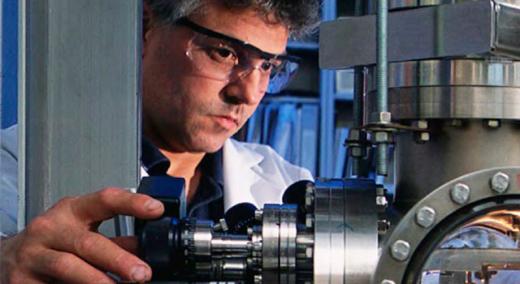
People often use the terms maintenance and reliability interchangeably. However, they are two separate concepts. Although there is some overlap, their scope and focus are quite different.
ADVERTISEMENT |
Understanding those differences, as well as how each concept affects the other, is a necessary step for optimizing your assets’ performance.
Defining maintenance
The ISO 14224 standard defines maintenance as a “combination of all technical and administrative actions, including supervisory actions, intended to retain an item, in or restore it to, a state in which it can perform a required function.”
In other words, maintenance encompasses all of the reactive and proactive actions we take to keep assets in optimal working condition.
Equipment is designed to perform a function. Maintenance ensures it functions as designed.
Defining reliability
The same standard defines reliability as the “ability of an item to perform a required function under given conditions for a given time interval.”
…
Comments
Upside down
The reliability definition used by the author is actually narrowing down the scope of reliability by introducing the time interval constraint. It therefore seems like a misunderstanding when the conclusion in the article ends up with the complete opposite by broadening the reliability definition.
Maintenance is better viewed as the processes realizing reliability. And with that perspective it is reliability that will be a subset of maintenance in a manufacturing environment.
Businesses have notoriously been bad at maintenance management with poor reliability as as the outcome. As a result, there seems to be a pressure to redefine reliability, and I suspect this pressure is mainly from reliability consultants. But as clearly defined by ISO, prevention and administrative tasks are a part of maintenance. This obviously includes, analysis of failures, long term thinking, improvements, etc.
Add new comment