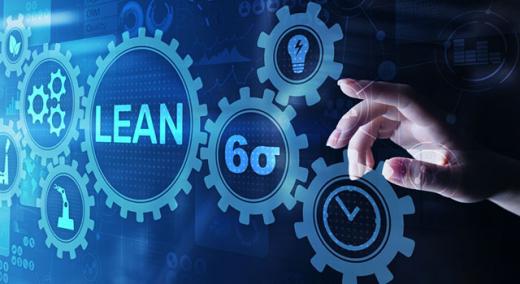
The manufacturing world, across industry sectors, has witnessed significant improvements in productivity and competitiveness during the past couple of decades as a result of continuous improvement (CI) methodologies. Two of these methodologies that are recognized as having broad applicability are lean manufacturing and Six Sigma.
ADVERTISEMENT |
In fact, some practitioners have combined these CI philosophies and tool sets into lean Six Sigma. Many smaller and medium-sized manufacturers (SMMs) have learned that making the organizational commitment to master the concepts of lean and Six Sigma methodologies can transform their business, leading to improvements in safety, quality, delivery, and cost.
By mastering lean and Six Sigma methodologies, SMMs can create a more efficient and sustainable business, and drastically improve their top and bottom lines.
…
Comments
What Are Laen and Six Sigma?
Why would an organization commited to Lean require Six Sigma. It would seem redundant.
In your point 3 - Improving flow, you don't mention that Lean organizations incorporate TQM (quality at the source) which is a major factor in increasing flow.
Also, point 5 - Seeking Perfection suggests to me the target is zero defects. Not 3.4 per million.
Your thoughts?
Six Sigma Eliminates Defects and Deviation
Lean Accelerates Speed by eliminating delays.
Six Sigma eliminates the remaining defects and deviation.
You need both Lean and Six Sigma. (And you will need innovation to keep from becoming obsolete.)
Why not zero defects?
How many defects, mistakes and errors do you want in your healthcare? The Institute for Healthcare Improvement (www.ihi.org) estimates that one patient out of every two suffers some form of preventable harm. The IHI also estimates that out of a $3 trillion dollar healthcare spend, $1 trillion is waste.
Healthcare has a Zero Harm initiative to achieve zero defects.
I have proposed a Trillion Dollar Prescription to help healthcare cut costs by $500 billion by 2025.
Lean is not just speed
This tired trope about Lean being about speed is still incorrect.
Where does Toyota say TPS is only about speed? Nowhere.
TPS (and Lean) are about flow and quality at the source.
Carving out (or implying) that Six Sigma is the only method for reducing defects is incorrect and insulting to Toyota, a company that doesn't use Six Sigma in manufacturing, but manages to produce world-class quality.
Toyota has been exceptional for a long time
Toyota started long before "Lean Six Sigma" even existed. Their culture makes the magic.
Trying to start being Toyota is not possible for service industries, because they don't have decades of foundation to support it.
You cannot get to the end state instantly. You have to start somewhere and build the mindset and processes to achieve it.
Using the tools of Lean Six Sigma can start you down the road, but it takes perserverance to get anywhere near Toyota.
Lean for Service Industries
In service industries, most of the "waste" involves delays between steps in a process (e.g., how long does a patient have to wait to see a doctor?)
I call this the 3-57 Rule: employees are working on product or service for only 3 minutes out of every hour, leaving 57 minutes of delay. Trying to speed up your people (e.g., doctors and nurses in healthcare) will only impact a minute or two out of every hour.
The 15-2-20 Rule says that for every 15 minutes of delay eliminated, you will double (2) productivity and increase profits by 20%.
Eliminating delays also reduces defects by 50%.
In manufacturing, most of the delays have been eliminated on the factory floor, but the service delays (ordering, invoicing, purchasing, scheduling, etc.) still remain.
In any flowchart or value stream map, focus on the arrows between steps, not on the steps themselves.
Make your product faster, not your people.
Six Sigma farce
Your claim "To achieve a Six Sigma conformance, a process must not produce more than 3.4 defects per million opportunities." is pure farce.
Six Sigma started with Mr Bill Smith and his out-of-control molding process that happened to drift “as much as 1.5 sigma”. Smith’s buddy, con man Harry, “proved” Smith disaster happened for every process ... based on the height of a stack of discs! Most folk never bothered to check. https://www.youtube.com/watch?v=0kZbJLHK_4M
A long term study of hundreds of Six Sigma projects at Ford showed an average of 1 in 5 parts defective AFTER improvement for “successful” Six Sigma projects.
Six Sigma's creator said: “Some claim that Six Sigma is nothing more than smoke and mirrors - a sales job for senior management and a snow job for the rest. Well, they couldn't be more on target."
Counting defects is the 1870 approach to quality. Defect relate to the specification, NOT the process.
Add new comment