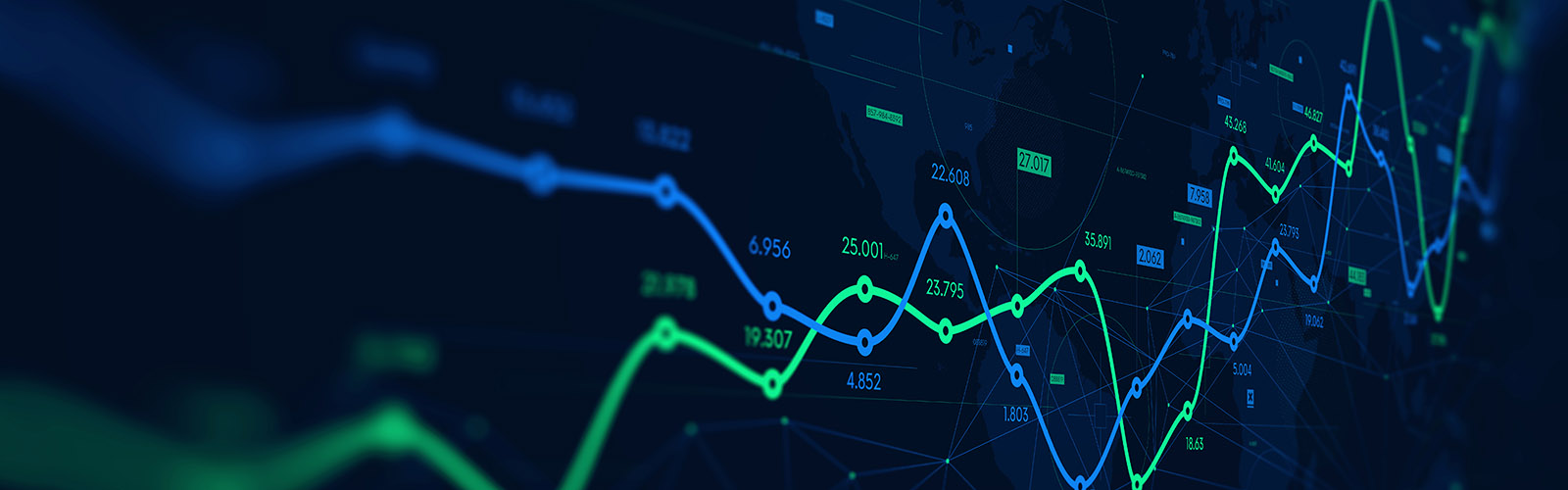
An organization can achieve great results when everyone is working together, looking at the same information generated from the same data, and using the same rules. Changes can be made that affect a company’s bottom line through operational improvements, product quality, and process optimization. There are quality intelligence (QI) solutions that can help reveal hidden opportunities.
Companies can save money and improve operational efficiency by effectively focusing resources on the problems that matter most from both a strategic and tactical perspective. A proper QI system makes this practical in several ways.
The QI advantage
With a QI system, data are captured and analyzed consistently in a central repository across the organization. This means there aren’t different interpretations of the truth, and there is alignment among those on the shop floor, site management, and corporate quality.
Alignment is possible because of a positive cascade of events:
• Notifications are sent to the appropriate people, and workflows trigger the required actions. This means people are appropriately accountable for addressing issues. Those issues can then be analyzed to understand recurring problems and how to avoid them.
This is possible because...
• Rules are consistently defined and enforced. This means users aren’t left to decide whether an action should be taken, which removes bias, increases consistency, and prevents tampering that ultimately leads to greater problems.
This is possible because…
• Data are collected consistently, and erroneous values are prevented. This means the data can be trusted, and time isn’t wasted accommodating data-entry errors.
Manifesting ROI
Every effort and expenditure in business must, of course, be weighed against a return on investment (ROI). This is where QI systems shine. ROI in a QI system becomes evident on multiple levels.
In manufacturing, consistency and accuracy are intimately related to profit margin. Proactive analysis of data from production lines can translate into customer retention, reduced waste, and reduced labor costs. For example:
• Material savings by reducing overfill
• Increasing yield from material inputs and machine utilization
• Increasing operator productivity and performance and thus reducing workforce overhead
These few examples are the tip of the iceberg. Every organization has opportunities like these, and many more besides. Which opportunities can your organization find?
Roads to rapid improvement
How does QI work in practice? Let’s put ourselves in the shoes of a corporate quality professional at a multinational food and beverage company that has access to all the quality data across the organization. Where should we start?
