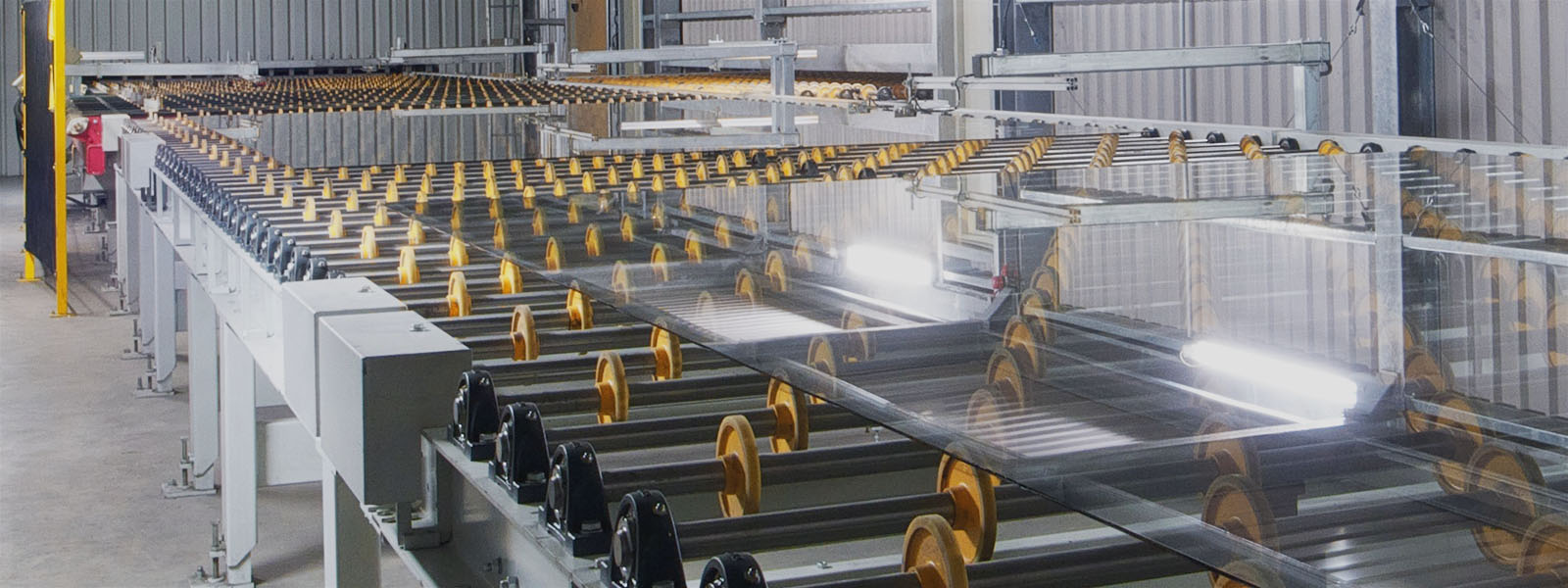
Digital transformation initiatives that aim at getting manufacturers to Industry 4.0 have been around a while and will assuredly continue to be with us for quite a while longer. But what can often get lost by manufacturers in the push to digital transformation are the reasons why one would want to undertake this journey in the first place, which in turn should all boil down to one essential reason: Preserving and enhancing the company’s position in the market.
There are many ways to do that, of course. You can improve efficiencies, for example, and increase throughput. But another area that’s incredibly well-suited to digital transformation initiatives is reducing total cost of quality and, in particular, reducing the costs of defects to manufacturers.
Why defect cost is important to target
That’s important because the costs of defects to manufacturers rapidly pile up in several ways: Defects that make it out the door to customers—so-called “escapes,” for example—are, of course, very costly. But in attempting to mitigate that problem, many manufacturers generate a different problem for themselves: They configure their machine vision systems to see defects that aren’t even there—so-called pseudo defects, false calls, or false rejects—which in turn results in the high costs of unnecessary rework or waste.
But false calls aren’t the only daily problem with visual inspection systems that manufacturers need to solve. According to the Association for the Advancement of Automation, besides the 56 percent of manufacturers who report problems with false calls, there are other defect detection problems with which manufacturers are struggling:
• 50 percent of manufacturers report that their visual inspection system struggles with complex surfaces.
• 42 percent report that their visual inspection system is unable to deal with variations in the pieces being inspected.
• 41 percent report that the labor costs attached to their visual inspection system are simply too high.
Artificial intelligence is already becoming table stakes for manufacturers
Clearly, advances in the visual inspection status quo are needed—and those who implement advances will be ahead of their competition. In fact, we’re getting to the stage where Industry 4.0 (I4) initiatives will be table stakes just to stay in the game. These numbers bear that out: Almost 70 percent of manufacturers plan on incorporating I4 tech and, more specifically, AI tech, into their facilities—which means that the 30 percent of companies who aren’t planning on implementing AI are at risk of self-inflicted obsolescence. But, on the plus side, of the 70 percent of manufacturers looking to implement some sort of AI-powered solution on the factory floor, two-thirds of them are still in the proof-of-concept or pilot stage—so there’s still time to catch up.
