Body
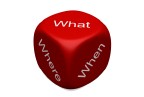
Why do we do lean? We often get so focused on making improvements that we forget why we are making improvements. It becomes a “make an improvement for improvement’s sake” mentality. We shouldn’t forget the guiding principles of our actions, meeting customer needs (internal, external, shareholders, and community) and respect for people. The improvements should be following the rules in use:
- Highly-defined activities.
- Clear and binary customer/supplier connections.
- Simple and direct flowpaths.
- Continuous improvement using the scientific method.
Meeting customer needs
…
Want to continue?
Log in or create a FREE account.
By logging in you agree to receive communication from Quality Digest.
Privacy Policy.
Add new comment