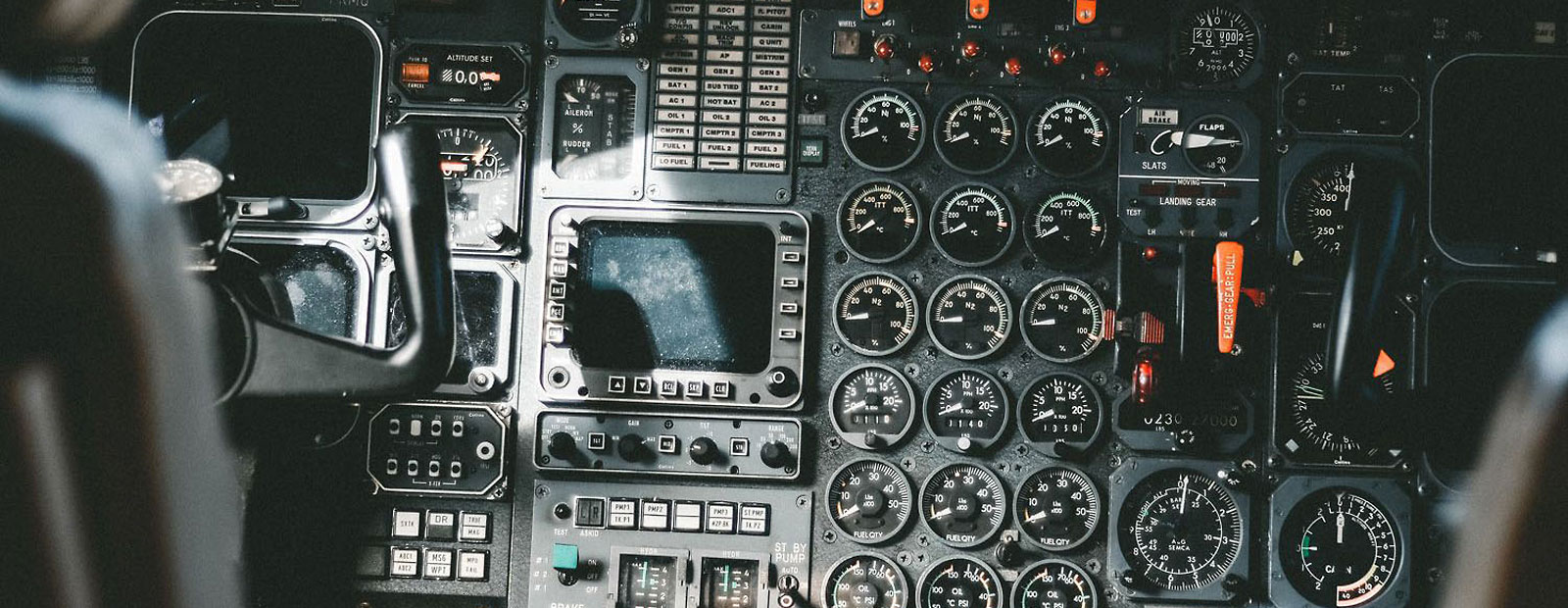
Even though most businesses have invested in quality management and performance improvement, each organization is unique. People, processes, and machines must be coordinated to achieve desired outcomes. This is not easy.
ADVERTISEMENT |
Whether you’re in discrete manufacturing, a process industry, or a service environment, it’s likely that you face challenges like:
• Variability in customer satisfaction and experience
• Resource constraints that impact quality and performance
• Inconsistent and/or inefficient processes
• Availability, reliability, and timeliness of information for decision-making
• Effectively prioritizing tasks and activities
• Organizational silos that reduce the speed and quality of decision-making
Furthermore, you may have more visionary goals like promoting sustainability throughout your environmental, health, and safety functions, or promoting sustainability in the supply chain. It’s hard to pursue these things when there are problems getting in the way of customer satisfaction, occupying the time of your managers and your staff.
Quality management is not just about getting rid of the bad—reducing defects, eliminating waste, and handling customer complaints and corrective actions. It’s also about building the capabilities of your organizations and your people so they can realize the good. To yield the greatest benefits, quality management must also address continuous improvement, which should be focused on outcomes you want, not just outcomes you don’t want and seek to eliminate.
