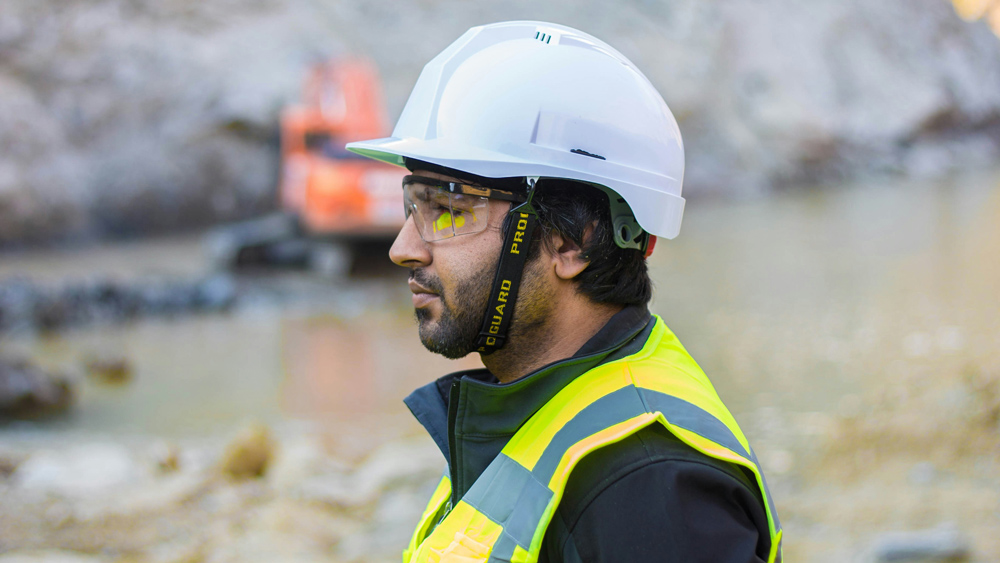
Photo by Ahsanization ッ on Unsplash
For any manufacturer, ensuring well-run, successful processes and protocols is the backbone of a successful and profitable operation. Yet, despite the most well-laid plans, circumstances can change and manufacturers may sidestep best practices in the race to meet demand. Still, ensuring quality, safety, and regulatory compliance remains paramount. To minimize associated risks—both within your operations as well as in your supply chain—it’s essential to perform internal audits.
ADVERTISEMENT |
Audit findings are discrepancies from regulations or other standards. An audit isn’t only about discovering discrepancies, but also about resolving them, especially in highly regulated industries such as pharmaceutical and food and beverage. Internal audits meticulously examine core processes, from raw material procurement to production and distribution, to verify adherence to predefined quality parameters and regulatory standards. By identifying and rectifying deviations promptly, internal audits safeguard the reputation of the brand and mitigate the risk of noncompliance financial penalties.
…
Add new comment