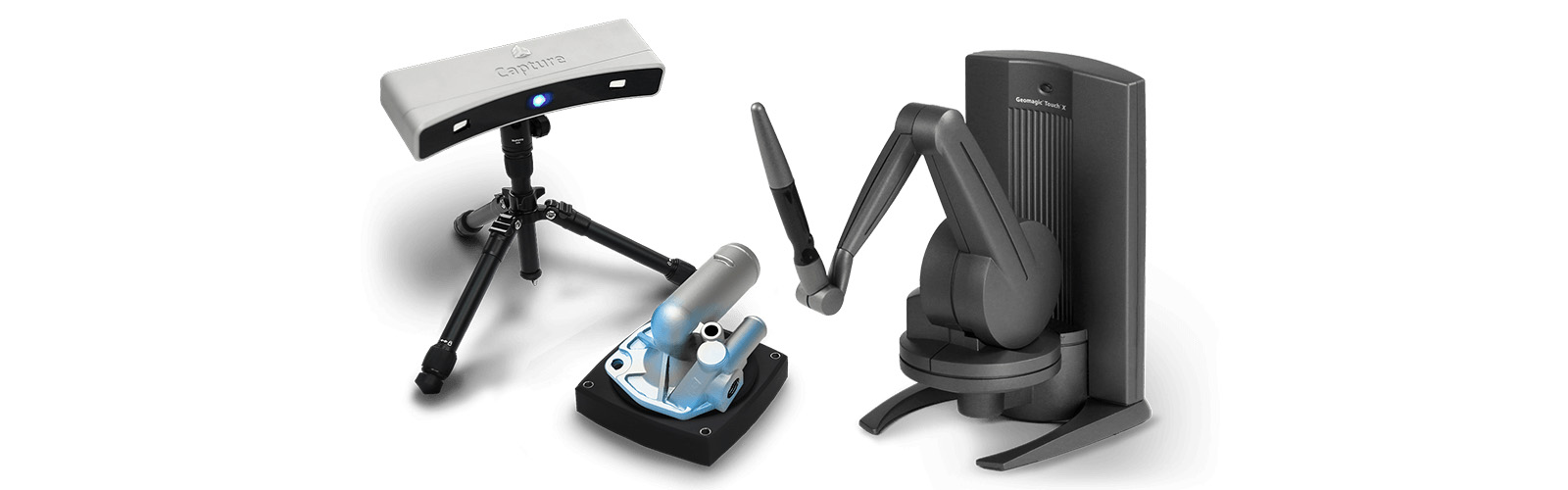
In today’s hypercompetitive environment, companies can’t afford to lag behind when it comes to the quality of their products—or the tools and technologies they use to ensure them. During the past two decades, 3D scanning has become an essential component of many companies’ quality control strategies. To help you take full advantage of 3D scanning technology, in this article we explore whether it is the right approach for your business, examine the right 3D-scanning hardware and software for your quality inspection needs, and offer tips on the right way to maximize your ROI.
Is 3D scanning right for your business?
Trusted for its accuracy, reliability, speed, and ease of use, the noncontact nature and exceptional flexibility of 3D scanning make it ideal for measuring a wide range of parts in a wide range of places. If you haven’t already taken the plunge, there are a number of key signs that indicate it’s time to dive into the world of scanning:
• You need to measure complex parts. 3D scanning measures every surface at millions of points, making it easy to inspect even the most complex shapes.
• You need to measure soft parts. 3D scanning only touches the part with light, so there’s no part deflection or deformation.
• Measuring parts takes too much time. 3D scanning is exponentially faster at collecting measurements than contact-based techniques.
• You need to remeasure parts you don’t have. 3D scanning creates a complete digital record that you can remeasure at any time.
• You’re not sure why some parts fail. 3D scanning measures the entire surface of a part, so you’re less likely to miss an unexpected deviation from nominal.
• You think you might be scrapping perfectly good parts. 3D scanning gives you a more complete view of your parts so you can make more informed decisions.
• You need to measure things in more places. 3D scanners and software are easy to use in the field.
The hardware: choosing the right scanner
Once you’ve decided to take the plunge, you need to decide which 3D scanner is right for you. There are many options available, each with unique pros and cons, but they can be divided into three basic types:
Laser triangulation scanners are one of the most popular and versatile 3D scan technologies. They pass a laser line over the surface of a part and, using straightforward trigonometric concepts, calculate the distance from the sensor to the scanned object’s surface.
|
Structured-light 3D scanners project a series of linear patterns onto an object and use sensors to recognize deformations in the patterns that indicate each pixel’s distance from the sensor. These systems are often referred to by their light source, commonly white light or LED blue light.
|
Medium- and long-range scanners use phase-shift or time-of-flight laser technologies to scan larger objects such as heavy equipment, aircraft, ships, buildings, or factory floors.
|
The software: making the right choice
It takes more than the right 3D scanner to get reliable measurements. You also need the right software—software that can effectively work with point-cloud data and quickly and efficiently get you the information you need.
