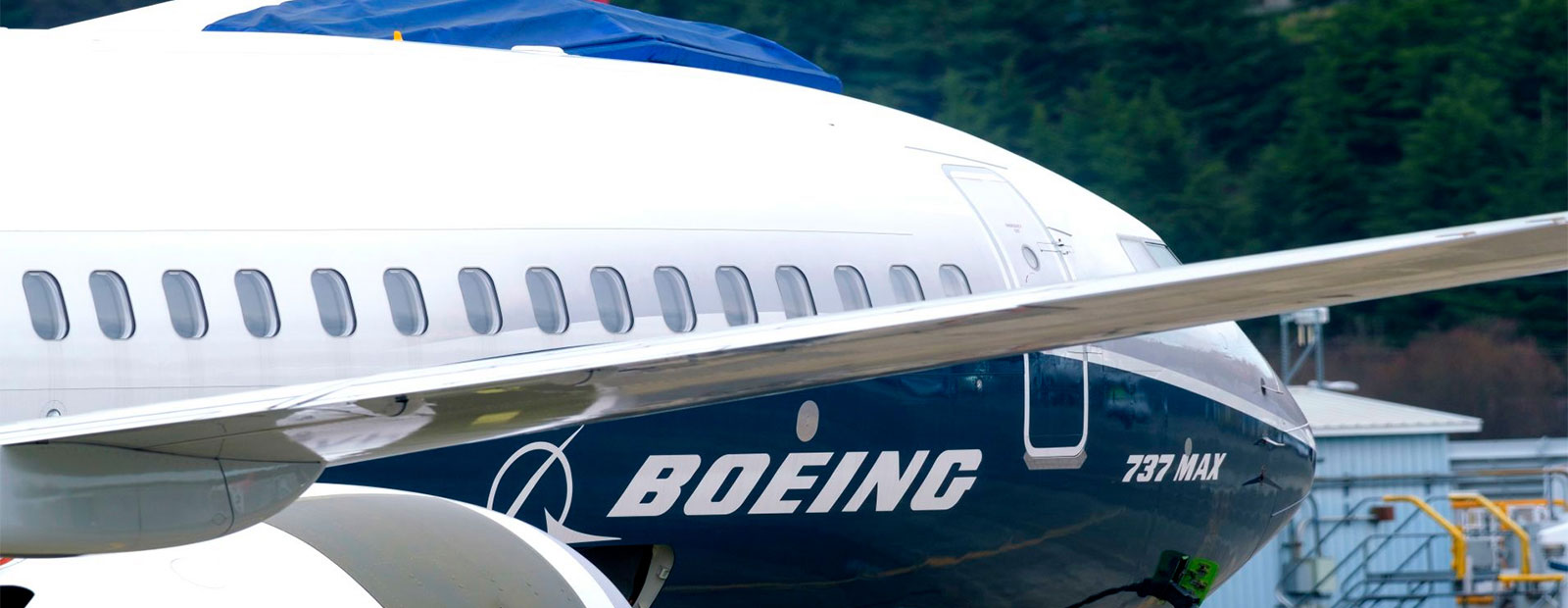
Boeing has been rife with issues lately. While the recent Ethiopian Airlines crash has dominated headlines and elicited an FBI investigation into the company, another federal body has stated it will be keeping a closer eye on Boeing’s safety shortfalls.
Boeing is now in hot water with the U.S. Air Force after tools, litter, and other work materials were found in newly delivered KC-46’s. High-ranking Air Force official Will Roper shared a statement to lawmakers, saying “debris translates into a safety issue.” Tankers were grounded for a week due to safety concerns, citing foreign object debris (FOB), which can lead to wear and damage over time.
One would imagine that the world’s leading aerospace company, responsible for designing and manufacturing more than 10,000 of today’s commercial airliners, would have rigorous quality control protocols in place. Not surprising, recent revelations have presented grave concerns about Boeing’s internal management and highlight the need to keep workplace standards in the spotlight.
A closer look at Boeing’s recent shortcomings have revealed a larger problem. “It’s clear that Boeing has insufficient process controls in place,” says Michael DiLeo, president of the Management and Strategy Institute. “While Boeing has a very strong safety record, incidents like this show the importance of a continuous improvement methodology being in place. If tools are being left on aircraft and no one notices, this is a sign that there is a breakdown of standards within the manufacturing process.”
