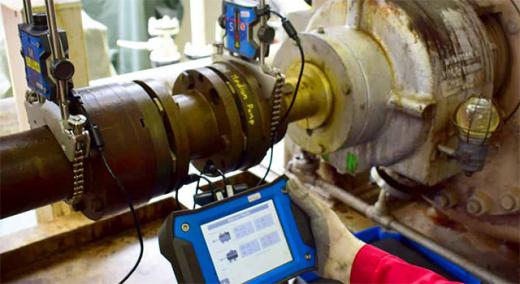
Learning from past failures is the best way to understand and prevent future equipment breakdowns. In practice, that learning process falls under the umbrella of failure analysis.
ADVERTISEMENT |
These days, there are plenty of failure analysis techniques to choose from. They all come with a specific set of advantages, challenges, and use cases. Let’s see what is available, what steps you need to take, and what are the right techniques for your situation.
What is failure analysis?
Failure analysis is the process of collecting and analyzing failure data, usually to identify the root cause of an asset malfunction or breakdown. This information can be used to improve machine and component design, adjust maintenance schedules, and improve maintenance processes. Ultimately, its goal is to improve asset reliability.
…
Comments
Failure Analysis - -misuse of 5-Why Analysis
The 5-Why Analysis is to be applied against the Direct or highest ranked or as Toyota say PoC. See Toyota Practical Problem Solving seven steps. The way you have done the 5-Why before the Ishikawa Type A C&E Diagram is incorrect. Toyota and Industrial Engineering, Work Simplification and AIAG FMEA do not do as your say. 5-Why is in support of the Ishikawa Diagrams and Dr Ishikawa has three types of C&E Diagrams.
Add new comment