There are three categories of software available to users of 3D scanners: Traditional contact measurement inspection software, which struggles to handle millions of scan points; 3D scanner operating software, which may offer add-on inspection modules but lack advanced capabilities like geometric dimensioning and tolerancing (GD&T); and scan-native inspection software, which is the best choice for most serious users of 3D scanning. There are certainly some compelling arguments in its favor.
Use your 3D scanner to the best of its ability. Modern 3D scanners collect up to 1 million points per second, so you can easily measure the geometry of your parts with exceptional resolution and fidelity. 3D scan-native inspection software can reliably and effectively handle these massive volumes of 3D scan data, help you take advantage of all that information, and maximize the potential of your 3D scanner.
Increase measurement precision. It’s a misconception that 3D scanning is inherently less accurate than contact measurement. An individual contact measurement will likely exhibit less random error and be more accurate than a single noncontact measurement. However, the copious amounts of noncontact measurements collected by scan-native software, combined with scan-specific algorithms, can yield equally or more precise measurements of the position, shape, and size of features on a part.
Open and work with large data sets easily. Scan-native software can handle such large data sets that it only takes three minutes to complete an inspection on a scanned part. Meanwhile other software options can spend up to 10 minutes on the same task or prove unable to handle even moderately large scan files. When you’re counting on 3D scanning to help drive your business, these constraints can add up to serious productivity losses.
Display deviation color maps on 3D CAD models. Imagine looking for your keys in a pitch-black room. Would you rather use a flashlight that illuminates only a small area, or flip the light switch and see the entire room? That’s the difference between using 3D measurement software that displays a basic color map on top of an imported CAD model and using native-scan software that displays a full deviation color map comparing your scanned part with a nominal 3D model. Native-scan software can also offer more advanced deviation analysis, such as 3D, 2D cross-section, boundary, along curve, silhouette, and virtual edge comparisons.
Use golden parts for comparison and analysis. High-quality 3D scan-native software allows you to create clean, nominal reference models from 3D scans of “golden parts”—parts that are perfect or nearly perfect—that you can then compare every other part to. The most advanced software will automatically define features on your scanned nominal so it behaves just like a full CAD model.
Measure features with GD&T. While a contact measurement system like a coordinate measuring machine (CMM) may be better at measuring a limited number of basic geometric features, for more complex parts you need scan-native software. It can automatically identify individual features in a 3D scan, filter the data intelligently to remove noise, and take reliable, accurate measurements. This will speed up your inspections and enable you to measure GD&T on your scanned parts too.
Create digital archives for future use. The best 3D scan-native software will save the scan data, nominal model, alignments, and every measurement you’ve taken on each part—all in one efficient digital file. This makes it easy to go back to any scanned part, see exactly how the data was manipulated, and make additional measurements whenever you need.
The hybridization of inspection and reverse engineering. When you invest in a 3D scanner, you not only gain the ability to measure your parts, but with the right scan-native software, you can use the power of reverse engineering to find and fix problems. You can easily update or recreate CAD models to reflect reality, rather than using an unmodified initial CAD model, or change CAD models to compensate for process-induced errors and end up with a part that has the desired geometry. Look for software options that combine inspection with reverse engineering and design capabilities to take advantage of this innovative approach to solving problems.
How to maximize your ROI
Ensuring you get the most out of your investment in 3D scanning is crucial. Here are some tips to help maximize your return.
Think differently. Go beyond simply replicating your current measurement processes. The flexibility of 3D scanning allows you to get creative and solve more problems.
Empower more people to measure more things in more places. One of the best things about 3D scanning is that the tools are generally easy to use and portable; you can take the scanner to the parts that need measuring and open up usage to more people in areas like design, engineering, and manufacturing.
Evaluate hardware and software independently. An excellent 3D scanner can be held back by mediocre bundled software, and vice-versa, so it’s important to research and evaluate both sides of the hardware/software equation with equal rigor. You’ll end up with the best system—with the speed, portability, comprehensiveness, and ease of use you need—when you separately select the best scanner and software.
And finally, don’t view the scanner as a panacea for all your needs across all your parts, as you’re likely to be disappointed; don’t assume your existing metrology software will work with your scanner; and don’t treat software as an afterthought—it’s just as important as the hardware.
Next steps
Discover more by joining 3D Systems expert webinar: “The Three Keys to Effective Scan-Based Inspection.” Pioneers in 3D printing and experts in Geomagic Control X—the world’s No. 1 scan-native inspection software platform—the global 3D Systems team offers exceptional experience and expertise in 3D inspection scanning.
Comments
3D Scanning: The Right Choice for Your Inspection Needs?
Just thought to tell you that I really enjoyed reading this. Thank you for a very detailed article on this topic.
K. T. Banafshe
Add new comment