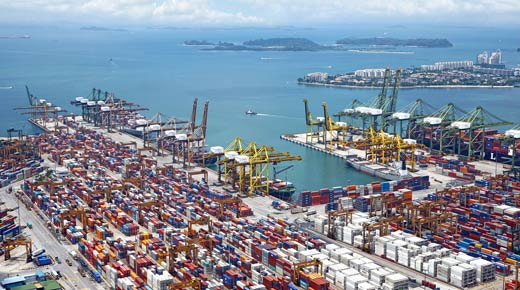
Ever wondered why quality control (QC) professionals check a sample instead of 100 percent of a shipment during inspection? Or maybe you’ve wondered why they use acceptance sampling, rather than simply inspecting an arbitrary quantity of goods, such as 10 or 20 percent?
ADVERTISEMENT |
Most importers value the transparency that quality control inspection provides. They know that catching any unacceptable quality issues or nonconformities before shipping is crucial to being able to address them before they hurt their bottom lines.
But many importers are at a loss when it comes to determining how many units they should inspect. They want to check as many as possible to get a representative look at their total order, while simultaneously trying to balance the time and cost needed for inspection. Frustration often results when importers don’t understand how standards dictate the sample size chosen for, and ultimately the results of, their inspection.
…
Comments
Just 1 more thing
Inspecting 100% of a lot is like adding a work station to the production line. Therefore the inpector becomes a production worker. And no matter how qualified the inspector is - will make mistakes. I've seen this in practice. Meanwhile taking a sample of a lot and usually taking it into a sterile environment gives the inspector the time and the peace of mind to actually "do the job" of inspection.
AQL / RQL
Modern Acceptance Sampling plans use both AQL and RQL (with associated specified risks of incorrectly classifying the lot). And accepting a lot in no way ensures that a lot is anywhere near as good as the AQL. Acceptance only implies you are highly confident (depending on the consumer's risk chosen) that your quality level is better than RQL which of course is higher than AQL and much higher than the quality level needed. Unfortunately, many users of acceptance sampling do not really understand the relatively low level of protection these plans actually provide (with typical sample sizes)
Bottom line, Acceptance Sampling should be viewed as an audit procedure to detect major issues that somehow went undetected. If one wants to really control quality, it must be during the production process via SPC (rather than hoping to "find" defects in a sample after the product has been produced.
Add new comment