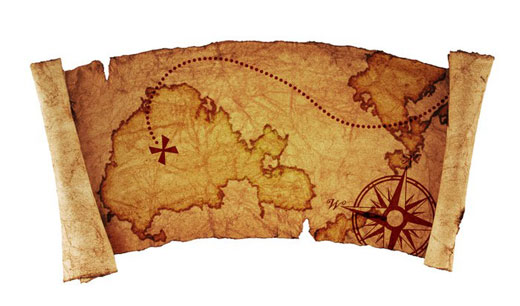
The cost of ineffective corrective action can be astronomical when you consider the monetary and reputational impact of delayed problem-solving. On a small scale, repeat problems—even minor errors—send a message to customers that you just don’t care to get it right.
ADVERTISEMENT |
And when poor problem-solving leads to more significant quality escapes? You could be looking at $10,000 per minute in line-stoppage charges from the customer, or even a $10 million recall.
To ensure corrective actions reduce risk, automotive and aerospace suppliers should avoid key mistakes around measuring effectiveness, root cause analysis, and tracking closure. Here are five that require particular attention.
1. Not measuring effectiveness over time
Most often, corrective actions fail because companies fail to measure the actions’ effectiveness over time. This is true for individual corrective actions as well as for the corrective action process as a whole.
…
Comments
#2 The importance of involving shop-floor personnel in RCA
One of the most important realizations that I have made as a quality professional is that RCA activities absolutely MUST include shop-floor personnel. These are the true experts in the process, and are best equipped to give an accurate view of how a process is actually carried out... not how it SHOULD be carried out. I won't even begin a formal RCA without at least one shop-floor employee present.
So pleased to see this point highlighted in the article!
Add new comment