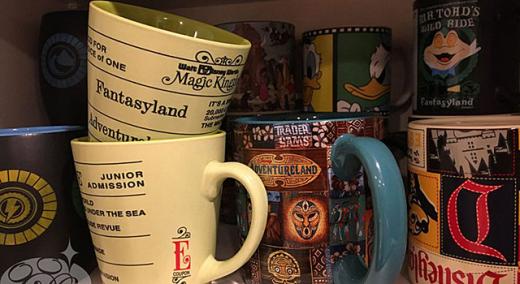
During the late 1970s, quality began to evolve from its historically Neanderthal, passive inspection approach to its current Cro-Magnon state, where its more proactive, project-based approach is bolted on to the operational status quo. Joseph Juran was a pioneer in such efforts. Various subsequent adaptations such as Six Sigma and lean evolved it further, but over time, it has become comfortably stuck in a misguided focus on tactical improvements at the expense of strategic improvements—i.e., doing things right as opposed to doing the right things right.
ADVERTISEMENT |
In 2011 Jim Liker, a professor of industrial and operations engineering at the University of Michigan, wrote the following to leadership expert Jim Clemmer (emphasis mine):
…
Comments
14 Points or Profound Knowledge
Davis,
Thanks for a very insightful article. I think you have articulated very well the stalled quality movement of today and some good reasons why we are stalled.
But I would like to point out that Deming, later in life, finally gave in to those who kept asking which point to work on first by elucidating his basis for the 14 points: Profound Knowledge. He basically said that the points flow from Profound Knowledge and that Profound Knowledge itself was a system in which all of the aspects of it worked together and were dependent on each other. With some thought. it becomes obvious that the 14 points are directly tied to Profound Knowledge. So it might be easier to persuade someone that seeking to learn about and implement Profound Knowledge, starting with the top leaders of an organization, and its management, might be the best way to proceed. Teach them about "appreciation for a system" so that system thinking becomes a way of life for management first, and then all members of the organization. Teach them about "variation" and how it works and why variation is a natural consequence of all processes which can, through quality improvement efforts, get better. Teach them about "theory of knowledge" so that managers especially will provide guidance and direction based on solid theory and that everyone in the organization understands such theory and evolves the theory when needed. Teach them about "psychology" so that they will know exactly how employees respond to the absurd stack-ranking and performance evaluation rampant in today's companies, among other things.
All of these, once disseminated, lead to every one of Deming's 14 points for management and make them logical things to work on as part of changing the organization's culture to one of quality and improvement.
- MIke Harkins
Another great article, Davis!
You know I'm always happy to read one of your articles, especially about Deming. We have talked about him a lot over the years, and have probably agreed on everything with the possible exception of the value of the Red Bead to teach SoPK.
I am afraid I am somewhat to blame for some the current state (Mea Culpa, Mea Culpa), however, or at least the consulting profession is to blame (along with a generous helping of Rule 4 of the Funnel)...I mean, it's mostly a problem of leadership failure, and the dominance of the shareholder primacy theory in business, and evreything else that has driven business leaders to continue embracing short-term results, performance evaluations, etc. But I have noticed some other trends over the years, too.
I think you are spot-on about Motorola. I know some people who worked there--good Deming-steeped people--and my understanding is that they were tryiing to operationalize the philosophy. They did a lot of great things. Then Welch was sold on it as a cost-cuttitng philosophy. You can certainly cut costs, and so the Big 5 got on board. They were accountants, not statisticians or quality professionals, so their nail was money, and their hammer became Six Sigma. I remember articles in Quality Progress by a PWC person who said that unless a Black Belt project was going to net you 250K, you shouldn't do it. I was appalled, and wrote to QP editors, but that letter was lost. So, we drifted (Rule 4).
The other thing, for all GE's early success with Six Sigme, their culture didn't change appreciably, either. My dad was a life-long GE engineer, who once told me that while he was glad I had figured out what to do with my life, he was sorry to see me getting into Quality. "At GE, our philosophy has always been that it's better to have a sister in a cathouse than a brother in quality control." That, along with some of his other platitudes--"A camel is a horse designed by a committee" and "the surest way to ruin something is to improve it"--kind of illustrate where that culture was. Now, you take a bunch of these people who have never cared at all about Quality, problably learned the least they could in the mandatory training, and put someone in charge of them who tells them they have to become a Black Belt if they want to stay, and fires the bottom 10 percent...well, it's only a matter of time before a lot of these people pulled 15 red beads, and ended up on the street. And the premier bullet on their resumes? "GE Black Belt." So, Rule 4 - we end up with the blind training the blind, and then those people end up training othere...
