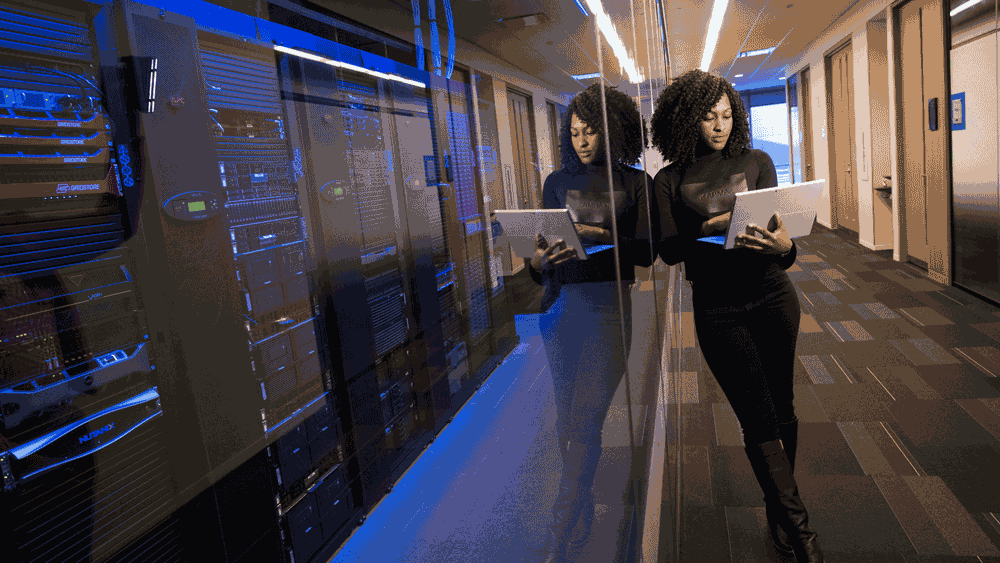
Photo by Christina @ wocintechchat.com.
Body
Quality management has evolved far beyond traditional checklists and periodic inspections. For complex supply chains, quality is no longer a static endpoint. It’s a dynamic real-time process deeply interwoven with collaboration, transparency, and data-driven decision-making. As supply chains grow more global and regulations tighten, companies must adopt innovative technologies to ensure efficiency and sustainability without compromising quality.
ADVERTISEMENT |
…
Want to continue?
Log in or create a FREE account.
By logging in you agree to receive communication from Quality Digest.
Privacy Policy.
Add new comment