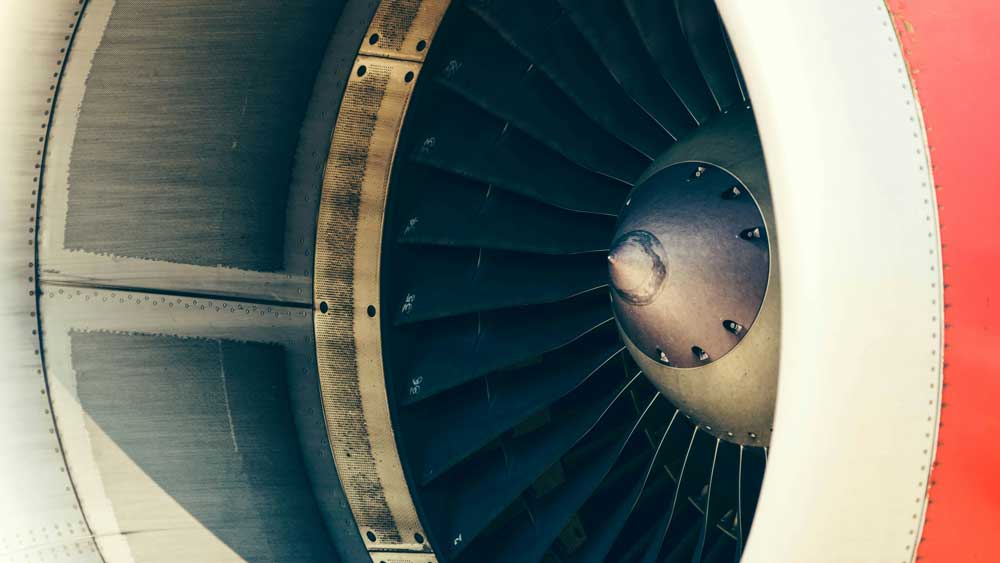
Photo by Inspirationfeed on Unsplash
We live in a world where problems aren’t just growing—they’re evolving into ever-more complex challenges. During the 20th century, we pushed the boundaries of innovation, creating complicated systems that demanded structured problem-solving approaches. Techniques like 5 Whys and the Ishikawa fishbone diagrams emerged, helping individuals and teams tackle the technical hurdles of that era. These methods, grounded in classic logic, empowered us to master the complicated.
ADVERTISEMENT |
But today, we face a new kind of challenge. Problems once neatly defined are now deeply intertwined, influenced by countless variables and cascading effects. In this landscape, the structured methods of the past are no longer sufficient on their own.
To stay ahead, we must adapt. The 21st century demands a shift from mastering the merely complicated to navigating the truly complex. This means merging once-discrete problem-solving methods into unified, resilient approaches, and embracing innovation. This isn’t an option but a necessity.
One example of such a methodology merger would be a combination of the human and organizational performance (HOP) approach and root cause analysis (RCA) for a greater overall understanding.
…
Comments
Nothing New
I was disappointed in this article in that it pushes the old false hood that 5-Why singularly focuses on human error. As a lifelong user of 5-why I know that it doesn't and that when human error is involved and that if the only ‘solution’ is remind, retrain or discipline then the ‘fault’ lies not with 5-why but with the shallow search and biases of the ‘investigator’. This ‘blame the operator’ mentality has been derided by Quality practitioners for as long as I can remember. It is had born the bane of our existence with ‘old fashioned’, ‘command and control’ managers forever.
The example given is not an ‘example of the new complexities of today’. It is fairly straightforward and has been occurring for 100 years; 40+ of which I have actively experienced and remedied.
The comments about AI seem like a blatant and gratuitous attempt to get on a dubious bandwagon. In this example and so many others there is no ‘massive amount of data’. No amount of AI can solve this type of Problem or lead to a determination of the causal mechanisms…
Surely we can do better than this advertisement?
Reply to "Nothing New"
Respectfully, I see a ton of RCAs performed by a variety of different people and from different disciplines and my guess is you'd be shocked at how shallow most of them are. Do all of them lead to human error? No... but between the self-limiting structure of the 5-Whys method along with the strong bias of many people to find fault with individuals, the vast majority of them point to people as the "root cause". And that sucks.
Now, I have no doubt that you are a more advanced and more experienced investigator. But most people conducting RCAs don't have the same level of experience or training as you. And in the world of aerospace quality, there is a ton of finger pointing along with the expectation of blame resulting in punishment.
Is all this the fault of the 5 Whys? No... but come on - is it really plausible to believe that you can reduce a complex event (or even something simple, like the heat-treat issue used in the example) - to a reverse series of five steps and come up with anything useful? Again, I am not doubting your personal experience - but most people aren't you. The example needs to be simple to stay within the word count limit and also so that it makes sense to a wide audience. But the lessons are solid - and would be even more applicable in something more complex.
And AI is absolutely a game-changer precisely because it can process a vast amount of data. Not the data from any specific event, but all the published data on the subject of metallurgy, exotic alloys, machining techniques, etc. AI alone will not be sufficient - but coupled with a knowledgeable, diverse team of experts, it improves the quality of investigations, solutions, and reports... and people in our field who learn to adapt it will have a dramatic advantage over those who shun it or discount its usefulness.
Some HOP people can be arrogant and dismissive, but that doesn't make them wrong. However, they have a blind spot to the usefulness of tried-and-true methods. The combination of HOP plus modern RCA methods plus AI is what the next generation investigators are going to need. That was my point.
I hope my comment doesn't sound disrespectful - I'm truly grateful you read the article and appreciate the comment.
Add new comment