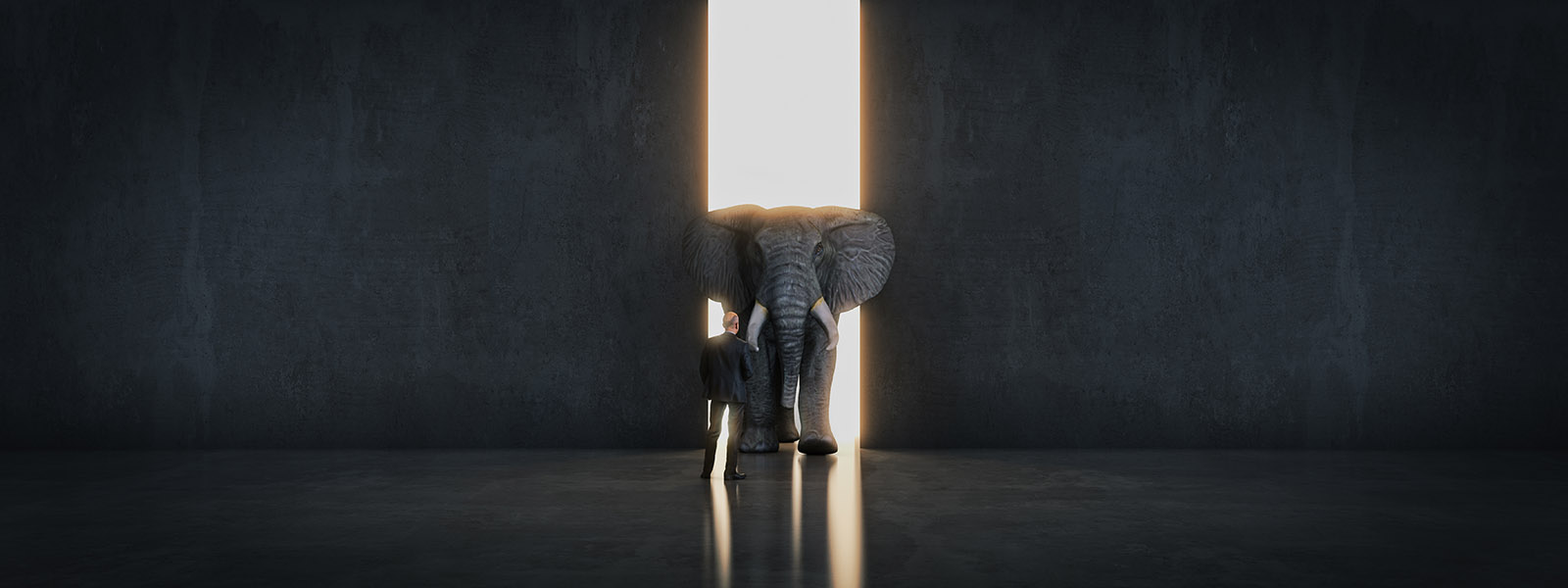
It’s no secret that manufacturing companies operate in an inherently unstable environment. Every operational weakness poses a risk to efficiency, quality, and ultimately, to profitability. All too often, it takes a crisis—like Covid-19 shutdowns—to reveal operational weaknesses that have been hampering an organization for a long time.
The nature of the problem
It is not just a manufacturing company’s production facility that faces operational challenges, either. The entire organization must address a host of risks and challenges; shifting consumer and market trends necessitate improving agility and responsiveness; dynamic and global competition force innovation not only in product development, but also service and delivery; evolving sales channels, including online outlets, challenge established profit margins. And these challenges are not going away any time soon.
The real problem, however, lies not with the challenges themselves but with a company’s reluctance to see the operational weakness that makes it susceptible to a particular risk in the first place.
Operational weaknesses
Lack of remote access to quality and operational data
Access to data in traditional forms has largely been taken for granted. For instance, in highly manual environments, data can be accessed by simply walking on the shop floor or accessing on-premises systems within a quality management system firewall. Manufacturing operations have never been regarded as a remote activity, so not having remote access to critical data was never seen as an issue. Thus, remote access to data has never been addressed as a need but rather as a “nice to have.”
Multiple scenarios have exposed the shortcomings of this model. The offshoring frenzy early in this century, for example. Global dynamics convinced many manufacturers of the benefits of offshoring certain aspects of their value chain. Unfortunately, quality assurance was severely diminished due to lack of quality control data availability and transparency.
We have come to realize the limitations of environments lacking remote access to quality and operational data.
Remote access does not just mean off-site, but off-shop floor as well. Although offshoring—and Covid-19 restrictions—have highlighted problems with no off-site data, companies can capitalize on that wake-up call by realizing the risks from no off-floor data as well.
Do you have data available to you when you are not on the shop floor? How about when you are not at a particular facility?