Then the consulting world discovered Lean Thinking, and because you didn't need stats, we now had a simpler approach to (if not better quality) efficiency. Don't get me wrong...I'm not against the principles in the TPS, but they were part of a total systems approach at Toyota, and have become something else you can do. So I started hearing a lot of competitive nonsense between Lean and Six Sigma consultants, none of whom had ever learned anything about Quality, really, and didn't understand how silly their arguments sounded.
So, glad to talk more, but I'm tired (just finished my last round of Chemo), and realize I've been on the stump long enough. Let's catch up sometime!
Best regards (and Season's Greatings) to all,
Rip Stauffer
Thanks for such a heartfelt reply, Rip!
And, yup, we still disagree about the red bead experiment...
But, then again, there are COMPETENT demonstrators who KNOW how to follow-up to get RESULTS. Methinks you qualify...
:-)
Your history is useful. Quality is stuck atop Mount Stupid...and all its vested interests.
Care to start a "13th clown" club with me?
Let's do catch up soon (sorry to hear about the state of your health -- sending stealth healing "vibes" your way!)
ALL the best for 2020,
Davis
When it comes to execs, there is no "teaching"...
Thank you for reading and for your kind comments.
I understand that Deming evolved to see that the 14 Points were actually manifestations of the deeper THEORY he eventually formulated -- such is the nature of empirical development. But if it took him that long, why should we expect execs (of all people, with their famous lack of attention spans) to understand it immediately, never mind get past a label they perceive as too pretentious for words? As soon as the words "profound knowledge" come out of your mouth in a roomful of execs, you will be thrown out on your ear (from my experiences 30 years ago -- there were several):
:-)
What is needed are COMPETENT Deming practitioners (not "bible thumpers") who know how to:
1. QUIETLY, and without fanfare, get RESULTS that move "the numbers that make the execs sweat" (easier than you might think):
https://www.qualitydigest.com/inside/management-article/it-time-self-ch…
2. put a stop to "silly meetings" like this (will yield incredible cultural respect):
https://www.qualitydigest.com/inside/management-column/quarterly-review…
3. "make a silk purse out of a sow's ear" (i.e., show how to get RESULTS) when faced with routine, everyday data meetings who use "analysis" techniques such as these:
https://www.qualitydigest.com/inside/statistics-column/vital-deming-les…
Logic + Humans = Change? Think again! Attention deficit execs want RESULTS
You don't need my endorsement
You don't need my endorsement and patronising ; this is an excellent article .
Only , I believe that Dr. Juran did admonish the narrow focus on stamping out fires , he did say 'Make no small plans' . People just chose to take the way way out .
Thank you, Balaji
I am indebted to Dr. Juran's wonderful book "Managerial Breakthrough" for a treasure trove of everyday wisdom! However, he insisted on a "bolt-on" approach to the status quo that formally set up an additional arm known as "Quality" in an organization that, in most cases, sank under the weight of its required excruciating formality. He accepted "confusion, conflict, complexity, and chaos" as necessary evils to work around, but Dr. Deming was adamant about eradicating their pervasive influence, which many saw as a fool's errand.
Not if top management is truly and passionately committed to excellence and not just "pretty good, 'above average' mediocrity"...
All the best to you and your Deming efforts in India. I'm afraid it's too late for the USA...and healthcare. Too many efforts remain entrenched atop Mount Stupid.
Davis
Davis, Deming and Quality
On every corridor in edison'slab in newjersey there is a framed quote by Reynolds: "There is no expedient to which a man will not resort to avoid the real labour of thinking".
Deming (and Davis) want us to think. Tricky business.
In the age of big data and analytics, quaity nees to move on and treat information quality. This is the natural path to take that would keep quaity relevant. A time stamped path of the evoluation of quality is presented in https://www.linkedin.com/pulse/evolution-quality-from-product-information-ron-s-kenett/?fbclid=IwAR1TiZqU2E3DltOXg9-GiaAQPaMKrgAy7RM_c4tLe6tCLItzBwpM1QrJqrE
Also the role of the leader of statistical methods envisaged by Deming evovled. It is now the Chief Information Officer or the top data scientist in an organisation.
