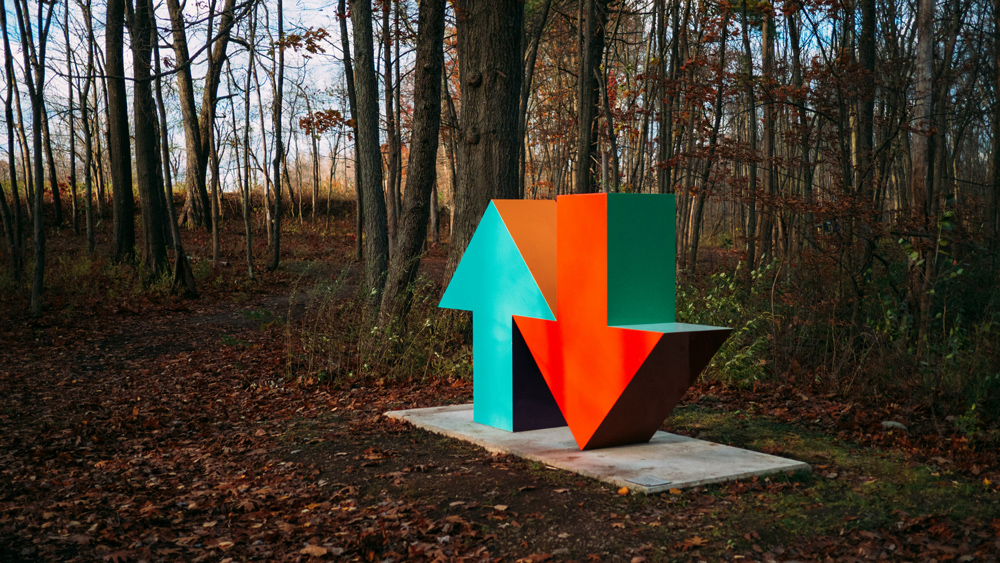
The plan-do-check-act (PDCA) cycle plays a central role in fostering improvement by facilitating a structured and ongoing approach to problem-solving. Because the PDCA cycle is ongoing, it also plays a central role in helping organizations navigate shifts in the economic climate, align with new regulatory requirements, adapt to rapidly advancing technology, and more.
ADVERTISEMENT |
Maintenance teams play a particularly important role in implementing the PDCA cycle. PDCA is an inherently proactive strategy and relies on the contribution of maintenance personnel. Maintenance technicians will perform several critical functions throughout the PDCA cycle. They will, for example, identify systemic issues, optimize equipment performance, and track performance improvements.
…
Comments
PDSA is not PDCA
I would suggest a read of this.
Deming emphasised PDSA study, understand why, not check if plan worked…. Fundamental difference explained better than I could here:
https://deming.org/explore/pdsa/
PDCA
In my experience many teams trying to implement/execute PDCA leave the rails between C and A. When the action they try out to solve the problem they isolated they celebrate and call it quits.
Successful teams usually take the step of trying to turn the problem back on after having (supposedly) done something to "fix" it. There is no allowance for the problem having gone away for some other random reason or spontaneously. In short, they're pleased to be rid of the problem but don't really know if they fixed it or have it under control. Not a good situation.
Add new comment