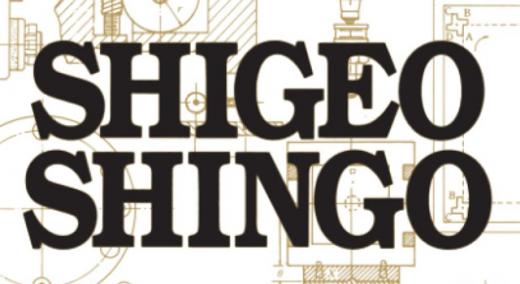
A Revolution in Manufacturing: The SMED System (Routledge, 1985)
Last May marked the 35th anniversary of the Shingo Prize, an award bestowed each year to recognize organizations that demonstrate the principles and methods espoused by its namesake, Shigeo Shingo. Although I haven’t made it to every celebration and award ceremony, it turns out that I was the only person at this year’s gala who actually attended the very first award ceremony back in 1989. So, I’ll memorialize it here as best as I can recall. It seems important to me to remember the beginnings of a great movement.
…
Comments
The First Shingo Prize
I think some of the problem and possible causes of organizations not really 'getting' Shigeo Shingo were his books and teachings were in some ways not really 'knew'. He copied aspects of largely American and British leaders at the time in productivity, O&M, work study, work simplification, wokplace flow layout Industrial Engineering (IE) experts / leaders in Maynard's Industrial Engineering compendium HB - various editions. As manifested in Shigeo's book, "A Study of the Tovota Production System From an Industrial Engineering Viewpoint" from 1989 i.e. ironically when the first Shigeo Prize was awarded, well to one company.
His SMED and OTED were step-changes but had it foundations in IE Flow Process Charts for work done off-line and on-line for die changes, set-up and changeovers aka Shigeo "Convert as many internal operations as possible to external ones".
His 'process' and 'operation' were insightful but then and still not well understood. The Toyota Production System has such processes but TPS is only one part of many Toyota "Systems" all centered around "TQM and the Science of Statiistcal Quality Control" (See Prof Amasaka - "Toyota New JIT" as per Amasaka's employment at Toyota and post academic and peer-reviewed research).
Shingeo Book extract: "Operations are the work or actions performed to accomplish this transformation; the interaction and flow of equipment and operators in time and space. Process analysis examines the flow of material or product. Operation analysis examines the work performed on products by worker and machine. To make fundamental changes in process, we must distinguish product flow (process) from work flow (operation) and analyze them separately." "https://elsmar.com/Cove_Premium/Toyota%20Production%20System/ToyotaProd…"
Add new comment