These topics (Information Quality and The Real of Work of Data Science) are discussed in:
[following books are co-authored by poster -- QD]
https://www.wiley.com/en-us/Information+Quality%3A+The+Potential+of+Dat…
https://www.wiley.com/en-us/The+Real+Work+of+Data+Science%3A+Turning+da…
Astute comments, as always, Ron
This other QD article of mine also addresses these concerns of yours regarding "Big Data":
https://www.qualitydigest.com/inside/statistics-column/watch-out-big-da…
I'm so glad there are tenacious "data scientists" like you!
Thank you and ALL the best,
Davis
Today's Healthcare Q.I. Déjà vu Continuing to Repeat Same Errors
Davis,
This is the best article I've read in at least two years. The sad reality: Those who need to understand your words here have no understanding of what Deming tried to teach us, and have a short term thinking of quick qains that we have done over, and over, and over again remaining in a quicksand of Q.I. with nothing sustainable and overdependance on statistics they do not even understand yet purchase powerful software to justify their repeated actions of generations before us. They cannot grasp what needs to be changed first: CULTURE!
I love this. It's like you were talking right out of my own mind! You have articulated the current state of Healthcare perfectly!
I'll do my best to translate this to my peers in a Politically Correct way.
Call me sometime soon.
Hope you are doing well.
Best regards,
Gary
Good to hear from you, Gary!
Sounds like you're still fighting the same battles as when we first met (and we know how that turned out!)?
Politically Correct isn't a strength of mine...but I can at least look at myself in the mirror in the morning. Let's just say I ain't getting rich.
:-)
Healthcare is indeed hopeless: vague solutions to vague problems yield vague results...and that includes its current fad du jour of shouting "Joy in work!" from the rooftops.
I'd love to catch up. Sorry we never got that chance to do more work together.
ALL the best,
Davis
The Sad Reality of Quality Today
Hi David.
I have a copy of the ASQ JUSE Tokyo Confeence from 1978. One speaker was Dr W Edwards Deming on his "25 Points for Administration".
It was as we know not distilled to his popularised "14 Points for Management" until the 1980's.
Dr Ishikawa's book on Introduction to Quality Control and J Akao's Hoshin Kanri provides similar historical perspectives on Dr Deming from 1950-53 and how JUSE had to invite Dr JM Juran in 1954 to rectify "these [3] problems Dr Deming caused" from 1954 and again in 1960.
All the best for Christmas and a great 2020. I enjoy your writing.
Mike
Thank you for your kind words...
...and interesting tidbits about Dr. Deming. Am I missing something? Dr. Juran was called in to clean-up after Deming? :-)
What were the three problems Dr. Deming caused?
All the best to you for 2020,
Davis
The Sad Reality of Quality Today
Yes read - "Dr Ishikawa's book on Introduction to Quality Control". It is sobering to read as history repeats itself.
Mike
Japan
Juran wrote a book A History of Managing for Quality His chapter on Japan was written by Nonakata. His perspectives on the issue... ishikawa wrote Deming lectures were enlightening. Juran was brought in to broaden the perspective from statistical to more comprehensive approach. His perspective was that Demings approach led to an over emphasis on statistics(problem 1). And management not having a lot of emphasis on total quality control (Problem 3). It was Ishkawa,s perspective. The chapter summary was interesting as he writes the Japanese would have achieved world quality leadership without Deming or Juran. He points both gave seminars in US was limited in success. His summary was Japanese leadership was driven by being destroyed by the war and a need to overcome the reputation for shoddy products. The Japanese also had National continued education bringing in gurus regularly by JUSE, radio programs given to mid level managers...This contradicts Ishkawa's problem 3. He then points out that both Deming and Juran were sowing seeds in soil ready for growing. They were catalysts. Recall this is the book Juran edited ... My view...What happened in Japan was multifaceted.. However the point all agree on was it requires management knowledge of quality and continuity of purpose... This ties in nicely with Davis's brilliant article about bolt on quality versus a comprehensive system approach to quality. Davis you are so smart. Deming evolved and learned after the 1950s and by the 1980s provides a firm starting point for organizations and Davis' article is the fired starting gun. The question is will it be heard by the runners who are facing the wrong way and will Kenneth Hopper be correct in saying "Deming was a kind of protestent Don Quixote who broke his lance of quality on the heavily fortified windmill of stockholder value..."with me adding or next quarters earnings.
Thank you for this clarifying insight...
...and your very kind comments.
Davis
Add new comment