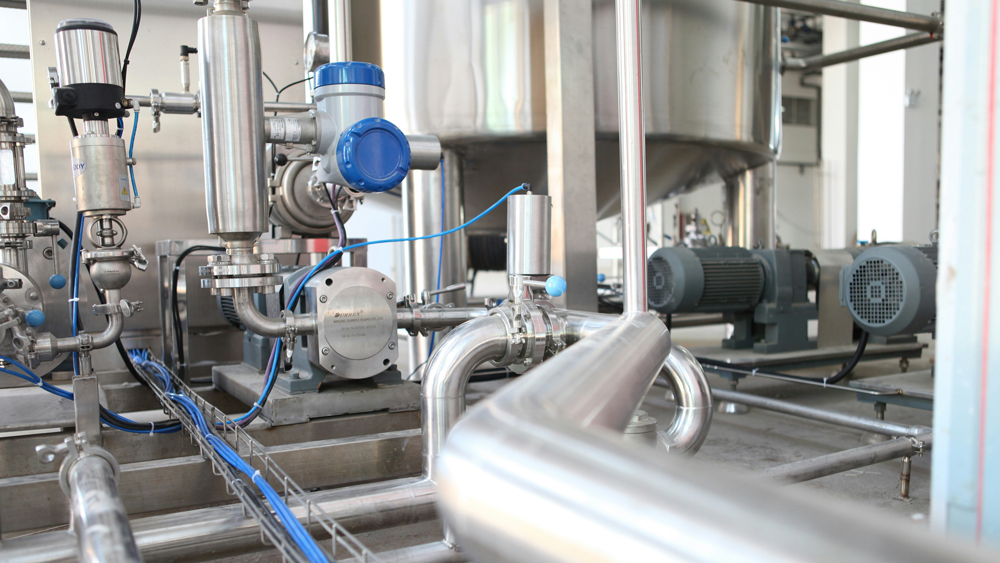
Photo by Crystal Kwok on Unsplash
Facility and equipment maintenance is most effective when performed proactively and regularly. This kind of routine maintenance can take many forms, ranging from the most basic approaches to complicated strategies using sensors and data to trigger maintenance. Time-based maintenance (TBM) is a useful part of even the most sophisticated maintenance programs, but it’s also a great place to begin if you’re just starting your maintenance journey.
ADVERTISEMENT |
In this article, we’ll provide a quick but comprehensive overview of the steps, benefits, and challenges involved in implementing an effective TBM program.
What is time-based maintenance?
Time-based maintenance, or routine maintenance, is a type of proactive maintenance in which tasks are performed at fixed time intervals, regardless of their condition. The purpose of TBM is to ensure that assets receive the regular maintenance they require to keep operations running smoothly and prevent breakdowns.
…
Add new comment