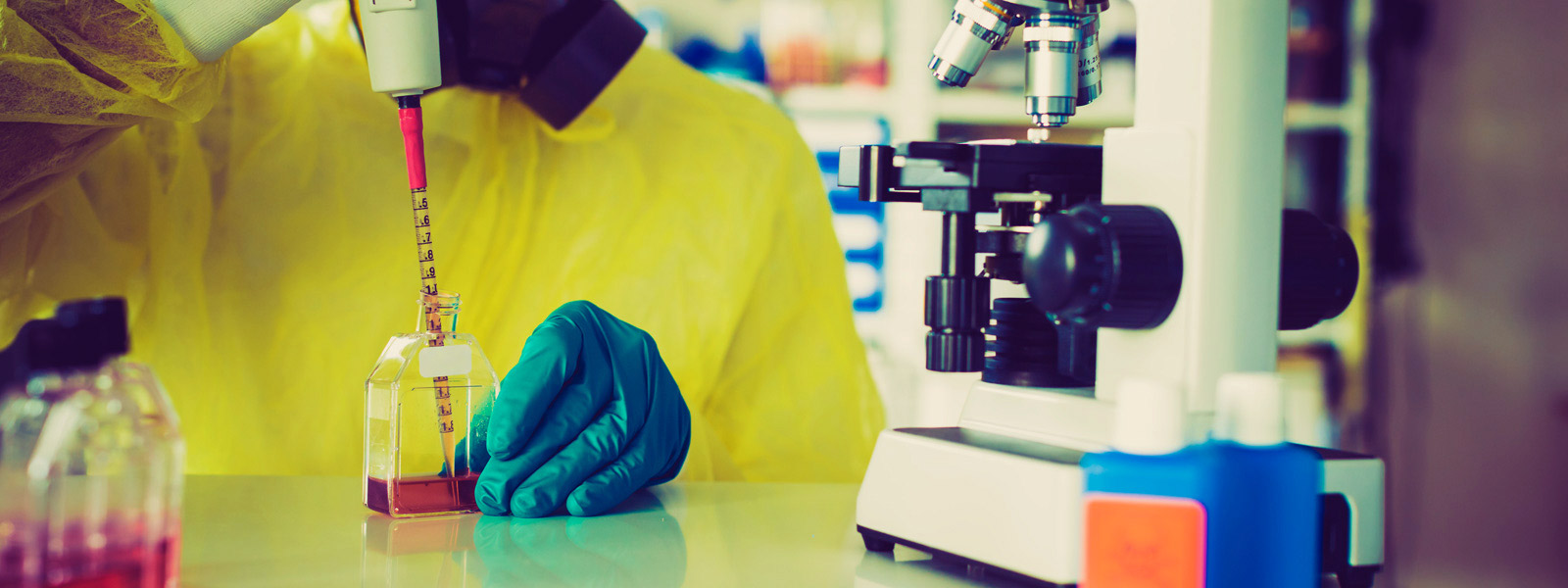
Great quality is pretty much the same everywhere, but the cost of poor quality is not equivalent from industry to industry. For example, it’s conceivable (but I hope not probable) that this article may turn out to be a real bomb, or worse, a complete snoozer. What’s the cost of that poor quality? To you, the reader, it will likely mean little except some lost time. For me, as the writer, the reputational hit could be considerable. To Quality Digest, as the publisher of the piece, the fallout could be even worse—lost readers and advertisers.
Now consider the risks of poor quality for a company operating within the life sciences sector. For these organizations, poor quality can lead to deadly outcomes for customers. That’s why U.S. Food and Drug Administration (FDA) agents won’t hesitate to shut down organizations that have been warned about faulty procedures and bad quality but can’t or won’t correct the situation.
Compliance to FDA regulations is not optional for life science companies, and that’s a good thing. That absolute level of adherence does more than keep the FDA from closing manufacturing operations or even entire companies. The FDA also helps to ensure our safety as it regards to the things we eat and drink, or that doctors prescribe, inject, and implant. Complying with both the letter as well as the spirit of FDA requirements is the surest way to drive quality outcomes that benefit stakeholders both in and out of the organization.
