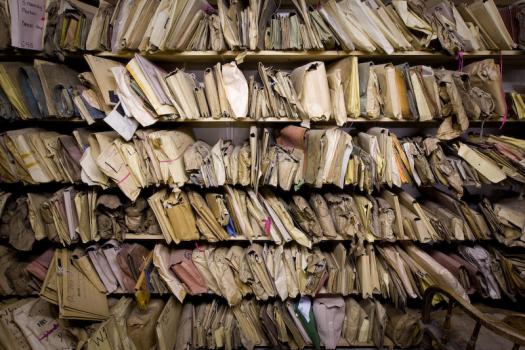
Can you imagine trying to do CAPA faced with this?
Credit: Dave Wilson Cumbria
Sponsored Content
For quality management to be effective, a solid corrective action process is critical. ISO standards and general best-practice guides suggest—and even mandate—a set procedure and proper documentation for addressing and correcting issues.
ADVERTISEMENT |
In fact, 72 percent of quality professionals we surveyed named corrective and preventive action as the most critical quality and compliance process in their organizations. That’s why many people choose to automate this process, to make it as simple and efficient as possible.
The importance of automating corrective actions
Because corrective actions are such a vital part of quality management, it’s essential to launch them in a way that yields objective, consistent results. Automation removes the possibility of human error and ensures that your corrective actions are systematic and efficient.
Automation proves helpful in the following steps of corrective action:
…
Comments
Flaws in corrective action
After being involved in Quality Management for over 30 years. I find the idea of Corrective action to have quite a few flaws.
1- Its common to observe organization use FMEA for Processes and Product but very rarely have I seen it used in relationship to failures. I usually observe failures in Pareto and the attack made to address the largest contributor... but what about severity? Is that not more important than a simple volume of occurrence?
2- Most corrective action systems I run across are related to audit results, usually management system audit results. Rarely if ever do those audit results assess the impact of non-conformance occurring in terms of severity. Most CAR systems I observe, treat all Non-Conformance as if its all of the highest severity, which is simply nonsense. ISO does little to help in this arena as their management system standards default to the same ideal which is credulous. If result of non-conformance occurring bears no impact upon the organizations customer or its interested parties, is it worth addressing with a formal corrective action process? Common sense speaks against performing such acts.
3- Root cause... this idea related to a process is utter nonsense. Even the Ishiwaga diagram speaks to the fact that there could be at least 4 causes to a failure to meet expectations of an organizations customers or interested parties. Further within those four basic operations causes are multiple branches of causes. Yes a team might vote on the most likely cause, however they will never be able to prove root cause outside the operation of a machine. And What is the most common "Root Cause" observed? ....Operator error.....
4- Finally there is effectiveness of action taken, which is often left to the auditor to determine. Really? A team of individuals worked on discovering the so called "root cause" to a problem, came up with a solution or solutions, implemented said solution and then never measured the result of their work? Wouldn't effectiveness be that measurement?
5- ISO 9001 drives the corrupt thinking of corrective action by not marrying Clause 6 to Clause 10 of the 2015 version. Section 10.2 indicates the organization should evaluate the need for action to eliminate the cause(s) of non-conformity then defines those as
These are the issues I discover with current approaches to "Corrective Action" especially under schemes such as ISO's Management System Standards (9001, 14001, 45001 etc)
Add new comment