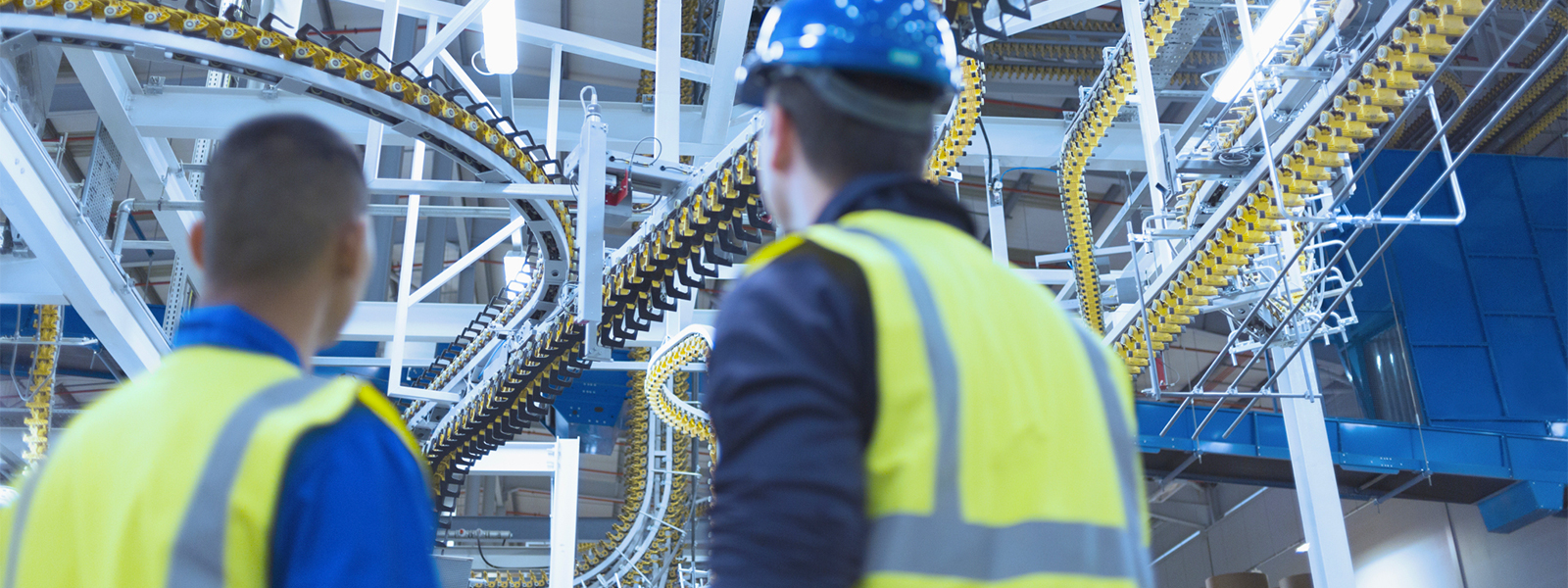
Quality data are the heart and soul of statistical process control (SPC), the industry standard methodology for measuring and controlling quality in manufacturing processes. Asking manufacturers to give up data is like asking them to give up water. It’s just something that is necessary for their survival.
However, like water, data can accumulate quickly under the right circumstances. When we get too much, we can drown. But with the judicial application of quality intelligence, we can dive into our data and come up with treasure.
The data deluge of digital transformation
For decades, manufacturers have collected data in a dedicated way, laboriously documenting essential process metrics and required quality checks. Traditional quality management methodology meant diligently performing quality checks, putting that documentation on paper or in a spreadsheet—and filing it until an auditor asked for it.
During the past 20 years or so, we have found new ways to collect more data faster. We have the ability to automatically, wirelessly, collect thousands—even millions—of data points per minute. It’s exhilarating.
Until it isn’t. Today, quality professionals and operators are dealing with an unprecedented volume of data coming from their production environments. Trying to sift through this flood of data can overwhelm even the most experienced Six Sigma Black Belt.
At a certain point, it all becomes increasingly murky. In general, most of the data that teams collect are still ignored, filed, and eventually discarded. That’s a shame, because there is a cost for all that data collection activity.
Today’s manufacturers are aware of the investment they have in their data. And they are looking for a return.
Looking for the ROI: finding riches deep in data
The reason we collect data is to learn what’s happening on the manufacturing plant floor. That information helps us improve our processes, prevent issues, and determine where to expend our efforts and resources. Such data-driven knowledge presents a distinct competitive advantage for forward-thinking manufacturers.
The Enact quality intelligence platform from InfinityQS provides a unique and innovative way to surface this rich information through data stream grading.
