All Features
Kevin Meyer
Nearly three decades ago, one of my first bosses pulled me aside. I forget the underlying incident except that I had somehow screwed up, and he bluntly told me to “sweat the details.” I clearly remember it to this day, and it became one of the defining pieces of advice I have ever received. It was…
Bruce Hamilton
Last weekend in the Nantucket Ferry terminal, I passed a defunct phone booth: an ornate wooden kiosk used 20 years ago to frame a pay phone, provide a modicum of privacy, and hold a phone book. It appeared that this particular phone booth had been re-purposed to hold a suggestion box, or perhaps…
Jim Benson
Prioritization is stressful. We find ourselves prematurely making value decisions about what to pull and when (right now!).
Recently a client asked, “How can I prioritize my work when there is no clear priority? Everything seems equally important.”
This is a deeper issue than simply being…
Annette Franz
Last month, I wrote about the concept of lean management and what that means not only for your company but also for your customers.
If company leadership wants to transform the culture of the organization and become a lean company, they’ve first got to understand what comprises lean leadership,…
Harish Jose
Uncertainty is all around us. A lean leader’s main purpose is to develop people so they can tackle uncertainty. There are two ways to tackle uncertainty: One is genchi genbutsu (go and see, or seeing for yourself), and the other is to employ the plan-do-check-act (PDCA) cycle, a method for…
Barbara A. Cleary
In a rapidly changing business environment, it’s sometimes hard just to keep up with everyday demands—never mind having time to develop new and better approaches to changing requirements, needs, or markets. Staying ahead of the curve sounds as if it might demand working longer hours, hiring more…
William A. Levinson
ISO 9001:2015 clause 4.2—“Understanding the needs and expectations of interested parties” requires the organization to determine the “requirements of these interested parties that are relevant to the quality management system.” The recent two-day conflict that Facebook lost to F.B. (Fluff Busting…
Bruce Hamilton
A friend and colleague remarked to me that “the lean market has become mature,” implying a depth and breadth of lean understanding in industry that I have rarely seen myself.
Standardized work, for example, almost always looks like time setting to me, an occasional and cursory exercise by…
Peter J. Sherman
As organizations become successful and grow, uncertainty is generally the enemy. Thriving organizations seek to eliminate variation and increase efficiency. They identify best practices and policies, and design standard operating procedures. Such efforts can make a business wildly efficient at…
Kevin Meyer
As I was researching the remarkable similarities between lean and Zen for my book, The Simple Leader (Gemba Academy, 2016) one of the most interesting—and meaningful—was the concept of the beginner’s mind.
Taiichi Ohno said, “Observe… without preconceptions and with a blank mind.”
Zen master…
Afaq Ahmed, Yves Van Nuland
New technologies have empowered customers to seek out the best products and services at the lowest cost and shortest delivery times. Customers can compare price and delivery information as well as reviews about product quality. Thus, the importance of sustaining outstanding quality in order to…
Steve Garbrecht
Here’s a stat that might surprise you—according to LNS Research, 50 percent of manufacturers have implemented or will be implementing cross-functional groups to support their operational excellence journeys within a year. At the same time, only 18 percent have software or processes in place to…
Harish Jose
Today I’d like to take a look at a lesson from Taiichi Ohno regarding the pursuit of quality. His comment, “The pursuit of quantity cultivates waste, while the pursuit of quality yields value,” struck a chord with me. Among other things, he's referring to the importance of resisting mass-…
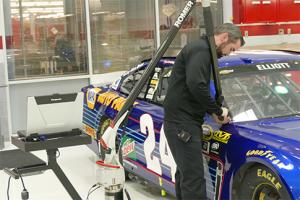
Eugene Daniell
Sponsored Content
For more than 30 years, Hendrick Motorsports has consistently been one of NASCAR’s most successful teams. In the course of winning a record 11 Sprint Cup Series championships, Hendrick Motorsports has learned that it must innovate constantly to stay ahead of the competition.…
Heinz Schandl
The world is using its natural resources at an ever-increasing rate. Worldwide, annual extraction of primary materials—biomass, fossil fuels, metal ores, and minerals—tripled between 1970 and 2010. People in the richest countries now consume up to 10 times more resources than those in the poorest…
Bruce Hamilton
Early along, as a student of the Toyota Production System (TPS), now referred to as lean, I struggled with some of the concepts and systems. For example, Shigeo Shingo’s claim that a four-hour machine setup could be reduced to less than 10 minutes made me a skeptic.
“Perhaps, when Mr. Shingo…
Annette Franz
I recently came across the Japanese terms genchi genbutsu and gemba; they’re both key principles of the Toyota Production System, which comprises Toyota’s management philosophy and best practices. Although they’re (lean) management principles and concepts, they apply not only to the employee…
Jason Furness
For the sake of argument, let’s say you’re aware of an issue that’s holding your enterprise performance back, and you know what to do about it. At that point, there are seven key actions you can take to rapidly implement change, which in turn will allow you to respond to market changes with short…
Kevin Meyer
Few people realize how employee policy manuals, usually given to you on your first day and then mostly forgotten, shape an organization’s culture and thereby its fundamental performance.
To give you a reference point, one company I worked for had an employee manual of 40+ pages. Every section…
Gwendolyn Galsworth
Does lean have a clearly delineated limit? When a company starts out on that path, should it expect an endpoint, a completion, an arrival? Is it a forever commitment, or is it a bounded outcome that companies can achieve and then move on? In short, is lean a destination or a process?
These aren't…
William A. Levinson
Masaaki Imai, author of Gemba Kaizen (McGraw-Hill Education, 1997), introduced the concept of the value-adding “bang,” the exact moment at which a process adds value for the customer. He meant the moment at which an official stamped a document, but the same concept applies when a stamping or…
Mark Graban
Given all of the problems that exist in our American healthcare system, it’s encouraging that most healthcare organizations are endorsing or practicing some form of process improvement or operational excellence strategy. Under the banner of different labels and using different combinations of…
Harish Jose
There is a concept in lean known as a “monument.” It refers to a large machine, piece of equipment, or something similar that can’t be changed right away, and so you have to plan your processes around it. This generally impedes the flow and frequently becomes a hindrance to lean initiatives. A…
Bruce Hamilton
I wrote a piece a little more than five years ago about a variety reduction program (VRP), an amazing but little-known product-design optimization tool. At the time I referred to VRP as an idea whose “time had not yet come.” Last week, as I gave a short presentation on VRP, I realized that five…
Bruce Hamilton
Many moons ago, when I was just getting started on my lean journey, I visited a large automotive supplier to benchmark pull systems. My own factory had started a pilot kanban between two work centers and I was hoping to gain some insight from a more experienced source.
To my disappointment, when…