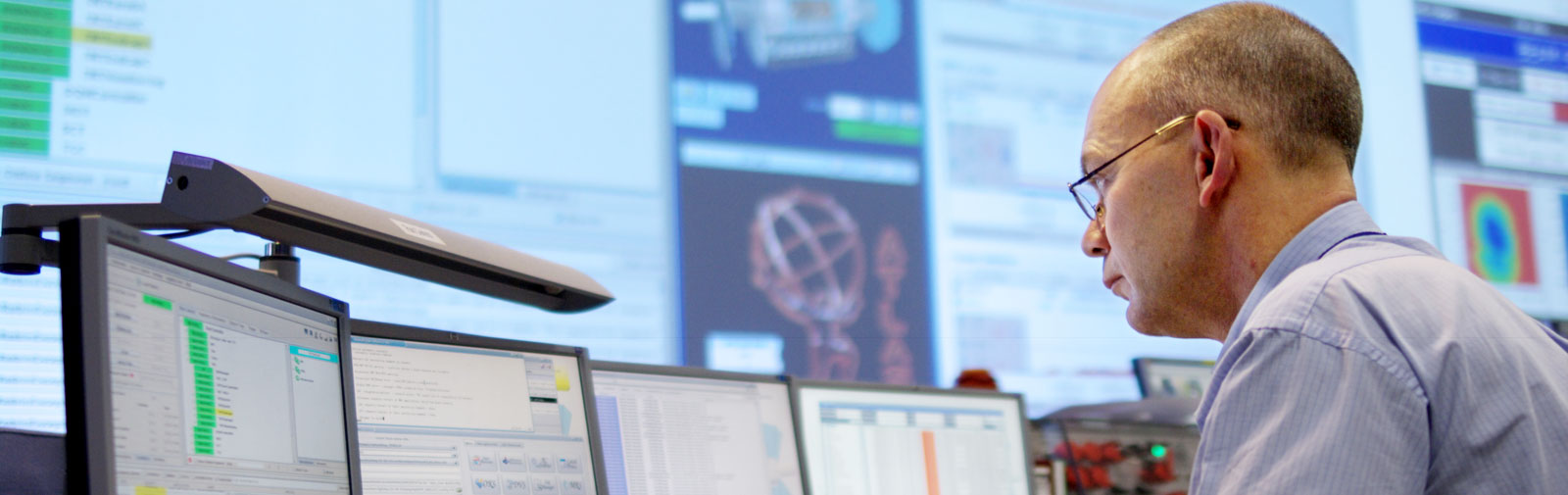
For nearly a century, statistical process control (SPC) has been the cornerstone of quality management and process control. But traditional SPC can’t keep up as the pace of manufacturing accelerates. Twenty-first century manufacturing lines produce multiple products and create thousands of data points in any given minute. Operations, quality, and Six Sigma teams are buried in an avalanche of data that they can’t possibly interpret.
Many organizations find that their teams are consumed by continually monitoring control charts and updating spreadsheets. They don’t have time to try to understand what all that data really mean—or how they can use them to drive meaningful action for their companies.
Even real-time data fall short when they’re siloed in different databases and accessible in only one location. The result is missed opportunities and wasted time as teams search for the details they need to achieve manufacturing optimization across the enterprise.
So how do you monitor what’s happening on the plant floor while it’s happening, without becoming so buried in data that agile analysis and response become impossible? And how do you scale your solution across multiple lines, shifts, and sites?
No. 1: Modernize SPC
Manufacturers must find better ways to leverage SPC in order to:
• Streamline operator efficiency
• Empower direct, timely action on the plant floor
• Enable effective, immediate comparisons and reporting of process output against specifications and control limits
• Aggregate and interpret information to drive strategic, data-based decisions
Modern manufacturing organizations strive to adapt their SPC systems to provide these capabilities. But until recently, it hasn’t been possible bring it all together in a “single pane of glass.” InfinityQS has the solution: the Enact quality intelligence platform.
Enact leverages the real power of SPC. By automating the backend analysis, the platform instantly enables you to interpret quality and process information in clear, intuitive, role-based dashboards. This is still SPC in the truest sense of the word—but a more sophisticated and modern implementation of SPC. All the control charts and details are still there for you when you want to dig deeper. But Enact does the grunt work behind the scenes, surfacing the information that every user needs, when he needs it.
When you are able to see the meaning behind your data—and what actions to take in response to that information—you can truly optimize your manufacturing operations.
No. 2: Implement quality checks at strategic points, not just at final inspection
If you’re waiting to collect quality data until finished products come off the line, your “real-time” data are likely coming too late to do much good in the event of an upstream machine or process problem.