Inability to meet substantial increase in demand
Certain sectors, such as food and beverage, healthcare, consumer packaged goods, and medical supplies and equipment, have witnessed a sudden and massive increase in demand. Normally, fluctuations in demand are manageable and sometimes even predictable, such as with market trends, economic trends, marketing activities, or through seasonal variations. But Covid-19 has generated a massive and sudden increase in demand. Often, this demand outstrips capacity, and every percent increase in yield across individual processes, sites, or lines is a big deal in terms of meeting increased demand. However, many manufacturers are realizing that a lack of fine-grained visibility into performance makes improvement in yield an insurmountable challenge, thus leaving them unable to meet the rising demand.
Availability of trained workers
Every plant has operators trained in specific duties and have provision for worker absence. But the scope of disruption from issues such as the skills gap to uncertain work visa regulations has meant that the availability of “trained” workers in specific roles has been an ongoing challenge. That has meant using available personnel in new and unfamiliar roles. The consequent lack of knowledge, training, and experience exposes the manufacturer to significant operational and quality risks. Manufacturers have realized that reliance on experience has been a weak point.
Having an automated system to collect data and perform regular quality checks and process collected data is more important now than ever. We can now see the usefulness of guided data collections, quality checks, and workflows that can be performed by even relatively new workers without a lot of experience or training, while still ensuring quality compliance.
Reliance on manual labor for routine mundane tasks
Many manufacturers have relied on manual labor to perform many routine and mundane tasks within the production environment. Labor is considered a cheap and readily available resource compared to what is perceived to be the costly alternative: technology. This is true especially in developing countries or where migrant workers are readily available. But with Covid-19, that manual labor pool suddenly became very scarce, leaving those manual tasks unperformed. By making the manufacturing workforce more efficient, and automating many mundane tasks, a reduced workforce could have been deployed on mission-critical tasks where human input is required, or where automation is not possible.
Waste perceived as a cost center
Waste, or the reduction of waste, is typically seen as purely a matter of cost. Because many raw materials have been available in abundance, many organizations choose manufacturing processes that involve an unnecessary degree of waste. It is a choice that many manufacturers accept, and they budget for a high degree of waste.
“Waste is just a resource out of place.”
—Bill Coors
However, events like the Fukushima disaster significantly disrupted—some would say destroyed—some well-established supply chains. The Fukushima prefecture was a major supplier of raw materials and components for electronics. When the Fukushima Daiichi reactor melted down, those inputs became scarce and more costly as a result. If minimizing waste had been a higher priority for manufacturers, perhaps the issue with material inputs would have a lesser impact on the profitability. Less waste, more margin.
Wasteful response to risk
Although manufacturing automation can be a useful tool to mitigate certain risks, it is not a panacea. Implementing automation without an appreciation for the real advantages of digitally analyzed data could just mask an underlying weakness. It’s a matter of blind automation vs. optimization. An organization can automate a suboptimal process that generates lots of waste, produces defective products, has a low yield, and suffers significant machine downtime... it just does all that faster... and consistently.
On the other hand, an optimized process is where you achieve the optimal performance of a process across many dimensions, such as quality, yield, availability, and waste. The more intelligence—data—you have about a process, and its context, over time, the more able you are to achieve greater levels of optimization.
To turn crises into opportunities, organizations consider:
• Cost (margins, efficiency, productivity, yield)
• Value (quality, agility, innovation)
• Risk (operational risks, demand-side risks, economic risks, supply-chain risks, black swans, quality, brand)
An organization can keep costs down to a point where quality becomes unacceptable, and where risks to brand, reputation, and safety become too high. Or they can continue to drive up quality to a point that it becomes uneconomical in the markets the products serve. Or they can become so risk-averse that their ability to compete becomes untenable.
Manufacturing optimization at this holistic level is about achieving the optimal balance between all three of those dimensions. Automation then becomes the force-multiplier of optimized processes.
Next, they must consider if their data system is dysfunctional, i.e., are their data:
• Incomplete
• Inconsistent
• Inefficient
• Isolated
Then a company is ready to consider data-gathering and -processing solutions that can mitigate risks—whether those stem from a novel virus, a natural disaster, or changing market conditions.
Silver lining
Although a crisis can expose a weakness, it does not actually create the weakness. This is where innovation supports risk management. What are the risks, and how can we implement new technology to mitigate those risks?
Realizing a weakness opens opportunities for improvements. Covid-19 and other crises have highlighted operational weak points and blind spots, and exposed IT limitations. We can more clearly see the urgency and need of true quality management system transformation. We can see it is not a matter of if a crisis-level event hits, but when and how severe.
Building flexible, capable, and resilient foundations for the future can begin by asking yourself these three questions:
1. Did these risks and our susceptibility to them exist before a crisis exposed them?
2. Did we do anything to mitigate said risks?
3. Are we doing anything now?
The silver lining to any event that poses a crisis to your operations is this: The weakness to that risk is now out in the open and thus ripe for resolving. Furthermore, this can open us up to more thorough investigations of other potential weaknesses that can be addressed pre-crisis—always a better option.
There is a difference between people in leadership positions and those who lead. One thing true leaders have in common is an openness to scrutinize their organization’s weaknesses and a willingness to seek out and implement appropriate solutions.
Add new comment