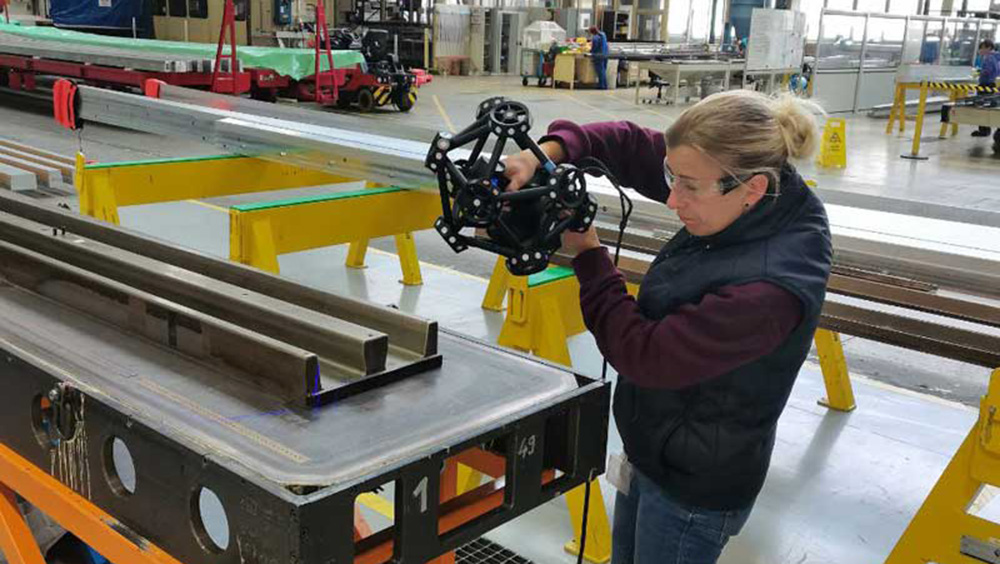
A GKN Aerospace team member uses the MetraSCAN 3D to scan an aerospace part. Credit: Creaform
GKN Aerospace Deutschland is a global tier-one supplier of airframe and engine structures, landing gear, electrical interconnection systems, transparencies, and aftermarket services.
ADVERTISEMENT |
The company has more than 38 manufacturing locations in 12 countries and 17,000 employees worldwide. It continuously invests in research and development to improve aircraft performance, efficiency, and safety—and to shape the future of the aerospace industry.
GKN Aerospace elevates the performance of more than 100,000 flights every day.
The effect of legacy aerospace 3D measurement methods
The metrology team at GKN Aerospace faced major challenges in its part inspection workflows. For one, traditional touch-probing systems provided only selective evaluations, which often resulted in insufficient data for detailed assessments of complex free-form surfaces.
…
Add new comment