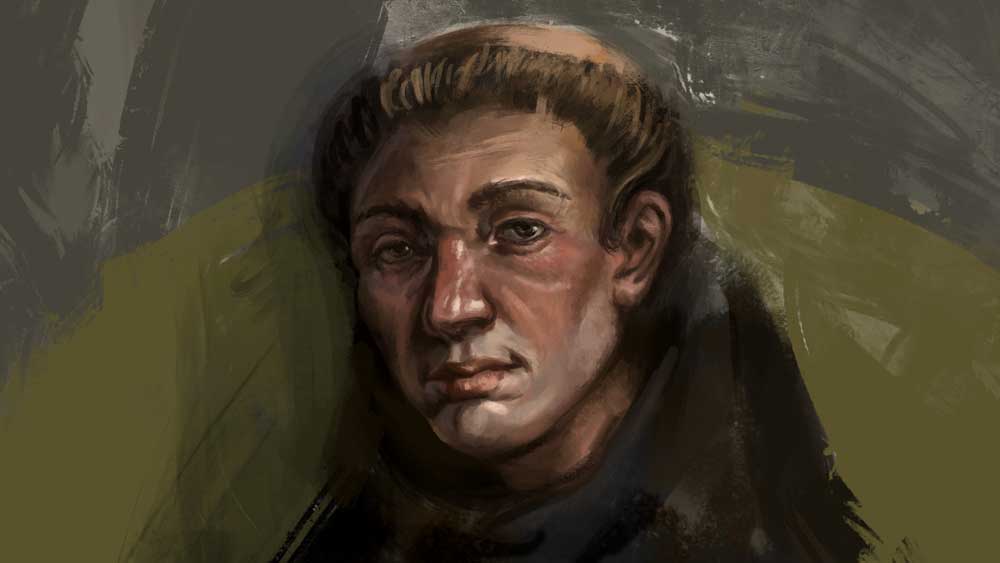
William of Ockham (1285–1347). Credit: AldrianMimi, Creative Commons
It was another busy morning at the monthly operations meeting. Lindsay, the operations manager at TechElectronics, a growing manufacturer of consumer electronics, called the meeting to order. As usual, they started with the routine updates—inventory levels, production schedules, and customer complaints. But today there was something more pressing on the agenda: delivery delays.
ADVERTISEMENT |
“All right, team,” Lindsay began. “We’ve been missing some crucial KPIs and not getting our products to customers on time. The warehouse is properly stocked, production is on schedule, but our products aren’t getting out the door as quickly as they should be. We’ve had a few near-misses with our major retail partners, and that’s not a position we can afford to be in.”
Lindsay paused and looked around the room. Everyone was silent and a bit puzzled. They had all worked hard to optimize the company’s inventory management system, improve production efficiency, and streamline the logistics process. So why were they still facing these delays?
…
Comments
Occam’s razor and TRIZ keep it simple
Well said Akhilesh!
Add new comment