Best practices
Great companies in this space understand the value of compliance in generating quality. They also, as it happens, value discretion and are notably protective of their proprietary processes.
There are no silver bullets or secret ingredients to quality or compliance... there is only hard work, persistence, and the commitment to one’s customers... |
With this in mind, I recently spoke to a senior manager of quality assurance at a clinical-stage biopharmaceutical company focused on developing novel cell and gene therapies. My contact gave me some great insights, but on condition that I not name any names.
This life science manufacturer currently has a handful of therapeutic products in the clinical-phase pipeline and moving toward commercialization. Therefore, the company’s management team is intimately involved with quality best practices around research and development, and ultimately, testing and regulatory approvals.
“We’re really looking to support the clinical manufacturing of those products,” notes my source. “We understand the build of our quality system, starting with Quality by Design. Developing products and processes is really something that we're very focused on right now.”
So how exactly does compliance lead to quality? How are the two different, and how are they similar? I was given good, practical insights into how compliance and quality work together.
“In my experience, quality has typically been the what and the how,” says my contact. “It’s how you do something or how something needs to be accomplished or achieved—a quality system, really. It can be a real enabler to profit your cycle times depending on what type of product you're manufacturing. We have one therapy that is an autologous product. In that instance, developing quality systems that enable quick cycle times is important because we don't have the luxury of, say, a 90-day batch record review and release process with that type of product. You need a very specific quality system enabler to handle a more rapid cycle.
“Compliance, on the other hand, is really educating the organization on why we do the things we do. It’s about managing the best way to achieve a quality product. From a compliance perspective, the FDA is looking to see that we can provide a product that is safe, of a high quality, and of a high purity and potency. Ultimately, the quality systems and processes that we have in place are those that allow us to comply with those requirements from the FDA. So that's where I see the differences, and the overlap, between quality and compliance.”
How to avoid a compliance black holeIt has sometimes been said about high-risk ventures that “failure is not an option.” However, failure is always an option, and in fact it happens all the time, especially in innovative, heavily research-dependent industries such as the life sciences. Because of this reality, regulatory oversight exists to ensure that potentially harmful products are stopped before they reach consumers, and that the processes leading to that failure are corrected within the manufacturer’s operation so that improvement and innovation are permitted to march forward as safely as possible. History is rife with examples of organizations that ran afoul of the regulators and suffered the consequences. The commonality is evasiveness toward inspectors, even to the point of malfeasance. A recent example that leaps out is that of Theranos, the blood-testing company lead by Elizabeth Holmes. After lots of empty promises about the efficacy of its testing systems and fawning press about the company and Holmes, it turned out that Theranos had misled inspectors about its technology and lied to investors about the state of the company’s finances. A criminal indictment of Holmes and former Theranos president Sunny Balwani is currently pending in a federal court. Late in 2016, about the same time that Theranos was laying off large portions of its workforce due to ongoing regulatory violations, a pharmaceutical manufacturer named Insys Therapeutics was running into trouble as well. Several members of the company’s leadership, including founder John Kapoor and CEO Michael Babich, were accused of fraud, bribery, and conspiracy in connection with efforts to get doctors to prescribe, and insurers to cover, their product Subsys, which is the opioid fentanyl delivered in a sublingual spray. Another notable case occurred in 2005, when four members of the quality team at pharma company Able Labs were found to be manipulating laboratory data in an attempt to gain approval for a new drug. The four were debarred for five years, and Able Labs itself soon went into bankruptcy and eventually sold off its assets. Avoiding the fate that befell these organizations, not to mention their managers and executives, requires a commitment to transparency and a process-based approach to continuous improvement. Following are some tips for avoiding the gravitational force of a compliance black hole: Don’t be a criminal. This one is self-explanatory, and it is good advice for anyone, anywhere. Crime doesn’t pay, period. Have a robust quality management system. A QMS that is rigorously examined on a regular basis, both by internal as well as external auditors, provides the ability to understand where your R&D, manufacturing, packaging, or other processes