First, it’s important to clearly identify the goal we are trying to achieve. For this example, let’s say we want to identify “easy wins” for our biggest critical-to-quality (CTQ) metric, net contents. If we can clearly demonstrate the value of quality data, we’ll be able to provide even more impact to the company in the future.
This is the classic low-hanging-fruit strategy. You probably already have one or two areas of production you know are suboptimal and leaving profit on the table.
A good QI system provides much-improved visibility into data—which can reveal inconsistencies between runs and production lines as well as quality issues that have been invisible with paper-based data sets. Here’s an example of a dashboard we might use to start our investigation.
Use a grading matrix, like that provided with Enact, to identify all data streams flagged as “A3,” which means the short-term standard deviation indicates 100-percent yield is possible, but the process isn’t performing that well.
Since we are focusing only on net weight, it makes sense to filter the dashboard to show only net weight results. The example below now shows there are four data streams with a grade of A3, which will be the starting point for further analysis.
A simple click on the “A3” cell provides the details of which products and which production lines are performing this way.
At this point, it is clear to see that the site in Fairfax, Virginia (denoted by the “FA” in the process name), has several opportunities for easy wins . We can now contact the Fairfax site to discuss how it can improve its yield. With a process potential of 100 percent, this is hopefully a simple solution like retargeting the process (or more likely, just leaving the process alone instead of making changes for each run or shift).
Because everyone is using the same QI system, the same data can be used to investigate these exceptions at a more granular level. This dashboard below is focused on exceptions, though traditional tools like Pareto and box-and-whisker charts are also commonly used. The stream summary tile shows that the “BBQ—50g” chips have the most issues with net weight (the images are ordered by number of issues). It is a simple click on that icon to look at the associated control chart.
Viewing the control chart confirms that the process is running consistently but is consistently overfilling product. There are many upper-specification-limit violations, and this behavior warrants a discussion with the operators on why the process is performing this way.
Perhaps there’s a setup issue that needs to be addressed. Maybe there’s a new filler on the line, and it hasn’t been fully calibrated. It might also be as simple as the operators aren’t looking at their notifications. There are other tools that can be employed to help. For example, each time a specification limit violation is encountered, the user could be required to enter a comment, or better yet, select a corrective action they took to address the violation. These can then be analyzed to see if a cause can be found. Another user for your QI system is to see how other sites perform when making the same product. Perhaps they have experienced this same issue and have a solution.
Once the site has implemented its improvements, you’ll be able to see if they’re improving using the same grading matrix you used at the start of this analysis.
If these steps sound familiar, they should. A QI platform does not replace SPC. In fact, a good QI system is all about making the familiar SPC concepts more accessible across an entire organization. The QI format allows all personnel to see and understand what the data are saying, which transforms raw data into actionable information.
The value of visualized data
The foundation of any QI platform is data. And that information is gold—if you know how to mine it. You see, it’s not the volume of data that makes or breaks your production and profit goals. The key is being able to see your data in a way that reveals the path to improvements.
Properly visualized data are priceless. So why isn’t every organization employing a digital QI system? Most organizations simply haven’t designated a team or department focused on these kinds of improvements; they focus on the immediate use of the data to manage quality and control processes (e.g., a statistical rule was violated, so adjust the process). This short-sightedness is why they miss out on the significant improvements that come from strategically using the data they collect.
Think about what your company could do with QI. What could you accomplish knowing how your products are performing across your company? Investigating which sites are setting the benchmark, and which ones need help? Understanding which actions are most likely to solve problems—and what those problems were?
If you can’t get those kinds of insights from your quality data, then you should ask yourself how long your organization can do without them.
As stated in part one of this series, “A reimagined quality stands on three pillars: data, which are the drivers; decisions, based on those data; and direction, or the control mechanisms that you put in place because of the data.”
We cannot realize potential improvements by making decisions based siloed data that are inconsistent in formatting and presentation. In fact, we see in part two how this outdated way of thinking about data usage exposes processes to the harsh realities of risk.
In part three we see how the visual component of QI helps reveal what the data mean and how we can edit the data format to help us make logical, informed decisions—the kind of decisions that lead to process improvements and increased profit.
And now in this article, we demonstrate basic data analysis using visualized data from a QI system. It is easy to see how QI makes tried-and-true quality tools—like SPC charts—that much more usable and actionable.
Clear actionable data are the stuff improvement is made of. Quality intelligence is the key to such data.
Add new comment