Disconnected quality events, as well as information that could lead to improvement or growth, can originate anywhere in an organization. A corrective action, for example, could be initiated by an audit finding, a customer complaint, or analyzing a key performance indicator (KPI) over time. Discovering these elements and acting on them requires understanding how the quality management system (QMS) works in functions across organizational boundaries. This concept has been called quality architecture by some authors. Especially when processes are managed manually or in Excel, disconnected data sources (and the inability to access them to use the data) can lead to slow responses or bad decisions. Making bad strategic and tactical decisions is far worse than operating less effectively than the ideal.
“Doing the wrong thing right is not nearly as good as doing the right things wrong,” says Russell Ackoff, speaking at the 1994 Learning and Legacy of W. Edwards Deming conference. “Until managers take into account the systemic nature of their organizations, most of their efforts to improve their performance are doomed to failure. If we have a system of improvement that is directed at improving the parts taken separately, you can be absolutely sure that the performance of the whole will not be improved.”
Though often considered an aspect of operations, quality is inherently strategic. Achieving quality goals requires a systems thinking approach to be effective. Systems thinking means examining the performance of the system as a whole rather than attempting to optimize the performance of the parts in isolation. Less efficient processes can be even more effective at the systems level—especially when the skills and performance of the people who play roles in those processes are taken into consideration.
Achieving this balance requires an effective quality architecture. This requires taking into account which quality tools to use, when and how to use them, and which software systems to implement—or avoid implementing. A robust quality architecture can help you achieve better alignment (making sure everyone has the information and resources to work collaboratively toward shared outcomes) and deliver greater value (while reducing or eliminating nonvalue-adding activity). At the same time, a high-level view of how you manage quality can help you identify high-impact initiatives that will move you toward Industry 4.0/Quality 4.0, whether you are in manufacturing or another industry.
Our Dec. 4, 2018 webinar, “SPC and FMEA: Integrating Systems Thinking Into Your Quality Architecture to Drive Improvement,” will cover all this and more—and you’ll also hear examples of how suboptimal processes may not be that detrimental after all. Focusing on failure mode and effects analysis (FMEA) and statistical process control (SPC) as core tools, we’ll show you how to make the most of your investment in quality systems and quality software.
Comments
Medical device industry trends - my point of view on QMS
Since 2016, Compliance with ISO 13485: 2016 and MDSAP has reignled supreme in the device industry for device manufacturers. It is also a welcome and timely change as viewed by the quality system management professionals.
In the life cycle of QMS, it is imperative that effectiveness of its subsystems are effectively examined a few times per year and audit findings are addressed through CAPAs that are issued by the QMS support teams to bridge those gaps that are identified. The impetus for allocating resources by leadership is mainly to ensure certifications are issued / maintained and in so doing the boxes are checked and businessled will not be interrupted as verified during management reviews.
it’s true that business leaders and shareholders measure their success through improved gross margins, ebitda and other stock prices as key indicators rather than quality system indicators. The intersection between financial, operations, quality and service delivery is viewed by the net profits and shareholder‘s ROI. To be fair, medical device companies do their fair share and make every effort to invest and maintain their QMS to ensure compliance. However they suffice to gain the benefits only indirectly and not through the lenses of QMS.
In my opinion unless there is a fundamental shift in culture of quality at the business systems level, in other words a paradigm shift in business management thinking, the QMS architecture may not receive the attention and resources and be identified as at the top of parameter to improve ROI.
I remember the days that the the paradigm shift in QMS was being actualized through efficient operation excellence teams and LSSBB methodology in early 21st century, but then the economic recession in 2008 hit the markets and it fell out of favor and gradually disappeared from the visions of leadership and the objectives in medical device arena despite the very tangible results the same companies were realizing by deploying them.
Will OpEx wave be once again rise and embedded in business management practices, and commissioned to provide tangible / hard cost avoidance data to justify the linkage between ROI in dollars and the quality management tools is the question that time will answer.
Add new comment