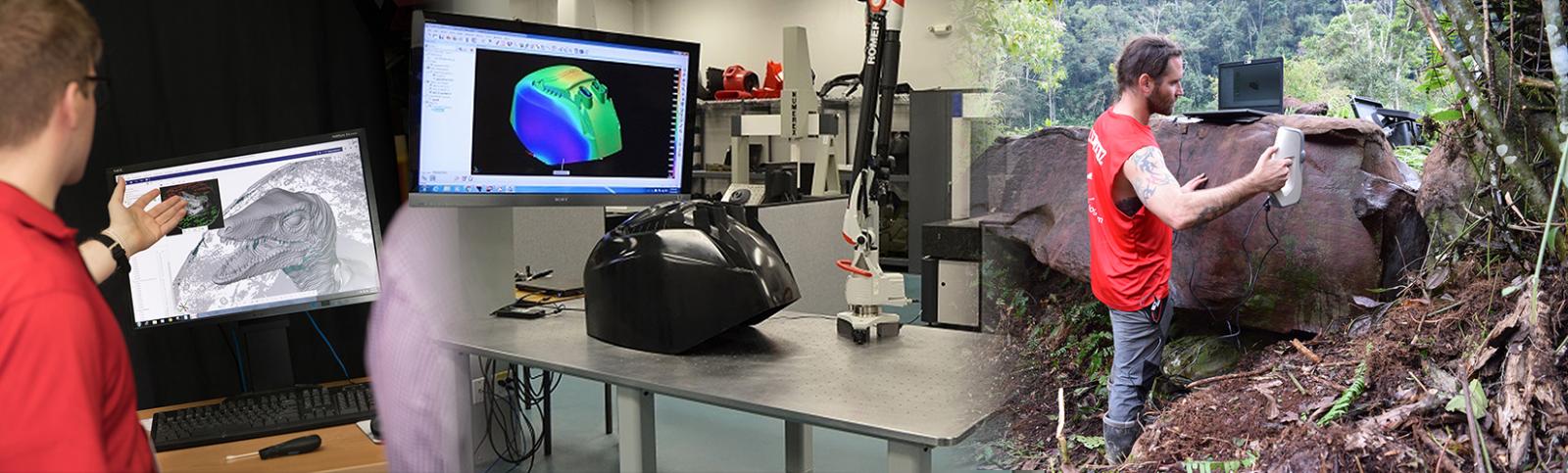
For more than 50 years, the benchmark for accuracy in measuring solid objects, whether machined, molded, die cast, welded, or forged, was the coordinate measuring machine (CMM). Typically using a solid, granite-base table along with a vertical, horizontal, gantry, or bridge-mounted arm and touch probe, measurements would be taken and compared in blocks to an engineering file, originally as 2D drawings and today as CAD files hosted in the cloud.
During the last two decades, however, a “new kid in town” has arrived on the scene, with power, size, point capability, and price value that are rapidly leaving the CMM technology in the dust.
![]() Typical CMM probes a part’s external dimensions at a limited number of touch points. Click image for larger view. |
3D laser scanning, plus the latest trend of industrial CT scanning, which is based on the same technology used for medical MRI, permit an array of points to be read, both external and now internal, on a wide variety of substrates and manufacturing techniques. 3D scans are made on many types of metals, composite, thermoplastic, elastomeric, wood, fiber, and fabric materials. CT scanning permits internal exploration of a thick aluminum casting, injection-molded plastic or rubber parts, even prepared foods, packaging, archaeological finds, and fine art. (The old joke is with CT scanning is we would have known about Venus de Milo’s arm problems long before they occurred.) CT scanning can produce results for porosity, dimensional, failure analysis, volume, and fiber orientation, all while leaving the part undamaged.
![]() 3D laser scan can capture millions of points instantly comparing them to a CAD file or cloud-resident data. Click image for larger view. |
In contrast to conventional, tactile CMM techniques, laser and especially CT scanning captures all surface points simultaneously, on even the most complex, convoluted surface areas. As an example, where a typical touch probe might capture 300 points of reference for comparison to a CAD overlay, the laser or CT will capture millions of points. Typical systems today can offer measurement accuracies to 4+L/100µm, referring to the VDI 2630 metrology guideline.
A customer recently came to us with the following scenario. An engineer at his company was boasting of having produced the “perfect part,” based on CMM deviation points. Our contact had used our scanning services in the past. We performed a quick blue-light 3D scan on the object and quickly determined the part was out of spec on several faces because certain critical points had been missed in the CMM protocol. Our millions of scan data points were fit to the deviation map, and the problem was tracked backed to the production source and rectified. Today, this company is a regular customer.