So where does the nation’s largest manufacturing exporter begin to resolve its endemic process standardization issues?
The answer to this question requires first understanding that problems such as these are not common with proper protocol.
The Harvard Business Review has written extensively on what can be gleaned from Japan’s cultural practice of attention to detail, something that could prove beneficial to Boeing in light of its current position. Roper said it best in his statement to the press: “It’s simply following processes that Boeing has on the books, and having a culture all the way down to the mechanic level that embraces them.”
Japanese auto manufacturer Toyota has mastered this concept in what has been dubbed the Toyota Production System (TPS), by focusing on what takes place at the micro-level. Toyota’s success is due largely in part to TPS, or what in the Western world is refers to as the lean manufacturing model and the 5S system.
Lean manufacturing is a workplace methodology that optimizes productivity and ensures an effective operational flow. The five S’s of lean manufacturing are the core tenets upon which the concept was founded and center around the goal of waste reduction.
Air Force officials will be keeping a close eye on Boeing’s management as they struggle to regain the company’s place as a trusted partner. Implementation of the 5S model would have undoubtedly presented many opportunities to spot the debris and tools left behind in the KC-46s prior to delivery.
In a sense, 5S prevents the spread of issues by cutting them off at the root. The five S’s are as follows:
Sort (seiri)
Taking stock of all items present in the workplace and identifying extraneous ones. Human beings are imperfect creatures prone to error. Taking this step ensures a clear work environment that ultimately eliminates distractions that lead to errors, and reduces time spent looking for the items necessary to do one’s work.
Set in order (seiton)
Having the necessary tools neatly organized allows for greater ease of use. Optimizing the workflow by keeping tools nearby and in an order that is logical for the task at hand lends itself to a more functional space—think of a dentist’s tray. When performing tasks that require precision, order is a critical element to flawless execution.
Shine (seiso)
Cleaning the workspace on a regular basis. This step promotes safety for employees by making it easy to spot when something is out of order, preventing mistakes and deterioration of surroundings. Giving employees a sense of ownership and pride in their workspace leads to a cultural shift that is transferrable to the actual work itself.
Standardize (seiketsu)
Systematizing the workplace standardization process is crucial to executing the aforementioned processes. It ensures the steps are executed consistently across all levels, and provides a basis for replication—rinse, and repeat.
Sustain (shitsuke)
The final tenet of lean manufacturing, requires intention, from managers to their employees, everyone participating and investing in maintaining the standardization process by making it a way of life in the workplace. Self-discipline and regular evaluation of whether standards are being met, or must be revised to evolve with growth, are key in this step.
“FOD is really about every person,” says Roper. “Everyone in the workforce, following those procedures and bringing a culture of discipline for safety.” Boeing would do well to implement workplace standards around the 5S model, ensuring that the progress made following such a shift is sustained in the long term—something the Air Force has stated it will keep under careful observation for months to come.
Comments
Boeing’s 5S Problem
Excellent articel Morgan,
The importaqnce of 5S methodolgy is crucial when reduction of waste. The culture of waste reduction should be primary to any "lean" initative.
However, some may argue and use the "6TH" S. "Safety" take be incorporated into the thinking and actions within a workplace.
6S now not just 5S
Yes the 6th S is safety and should be a part of all Lean 6S type events, and processes.
6S relevance and importance
The focus of a 360 Degree Safety would make the 5S system more effective and pave way for an excellent Lean practice. Practicallly testing in Large, Medium and Small industries, I feel the right focus would bring in better results.
Do you seriously think Boeing
Do you seriously think Boeing hasn't already tried implementing 5S?
“It’s simply following processes that Boeing has on the books" -- yeah, they probably aren't following 5S with much discipline.
But that's different than saying that Boeing should look into 5S, as if they've never heard of that or TPS.
Inaccurate and ineffective
Inaccurate and ineffective article. I laughed pretty hard when I read that - Boeing should consider 5S. Article is written very well and content flows smoothly. It just wasn't researched at all. Depth of material shared in article was pretty limited. Shame on the author and shame x 2 on the editor. Quality Digest should present a more professional and effective/useful article to its readers.
Add new comment