Say you have a company with multiple manufacturing sites, each with several lines. If you’re like most manufacturers, you want to aggregate the data from every line and site to look at some summary statistics. You want enterprise-level visibility to find which sites, processes, or products are doing well, which are doing poorly, and what needs attention.
In a traditional approach, you would look at metrics like Cpk and Ppk ratios that compare specifications limits to the spread of a process’s output to reveal standard deviations.
However, these metrics have a few shortcomings:
• Typically, only a few people on staff understand what Cpk and Ppk mean.
• Cpk and Ppk report how good or bad a process is; they do not help you understand whether the problems are unique or systemic.
• Cpk and Ppk ratios are designed to focus on single streams (one part, one process, and one feature); you can’t use them to compare metrics at the enterprise level.
Parts per million (PPM) is another common process metric. Unfortunately, it requires proper normalization and is not very intuitive for most decision makers.
However, most users do understand yield. Data stream grading offers a new yield-based way to assess manufacturing performance.
The ABCs: a simple view of performance
Data stream grading presents users with a simple letter (A, B, C) and number (1, 2, 3) combination to indicate how a specific data stream is performing based on daily summary records. Nine grades are possible in total: A1, A2, A3, B1, B2, B3, C1, C2, and C3. A grade can represent a part, process, feature, or entire manufacturing site.
The letter grade represents the potential yield of the stream, that is, the expected yield assuming a perfect, on-target element using the level of variability. A distribution spread that falls well within the specification limits gets an A grade. Grade B is when the distribution width is equal to the range of the specification limits. Grade C is when the distribution cannot fit within the specification limits. A is the best letter grade possible.
The number grade indicates performance yield, that is, the expected yield using centering. A perfectly centered process is a 1. A number grade of 2 means the process is not centered. A process that is woefully off center will earn a number grade of 3.
Exclusive to the Enact platform, grading provides a unique way to roll up and interpret performance across many products, processes, and sites. It then goes one step further, allowing you to quickly drill down into specific data streams. You can dive into each stream to determine where to focus your attention for the greatest ROI and most effective quality wins.
Whether you have one plant or many, grading allows you to quickly identify where and how to make the biggest impact on quality, processes, and business performance. Gold starts to emerge out of the murky depths of the data.
Going after the ‘A3’
Based on Enact’s grading system, a grade of A1 indicates the highest-level performance, with minimal or no scrap. It’s right on target. A C3 grade reveals a process that has low potential and even lower performance. C3 is where you want to deploy your quality improvement teams to resolve systemic issues.
However, a grade of A3 reveals a stream that is highly capable but way off center. There’s a lot of room for easy improvement here. The “3” tells us we have a poor yield, but the “A” tells us that we should have the potential to perform at 100-percent yield by simply retargeting the process.
Often the fix is a matter of operator training or modifying the process setup. But we wouldn’t have been able to quickly isolate the opportunity here without quality performance grading.
In this way, grading is a great tool for quality professionals who not only need to uncover hidden insights in data, but also require an agile way to prioritize their resources and efforts. If you are trying to maximize every resource and make the biggest impact for the least amount of effort, going after the A3 grades will be your best bet for quick returns.
Seeing the big picture
To help with comparative analysis and prioritization of improvement efforts, Enact includes several ways to look at grades across multiple streams.
You can create a grading matrix that summarizes all the streams that meet each grade. You can drill down into the streams under different grades. For instance, you can see which ones are A3s, which are where your easy wins are going to be. You can see where your C3s are, which are going to be your major improvement initiatives. The primary benefit of this view is you can target streams based on amount of effort.
![]() |
A site summary shows the site grade for each critical feature across multiple plants.
![]() |
Color codes make it even easier to spot areas that need attention. You can click a grade to see layered details that reveal the grades for individual processes or parts. A site summary is especially helpful for determining:
• How each line is performing
• How various parts perform on each line
• How features within a process measure up
When you want to dive even deeper into a particular stream, you can quickly access the granular information that’s behind the grade.
![]() Click here for larger image. |
Bring treasure to the surface
What you get with data stream grading is a fast and easy way to find nuggets of process improvement knowledge hidden within seas of data. The simple letter-number combinations and color codes make it even easier to prioritize your actions. You can take your quality to the next level and gain an edge over the competition—and that’s worth every ounce of gold.
At InfinityQS, we understand that we continue to face challenging and tumultuous times ahead. But we face them together. As manufacturers look to the future, we are here to help your organization in innovative and practical ways. Visit our website to learn more about our Enact quality intelligence platform.
Add new comment