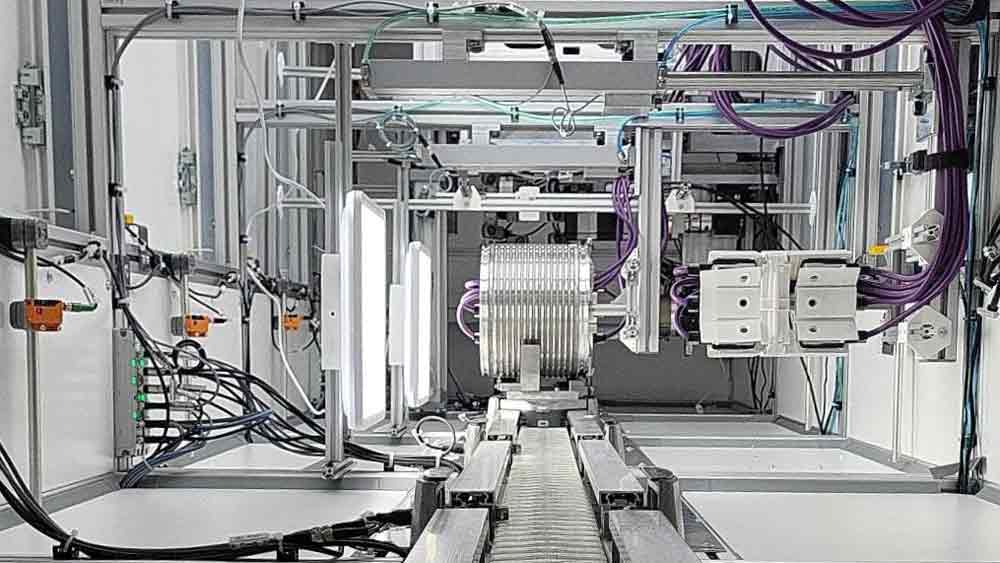
IDS Imaging Development Systems
Electric motor housing inspected by 42 uEye XC cameras.
In areas such as high-precision metalworking, accuracy is nonnegotiable. This includes the automotive industry and its suppliers, which are in crisis in Germany for several reasons. The industry is under enormous pressure to deliver products of impeccable quality while reducing operating costs (for example, by increasing process speeds).
ADVERTISEMENT |
The automotive industry’s quality assurance standards are strict, the component geometries are complex, and the demands for precision and process reliability are enormous. Fluctuations in detection, insufficient traceability to individual serial numbers or batches, and changing environmental conditions can lead to costly errors, production downtime, and customer complaints.
Vivaldi Digital Solutions has developed an exemplary, innovative solution for AI quality inspection in real time. In addition to an edge server with an Intel processor, intelligent image processing plays a key role in its “SensorBox.” Designed for an automotive supplier and its production site in the Czech Republic, up to 70 USB3 uEye+ XC autofocus cameras from IDS Imaging Development Systems perform automatic visual inspection for surface inspection in several inspection cells.
Round component geometries with strong reflections must also be inspected with process reliability.
“The IDS cameras integrated into the test cells capture high-resolution images of the surface of aluminum components from German OEMs, in this case an electric motor,” says Uwe Siegwart, managing director at Vivaldi.
The captured images are preprocessed to optimize factors such as exposure, white balance, and color correction. The AI recognizes various surface defects such as scratches, pores, or dirt.
Siegwart says, “There are strict requirements at the plant in the Czech Republic. According to the defect catalog, defects from 0.2 millimeters must be reliably detected. The test time per component must not exceed 36 seconds.” Up to 2,400 electric motor housings are tested daily with a completely automatic system.
Simultaneous image recording ensures a complete inspection and helps to maintain the cycle time.
Why choose the IDS uEye XC camera?
Eike Humpert from Vivaldi’s business development department says, “The decisive factor was that the autofocus camera can capture several surfaces at different distances from the camera.”
This simplifies the testing process and ensures greater efficiency and flexibility. That’s crucial when, for example, different component variants need to be tested. With the macro attachment lens, the minimum object distance of the camera can also be shortened very easily.
“The BSI pixel technology enables the sensor to deliver consistently precise and reliable results, even in changing light conditions,” says Jürgen Hejna, product owner of 2D cameras at IDS. But it’s not just the excellent low-light performance and minimal pixel noise that make the sensor particularly suitable for this application. “The 24X digital zoom, combined with auto white balance and precise color correction, contributes significantly to the success of this demanding test procedure,” Hejna says.
AI-supported analyses and camera control via edge server
The simultaneous image processing task is complex, and the challenges are diverse. Aluminum parts often have shiny surfaces with reflections that can obscure the images. It’s difficult to reliably recognize defects such as scratches, cold runs, chatter marks, or surface irregularities because they’re often obscured or distorted by the reflections. This, along with other material and environmental variations, means AI-based image processing must be able to distinguish precisely between the normal material structure and actual raw areas that are considered defects in surfaces to be processed.
Image processing is carried out via an optimized infrastructure. Up to eight cameras can be connected per USB hub, enabling simultaneous recording of several inspection areas. A maximum of two of these USB hubs are connected to a “cam controller” that bundles and processes the image signals.
Several cam controllers are networked with the edge server. This server not only calculates the AI-supported analyses but also communicates directly with the system controller, which coordinates the triggering of the cameras and ensures synchronized recording.
“Image processing is a central component for traceability, which is the actual technological centerpiece of the solution. IDS is the ideal partner for this point,” says Siegwart. “Digitized quality data acquisition in real time and linking with other production parameters not only increases efficiency but also significantly reduces rejects and rework. Errors are minimized, costs are reduced, and production processes are optimized.”
The system has already paid off in the Czech Republic: The number of complaints per year has been reduced by two thirds, and the number of unrecognized surface defects has even been reduced to zero.
Outlook
The market for digital quality control is developing rapidly, particularly due to advances in camera technology that enable higher resolutions. “Optimized image-processing processes and tools also make it possible for real-time analyses to be carried out by end users,” says Humpert. “Improved resolution, more compact design, and price-optimized cameras are in demand.”
IDS’ industrial camera portfolio is designed to meet this demand with state-of-the-art technology.
IDS camera model U3-36LOXC
Add new comment