may be flawed. When problems are detected, root cause analysis and corrective and preventive actions are your allies. Regulators are not looking for perfection, but they do expect you to find and take prompt and effective action on issues that may arise. Listen to guidance. The FDA does not want life science companies to fail, and the agency is clear in offering insight into its Current Good Manufacturing Practice (CGMP) as well as forthcoming changes in procedure and protocols. The administration’s website is a great place to find information, as are conferences, events, and training from organizations such as the Parenteral Drug Association (PDA). Lean on your partners and colleagues. Life sciences is a competitive industry, but it’s a rather collegial one, too. Reading case studies from others that have strong quality practices in place is invaluable (even if, as in the article accompanying this sidebar, the names of the company and people are redacted). Many others are willing to share their general experiences. Companies providing QMS software can also offer great, practical insight into how to build quality systems that can stand the test of time—not to mention the scrutiny of regulators. |
The role of regulators
The FDA carries a somewhat menacing reputation that, in a sense, is well earned. FDA agents do carry badges and guns, along with the power to bring financial ruin to companies and significant legal jeopardy to executives and managers (see sidebar).
Of course, all this is necessary because the most important role of that administration is to protect us, the consumers of food, drink, pharmaceuticals, and medical devices made or sold in the United States. What’s sometimes less understood is the fact that the FDA protects life science manufacturers, too. Without this necessary oversight, and the framework of internal excellence it demands, companies in this space would not be as successful as they are.
Again, my contact provided an interesting perspective: “The FDA is ultimately responsible to consumers to ensure the safety and effectiveness of products. They also really collaborate very well with industry because they want us to be successful. At the end of the day, shutting down a facility that may be a single-source manufacturer for a chemotherapy drug might not be in the best interests of the American people, and so the FDA works very closely with industry.”
Warning letters and consent decrees are issued if significant flaws are discovered in a company’s quality processes, and those actions are serious indeed. But the vastly more significant step of shutting down production is rarer. Being mindful that direct dangers to the health and safety of the public are always given utmost priority, short of those actual threats, the FDA is generally more collaborative than adversarial in nature.
“The FDA wants to help manufacturers better understand how to have robust manufacturing processes and robust quality systems that achieve the goal of compliance but also are sustainable,” says my contact. “When it comes to questions like, ‘How do you really get product from the clinical realm into the commercial space?’ there is a collaboration that happens between a manufacturer’s regulatory team and the FDA. I see the FDA as helping to ensure that we're doing what we need to do and that they are offering guidance, in a very transparent way, so that we can be successful.”
Making it work
If quality is the “what” and the “how,” and compliance is the “why,” then the bigger questions are where the hand-off between the two occurs and when you know you’re doing it right.
There are no silver bullets or secret ingredients to quality or compliance, especially within this sector; there is only hard work, persistence, and the commitment to one’s customers to provide therapies that function safely and effectively.
To make compliance work as a driver of world-class quality, a manufacturer of life science products must be willing and able to understand the goal before constructing a framework to achieve that goal. And, tempting as it may be to consider the goal as only the approval of a given drug or therapy, it’s broader than that. The overarching ambition is to create a quality management system that all key players in the organization can draw from and contribute to. Such a system should be easily understandable and yield powerful, specific insights into the reasons for successful outputs. Do it right, and compliance to regulatory requirements is only the first of several significant benefits. Everything else—great public relations, growing market share, and blossoming shareholder value—will naturally follow as a function of outstanding quality.
“I don't want to be simplistic because it isn't simple,” this manager concludes. “But you start by taking a very methodical approach to the basic compliance requirements, and then you work through those processes and gain a better understanding of how they work in your organization, and how they complement your manufacturing processes. That just takes time and practice. You can build any kind of model conceptually until you actually walk through it. Sometimes you learn from failure, but that's not something that anybody is ever necessarily eager to take on. We don’t want to fail. We want to be successful.”
Add new comment