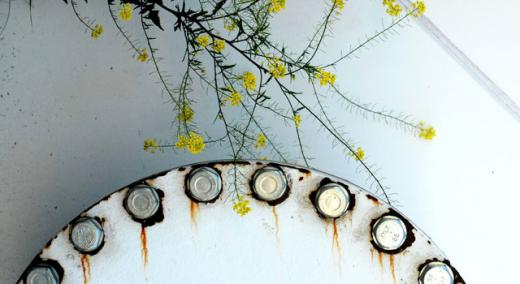
The Automotive Industry Action Group’s (AIAG’s) and German Association of the Automotive Industry’s (VDA’s) new Failure Mode and Effects Analysis Handbook (AIAG, 2019) offers significant advances over FMEA as practiced 15 or 20 years ago.1 The publication is definitely worth buying because the new approach includes valuable methodology; this article will cover the most important points and highlights.
ADVERTISEMENT |
New features
The new process is qualitative rather than quantitative, which overcomes a major drawback of the previous approach. The older occurrence ratings were based on the probability of a failure, and the older AIAG manuals even tabulated recommended nonconforming fraction ranges. If, for example, the failure was 50 percent or more likely, the occurrence rating was 10 (worst possible on a 1 to 10 scale), while one or fewer per 1.5 million opportunities earned a rating of 1. These probabilities can be estimated from a process capability study, assuming that one is available; otherwise, one might easily have to guess.
…
Comments
The AIAG VDA Method Is Fundamentally Flawed
--> Fundamental Flaw of AIAG VDA FMEA Methodolgy
The AIAG VDA FMEA Methodology uses Structure, Function and Failure Analysis to populate the DFMEA and PFMEA. The combination of the Structure, Function and Failure Analysis form a Fault Tree. Since the methodology uses the Structure, Function and Failure Analysis to populate the DFMEA and PFMEA, the methodology makes the fundamental mistake of equating a Fault Tree with a FMEA. In a Fault Tree, the only root causes of failure are the last leaves on the tree. In a properly constructed DFMEA or PFMEA all failure causes must be root causes.
--> The Core AIAG VDA FMEA Methodology is Over 30 Years Old and Software Driven
The AIAG VDA FMEA methodology represents an adoption of the VDA FMEA methodology whose origin can be traced back to 1988. Peter Rosenbeck was contracted by Siemens AG to develop a failure diagnostic system with fault tree elements for a semi-conductor production process. The software was originally called “Object-FMEA”.
In 1989, Merecedes-Benz AG, BMW AG and Siemens AG partnered with Mr. Rosenbeck to further develop “Object-FMEA”. In 1992, “APIS IQFMEA” was released. Daimler-Benz Interservices (debis), an internal services arm of Diamler-Benz AG, was named distributor of the software. They would continue in the role until 1996. In 1996 the VDA FMEA manual would be published. Jurgen Eilers, Managing Director of APIS, is listed as one of the authors in the manual.
In 1996, Volkswagen acquired a world-wide site license for FMEA software being developed by Plato AG. One might assume the purpose was they did not want to be using a critical software program developed and promoted by a competitor. The two largest FMEA software companies in Europe are currently APIS and Plato. Any doubts why?
And now we have AIAG partnering with the VDA to come up with a handbook that adopts the VDA method. Per AIAG, 80% of the current companies in North America use Excel. The new AIAG VDA FMEA methods will be very difficult if not impossible to implement with Excel. In 2019 the AIAG enters the FMEA software market with software that will support the AIAG VDA FMEA Handbook methodology. Interesting isn’t it?
If you doubt that the AIAG VDA FMEA Handbook FMEA method is driven by software, read Mike Bucala’s comment to my article in Quality Digest titled “The Case Against the AIAG VDA DFMEA” ( https://www.qualitydigest.com/inside/risk-management-column/case-against-aiag-vda-dfmea-013118.html ). Mr. Bucala is an employee of Diamer Trucks North America and member of the AIAG VDA FMEA Handbook committee. In response to my article, Mr. Bucala wrote: “Your article concludes that the team should have started with (Excel-based) AIAG 4th Edition methods, and (by inference) expected the Europeans to modify their software-based methods to conform to it. This in an unrealistic expectation”. Simply put, the Europeans have spent a lot of money on FMEA software and they are not changing.
--> To Learn More About the Weaknesses of the AIAG VDA FMEA Methodology
If you want to learn more about the weaknesses of the AIAG VDA DFMEA and PFMEA methodologies I encourage you to watch a webinar which gave for the ASQ Reliability Division titled “Implementing DFMEAs and PFMEAs Using the New AIAG VDA FMEA Handbook” ( https://www.youtube.com/watch?v=tLaTwKNM7zM). The webinar uses DFMEA and PFMEA examples that are very similar to the DFMEA and PFMEA examples found in the AIAG VDA FMEA Handbook (only difference is type of motor). The webinar shows why the AIAG VDA FMEA methodology will result in more time to create DFMEAs and PFMEAs than the AIAG 4th Edition FMEA method. It also explains why it will be difficult if not impossible to implement with Excel.
Most importantly, the webinar also explains why the DFMEAs and PFMEAs created using the AIAG VDA FMEA methodology are ineffective in managing design and manufacturing risk. If the creators of the handbook cannot create DFMEAs and PFMEAs that are effective if managing risk, how is the reader of the manual supposed to?
If you do PFMEAs and prefer to read why the AIAG VDA PFMEA methodology is inefficient and ineffective in managing risk, see the “The Case Against the AIAG VDA PFMEA” found at https://www.harpcosystems.com/articles/case-against-the-aiag-vda-process-fmea.
Add new comment