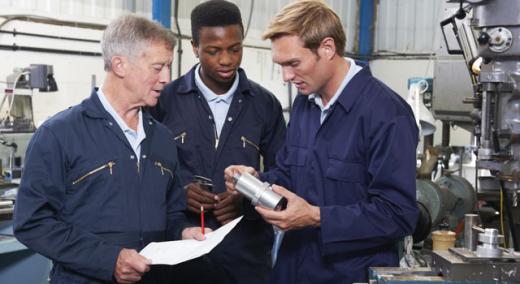
Root cause analysis (RCA) is the process of finding the basic underlying cause for an effect we observe or experience. In the context of failure analysis, RCA is used for finding the root cause of frequent machine malfunctions or a big machine breakdown. But what exactly is RCA, and how is it done?
ADVERTISEMENT |
In this series we take an in-depth look at how to perform RCA: We outline the steps, describe common tools and techniques, and give a couple of practical examples. Let's start by defining what RCA is.
What is root cause analysis (RCA)?
Root cause analysis is the process of tracing causes of an observable problem and identifying the basic underlying issue that was causing it. Fixing the identified basic problem should stop the recurrence of other problems that originated due to it.
If the problem fixed is not the underlying cause, there is no guarantee that the same fault will not occur again. RCA tries to follow the chain of cause and effects to pinpoint the problem that, when eliminated, makes all the other faults disappear.
…
Comments
Root Cause Analysis
I worked for a number of years as QA Manager for a plant making non-woven fabrics from polypropylene. A big market was for use in baby diapers. A customer in Japan complained that our rolls of fabric were non-uniform, being streaky with lanes thin and thick. The thin lanes leaked glue in converting forcing line outages for cleanup.
Our manager's RCA method was to call department heads together, solicit ideas as to cause, vote to rank them in terms of probability, then retire to his office to call the customer. The advantage of this method is showing rapid response to a customer complaint.
The solution selected was to install a "randomizer' which moved our fabric stream back and forth about six inches across the width of the machine. The result were rolls of fabric which appeared even with no hills or valleys.
An engineer friend and I were skeptical of this "solution" and wondered how long it would take the clever Japanese engineers to discover how they had been tricked into believeing we had fixed the problem. Our solution was to monitor the stream of fabric across its width to ensure even distribution. Took longer but was more effective.
When we started using a few control charts, this same manager was quick to want analysis when a process went out of control in a "bad for the customer" direction, but saw no reason to find the source of an out of control signal in a "benefit to the customer" direction.
Enjoyed your article
RCA and Healthcare
I work in Patient Safety and we use RCA techniques all the time to look at events that affect patient care. We also use RCA techniques for what might be called proactive risk assessments (PRA). While aviation and nuclear industries have matured the use of root cause analyses, healthcare is still working on making this mainstream and part of a just culture so it is not seen as punitive.
RCA
Great read!
I have worked and used RCA methods in the Automotive, Oil & Gas, Non-Profit, and now in the Construction industry(*sighs*). Construction has been the most difficult to get others to Want to understand why the same errors happen or the same required tasks get forgotten, project-after-project-after-project(*sighs again!*)
But I am persistent and it always comes down to managing People! Thanks, CS
Add new comment