A better approach is to collect data at multiple points along the manufacturing process. This approach enables you to discover trends or issues, and take corrective action before the trouble gets out of hand.
A great way to implement this type of continual data flow is with an SPC solution that uses process models and part recipes. For example, Enact enables you to configure a graphical representation of how products are made (i.e., how inputs are transformed into outputs). These “recipes” are used to produce a specific product and include embedded quality checks during the process.
Figure 1: The process model and part recipes enable you to create a visual map of your process.
Part recipes and process models document all the steps in the production process, along with an array of other valuable information:
• Process name
• Data tags
• Data collection flows and timing
• Specification limits
By checking quality earlier and more frequently, you can use your real-time data to implement real-time solutions.
No. 3: Automate notifications and data collections
Is your company still recording quality checks manually and jotting them down on paper forms? Or are operators expected to keep an eye on the clock so that they know when to make the rounds, testing and recording quality metrics? If you answered “yes” to either question, you could be in trouble.
One way to reduce missed checks is through an SPC solution that makes data collection faster, easier, and more accurate. Enact provides automated notifications to help keep collections on track, enforce best practices, and catch entry errors when they occur.
Figure 2: Automated notifications and collection parameters help to reduce errors or missing information.
Enact can help reduce data collection errors and increase data accuracy by allowing operators to capture data directly from digital measurement devices such as handheld measurement devices or bench-top gauges. Another way to help ensure the most accurate data possible is to use Enact’s optional Automated Data Collection Service. ADC can automatically collect measurement values from a variety of data sources—including gauges and digital devices, flat files, XML files, databases, and OPC servers (for PLC data)—and store them directly in a centralized Enact database.
No. 4: Stop data overload
So now you are ready to collect data from across all of your end-to-end production processes, and to keep it flowing consistently and accurately. But when a manufacturing plant produces thousands of data streams, how do you help users at every level use those data to make improvements in production performance and profit? You need a way to see the “big picture” of what all that quality and operations data are telling you.
To address these needs, the InfinityQS experts—many of whom are Six Sigma Green or Black Belts—applied their decades of statistical and real-world manufacturing and quality experience to design the Enact dashboard.
Figure 3: SPC solutions that filter data can help you avoid data overload.
This role-based interface is made up of data tiles that surface the most important information for any given user at any given time. Enact monitors real-time data streams for processes and collections, prioritized based on the user’s job and shift. Stream summary tiles provide a visual of what’s happening across a line or site, automatically alerting you to anything amiss, as well as enabling you to dig deeper for more details whenever you want.
No. 5: Stay fast but flexible
The next important step in speeding your ability to gather, digest, and act on quality data involves those details. The more analytic power you have, whether on the plant floor or during a review of aggregated data, the easier it becomes to make proactive, strategic decisions that can result in significant cost savings and productivity gains.
All SPC efforts revolve around measuring and observing process variation. Using an embedded real-time SPC analysis engine, Enact processes every subgroup and data value, and warns the user when statistical or specification violations are detected. The operator then has the ability to simply click and explore the underlying data through data visualization tools such as control charts, Pareto charts, and box-and-whisker plots to get to the source of the underlying problem.
Figure 4: Robust solutions surface prioritized information but let you dig into control chart details.
Enact enables you to slice and dice data the way you want, both to keep an eye on real-time quality and to support improvement projects such as Six Sigma. Given this extensive support for flexible views and analyses, you can find the tools that lead to operational insight and better decision making.
No. 6: Support mobile and remote workers
Round-the-clock operations, a global workforce, and the importance of supporting workers who are required to work offsite increase the importance of 24/7 data access from any location. Fortunately, cloud-native software and data storage make this mobility possible in ways that we couldn’t imagine even a decade ago.
Figure 5: Access data from anywhere, at any time.
Enact supports mobility in several ways. Mobile data collection enables untethered, real-time data collection from any web browser or mobile device. Authorized users get instant access to all the data surrounding a given event, regardless of where and when it originates. And mobile access simplifies the communication of traceability data to vendors and suppliers.
Get ready for the future of SPC
SPC is not going away. If manufacturers have learned anything during the past century of SPC-based quality management, it’s that data are the key to optimizing manufacturing operations. The methodology is still right, but how it is used is changing.
Apply these tools, and your process approach will be up to speed in no time. And with an SPC solution like InfinityQS Enact, you’ll also find yourself hurtling toward a robust return on investment (ROI) for your process-improvement efforts.
At InfinityQS, we understand that we all face some challenging and tumultuous times ahead. But we face them together. As manufacturers look to the future, we are here help your organization in innovative and practical ways. Please visit our website to learn more about our Enact quality intelligence platform.
Add new comment