That example does not indicate CMM technology has outlived its usefulness, by any means. We continue to use it in our operations for certain measurements in many applications.
One important point to note is that the same software that manipulates data from the CMM can be used with 3D scanners and CT equipment alike. Because there are substantial cost savings to be realized in the purchase of a 3D-scanning device or the new generation of tabletop CT scanners, depending on the parts being examined, the transition from CMM to 3D or CT is more feasible today, economically. The driving factors for a company, when evaluating the service vs. purchase issue, are two.
The easier factor is raw cost, where a 3D scanner is typically half the cost of a CMM for measuring comparable part sizes. The other is more complex: the talent of the personnel doing the work. Experienced technicians have the ability to scan and process large data sets on a wide variety of substrates, geometries, and part sizes effectively. Coupled with the part volumes being processed and other factors, it is often more practical and profitable for a company to use a scanning service on an as-needed basis.
![]() 3D printing allows quick sampling of modified designs as well as finished prototypes, producing parts directly from the scanned data. Click image for larger view. |
An additional point to note in evaluating CMM vs. scanning is the time involved. To derive those 300 touch points referenced above might take four hours, while the 2.5 million points derived from a 3D scan would take 30 minutes. Because Polyworks software can be used on a CMM or 3D laser scanner, the time and money savings quickly accumulate. Plus, in this manner, companies can develop something of a “universal metrology” scenario at their companies by augmenting the existing CMM technologies with 3D and even CT scanning capabilities, making their quality control departments more powerful. (One practical note: We can train quality control, R&D, and production department personnel usually in three days or fewer to expand their capability from CMM to include 3D and CT scanning.)
In terms of the data created, 3D scanning produces color maps, inspections, first article inspections, or other outputs. What you can do with the data after completing the scanning is endless.
On the topic of substrates, it should be noted that CT scanning today offers the ability to evaluate a wide variety of dual-thickness and dual-density materials, with disparate examples ranging from an automotive firewall that might have differing thermoplastics or rubber, and thermoplastic elastomer materials co-molded to a candy bar with chocolate and nuts.
Note: The author welcomes all contact and questions regarding this article. In full disclosure, Exact Metrology performs 3D laser and CT scanning, plus sells, rents, or leases the equipment to perform such scanning procedures.
Comments
Cosmetic packaging
Hellow Matthew:
Thank you. It was a pretty interesting and useful article. I can see that 3d scanning has some advantages over CMMs in certain applications. I would like to ask you a question. I work in a cosmetic multinational company and we develop many new products as well as packages for fragrances, makeup, personal care, skin care and even bijuterie. Our suppliers are all around the world and we have identified that metrology is a key part of the success of every new launch we have. In that sense, do tou have any experience measuring packaging such as bottles, caps, pumps, cases, etc? Would you recommend to use 3D or CT?
Thank you,
Cesar
Cosmetic Metrology
Cesar,
Because of the wide range of technologies available today you can tackle your problem many different ways. If it were me I would look at CT scanning the assembled bottles. By doing this it would allow you to check the flush/gap of the closures, thickness of the material, porosity, and overall geometry back to the design intent CAD model. All of that can be checked with just one CT scan. Another benefit of CT scanning is depending on size of the parts and resolution you want to hold you can scan more than one part at a time. CT scanning also offers you the ability to do inline scanning as an in-process check. If you have any additional questions please feel free to contact me. 513-831-6620 or matthewm@exactmetrology.com
I had a chance to use both:
I had a chance to use both: newest CMN and newest blue light scanner from very reputable company. For measuring inspecting plastic parts. Bigger ant rather flat 10 x 8 in. An small one another 2 in.
Blur light was big disappointment becausr:
Setting proper lighting to have possible uniform exposure was next impossible
Number of trials to fill not detected or missing surfaces was countless.
Manipulations to obtain dicent set up was exhausting.
Prosess require transferring files between two programs.
Finally to get second part analizeayou have to go through it again.
Now in CMM :
Once we created program we can are able measure parts all over again and again with reproducible result and actually after per pert
Because you are using the 3d
Because you are using the 3d scanner in the wrong way. If you created the a program for it, then next time, you don't need to care about how you place the part anymore.
Scanning vs CMM
What I don't see in your article is any mention of precision. You said that a scanner would be half the cost of a CMM. To get the repeatability and reproducibility of a high precision CMM with tight tolerenced parts, I really don't think that statement is accurate as scanners in that price range are not very precise.
Add new comment