Those numbers point to the need for digital transformation simply to deny manufacturers within a market a competitive advantage. But why all of the interest in AI in the first place? And why should those in quality roles care? A few numbers from McKinsey are revealing: AI-driven productivity gains of up to 50 percent are possible, and defect-detection accuracy rate improvements of 90 percent are also possible. But what does this look like in practice?
A real-world deep learning defect detection example
This image is an example of defective and nondefective product pulled from Sage Automotive Interiors. Which of these pieces of fabric shows a defect?
This turns out to be a multimillion-dollar question, and it was asked every day at Sage. The right answer is that images two and four show defects. But if you didn’t get that right, don’t feel too bad. Because of its existing visual inspection system, Sage also was struggling to get it right—to the tune of approximately $2 million annually.
We’ll talk more about this particular case a little later. For now, what you need to know is that the Spyglass Visual Inspection (SVI) solution has helped Sage solve this complicated and expensive problem.
Mariner’s deep-learning, AI-driven SVI solution is enabling manufacturers to capitalize on the promise of dramatically improved productivity and quality by providing a simple solution to previously challenging problems of defect detection and elimination.
More about Spyglass Visual Inspection
Spyglass Visual Inspection’s deep-learning AI uses ResNet, the most advanced deep-learning algorithm available at this writing. It also uses a unique training pipeline and a class rebalancing procedure that solves some of the problems inherent to manufacturing data sets, such as not having enough images of a particular type of defect. Its powerful technology is beyond the scope of this article, but if you have more in-depth questions about deep learning or AI, please feel free to contact Mariner.
Deep learning is how SVI detects defects, and that happens on-premises at the manufacturer. But the cloud also serves as a vital part of how SVI eliminates defects: It's how we do centralized management, telemetry correlation, and provide alert criteria and behavior. It’s also in the cloud that deep-learning models are retrained as they learn from real-time data.
To summarize, because it dramatically enhances defect detection and elimination, SVI provides a unique blend of reduced costs and increased productivity. Costs are reduced not only by eliminating the number of escapes that reach the customer, but also in fewer false defect detections that result in needless and costly reworks or rejections.
SVI and its deep-learning AI accomplish this in a few different ways, as we shall see.
How SVI generates return on investment
First and foremost, SVI learns the different kinds and features of defects that it sees on production lines and is able to discern patterns that are too large or too finely nuanced for even expert human inspectors to see—and that’s why it outperforms existing machine vision systems that are built using the traditional rules-based approach. Even better: We have instances in production, for example, where SVI identified a defect category unknown to the customer’s existing system.
And because SVI outperforms human inspection, experienced quality assurance personnel can be redeployed to other high-value assets within a plant. Furthermore, because human inspection typically forces lines to run at substantially less than full speed, removing the human constraint allows for increased throughput.
Taken together, these benefits mean that our customers are producing more product, at higher quality and lower cost, than they were before implementing SVI.
Real-world defect detection, part 2
Sage had a very high false-reject rate of 34 percent on some of their textile lines because their existing vision system was so tightly tuned to prevent escapes that it struggled to tell certain defects from nondefects—it couldn’t reliably tell the difference between lint and a stain, for example, and was halting whenever it saw a piece of lint.
SVI reduced the rate of false rejects to less than 2 percent, which allows Sage’s lines to operate without human inspection and has practically doubled production speeds—and that has generated approximately $2 million in annual ROI. It’s a great case for how digital transformation can transform quality—a fact not lost on Sage, which is rolling out SVI to even more of its lines and facilities.
Getting past the Industry 4.0 credibility gap
One of the reasons many Industry 4.0 and digital transformation projects aren’t moving forward is that value can be hard to demonstrate up front; if value could be shown initially, of course, it would be vastly easier for manufacturers to green-light quality and other digital transformation initiatives.
That’s why we believe that a proof-of-value offer should be a best practice for Industry 4.0 or digital transformation initiatives—and why Mariner has created a 30-Day Proof of Value offer for SVI.
If you’re a business decision maker for your company—or can bring a business decision maker to the table—who agrees that improving customer satisfaction, reducing costs, and increasing throughput would have significant business impact, Mariner will set you up with its 30-Day Proof of Value engagement at no charge. Mariner will train your quality personnel to identify, classify, and label defects in the images. Once you have a hundred or so labeled images, deep learning will build an AI model for your product to demonstrate just how successful SVI will be on your lines. This iterative process continues until it demonstrates more accuracy than your human inspectors—and if it doesn't, you owe Mariner nothing.
Wrapping up
This concrete example of how SVI dramatically lowers quality costs while increasing product quality and output serves as a useful example of the kinds of digital transformation that manufacturers and quality personnel should look for when mapping out their Industry 4.0 objectives. Indeed, these kinds of changes can provide pronounced competitive advantages for manufacturers who adopt before other companies in the market. Conversely, manufacturers who aren’t already looking to digital transformation initiatives face the existential threat of being left behind by their competitors in an increasingly tight market.
Add all of that up, and it’s clear that digital transformation both can and must be used to preserve and enhance a company’s position in the marketplace. At the end of the day, that’s truly what lies at the core of quality.
Add new comment