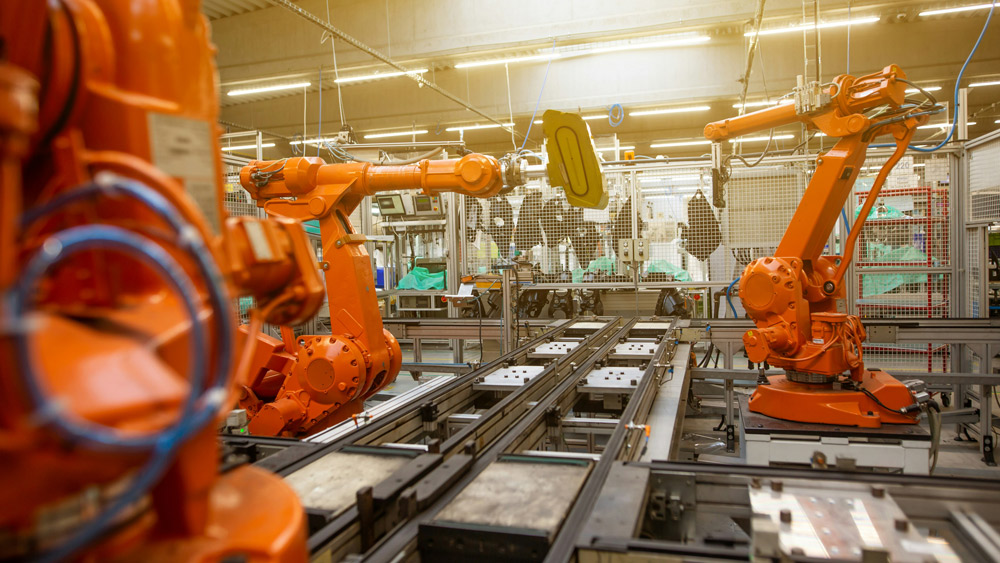
Photo by Simon Kadula on Unsplash
In manufacturing, especially in assembly systems, every operation plays a role in shaping the quality of the final product. The influence of these operations can carry through each stage, ultimately affecting the quality of the finished products delivered to customers. Understanding how these subassemblies and operations contribute to the overall product quality is essential for identifying root causes of issues, resolving quality problems, and driving continuous improvement.
ADVERTISEMENT |
A manufacturing system is complex, with numerous processes and variables affecting the overall quality of products, as illustrated below in Figure 1. This dynamic applies whether you’re looking at a single operation or the entire system. Given this complexity, it’s important to ask: How does each process step or factor relate to the product’s final quality? For instance, how does a specific process in producing a subassembly affect the quality of the completed product? This insight is key to effective problem-solving and quality control.
…
Add new comment