveyance routes were also standardized, providing material just in time at a rate of three kits every 12 minutes to match a customer takt time of four minutes per assembly. It was now time for our first live trial of a full production day with a production goal of one product every four minutes—or 120 products by day’s end.
…
Comments
Commitment or Perseverance
I prefer the term Perseverance over Commitment, as the former suggests hardship and, in many of these cases, it is being able to put aside our human emotions and continue with the actions to move forward to a successful outcome that matters.
The Power of Commitment
The hardest part of my job is continual improvement. Shop workers know when we improve efficiencies it means less money in their pocket. No more over time. Very hard to get buy in. How do you address the financial shortfall to workers? How will they benefit? More pay? Bonuses? ???? And we can't just say they get to keep their job instead of the plant shutting down becasue we are losing too much money.
Add new comment