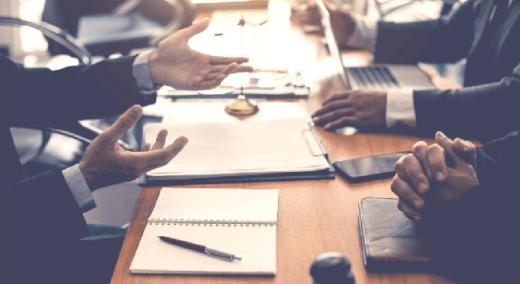
It’s a conundrum that faces everyone who operates a manufacturing or service business: Most are unaware of the dire consequences of a defect reaching a customer until a process server hands them a lawsuit. By then it’s too late. Regardless of the outcome, the people and businesses will be permanently scarred and damaged.
ADVERTISEMENT |
Most of the more than 700 companies I’ve worked with during the last 50 years have robust customer service and warranty processes that never address the question: What might be the dire consequences of a defect reaching one of our customers?
During the last two decades, I’ve expanded my quality management consulting work to include consulting and testifying in products liability and organizational negligence cases. In more than 40 lawsuits, I’ve gathered empirical evidence which concludes that our fundamental tenets of quality management are seriously flawed. Our charter has been to minimize process variability and reduce defects to an acceptable level. Both canards are folly.
…
Comments
FMEA can help prioritize
I am not sure it is practical to ensure that no defect (regardless of how minor) ever reaches a customer, but failure mode effects analysis (FMEA) would probably assign a severity level of 10 (worst possible) to the defect in the space heater's switch as the failure effect is to start a fire that endangers human life. This is in fact something that must never be allowed to reach a customer just like a failure mode that causes a vehicle's brakes or steering to fail.
FMEA addresses a couple of other important issues. "What might be the dire consequences of a defect reaching one of our customers?" This is reflected by the severity rating, with 9 and 10 generally reserved for dangers to life and safety, or noncompliance with a government regulation. A failure mode that caused a car's brakes or steering to fail would get a 10 severity rating. My position is that feedback from warranty claims should be reviewed in the context of the design or process FMEA for the product in question--that is, if failures are happening, then the responsible failure modes need to be added to the FMEA.
As to ensuring that defects do not reach an internal or external customer, FMEA relates the detection rating of 1 to 10, with 10 being the worst possible, to the detection controls (such as a go/no-go gage) that are supposed to detect poor quality before they leave their place of origin. Failure of the detection controls to do this is the escape root cause. The occurrence rating of 1 to 10 is based on the prevention controls whose purpose is to prevent creation of the defect in the first place. Their failure to do so is the occurrence root cause. This, in turn, relates AIAG's Effective Problem Solving process (which considers escape and occurrence root causes) directly to FMEA for which the AIAG/VDA manual is an outstanding reference. I think companies could stay out of the most of the trouble this article describes if they used it diligently.
(Does not constitute formal engineering advice.)
Risk Prioritization
The article is particularly firey (likely the point to help wake people up). However, the notion of preventing every foreseeable risk is a fallacy. Risk mitigation must be relative to the risk. Human life and safety must never be compromised (FEMA 9 and 10) and would require all available means to mitigate the risk. Whereas a cosmetic issue may be allowed if the mitigation is overly burdensome. This is the explicit requirement of ISO 9001, "Actions taken to address risks shall be proportionate to the potential impact..."
Agreed that the FMEA tool is perfectly suited for this task of prioritizing. Good RCA on warranty claims, product returns, and internal defects are also tools that will help reduce failures thereby mitigating their risk.
Add new comment