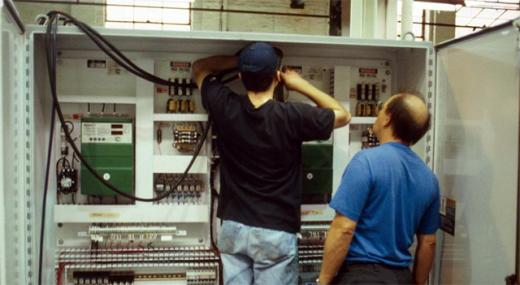
While on-the-job training is practical for certain applications, manufacturers rely on it too heavily as a method for onboarding and training employees.
ADVERTISEMENT |
Companies looking to train a new workforce should be aware that on-the-job training can:
• Hurt productivity
• Increase safety risks
• Impact quality costs
Training without standards
On the surface, the concept of on-the-job (OTJ) training makes sense: Follow an employee around and watch what he does so you know how to do the same. Unfortunately, the desired outcome rarely comes to fruition. OTJ training methods rely too heavily on mentor/mentee relationships and are by their very nature, nonstandardized.
A new recruit may experience a completely different training process depending on:
• Availability of mentors
• Variance in tribal knowledge
• Accuracy of the job demonstration
• Nonstandardized work practices across mentors
…
Comments
Agree and Disagree
I was encouraged to see this article...Deming talked about this extensively up to his death in 1993. He used "telephone" to illustrate Rule 4 of the Funnel (Nelson's Funnel experiment, popularized by Deming as a follow-on to the Red Bead during his famous 4-day seminars). Rule 4 is especially wicked, because as time goes on, the standard is lost, and the output drifts further and further from what was intended. It doesn't just apply in manufacturing, though. It's probably worse in service, and takes a bigger toll, because the "last one written" is often used as the template for the new one (even though it drifted from the standard template long ago). This results in overruns, waste and a lot of rework (if the differences are caught), sometimes on a grand scale. Just look, for example, at government spending. At the end of the year, almost every agency and operation in the government struggles to ensure they spent all the money they got last year, because if they don't, they can't get that much next year (and they still ask for more each year). In that environment, realistic budgeting is a fool's errand. So, kudos for bringing this principle forward again!
On the other hand, it seems we have drifted away from what we learned in the 90s again..."85% of quality issues are caused by worker errors?" That's opposite of what's actually going on. Systems thinking and the theory of variation teach us that we can not separate the performance of the worker from the performance of the system. Deming's contention was that 85% of the problems are caused by management (because only they can provide the constancy of purpose and resources to improve the system). Later in life, he pushed that to 94 or 96%. This is illustrated in the next sentence of the article, "This means that lack of procedural adherence or poor training practices are still where most quality issues originate." You can't hold the process workers accountable for errors if the system trains them to make errors, does not properly monitor for errors, does not improve systems and their associated processes through mistake-proofing, etc.
Add new comment