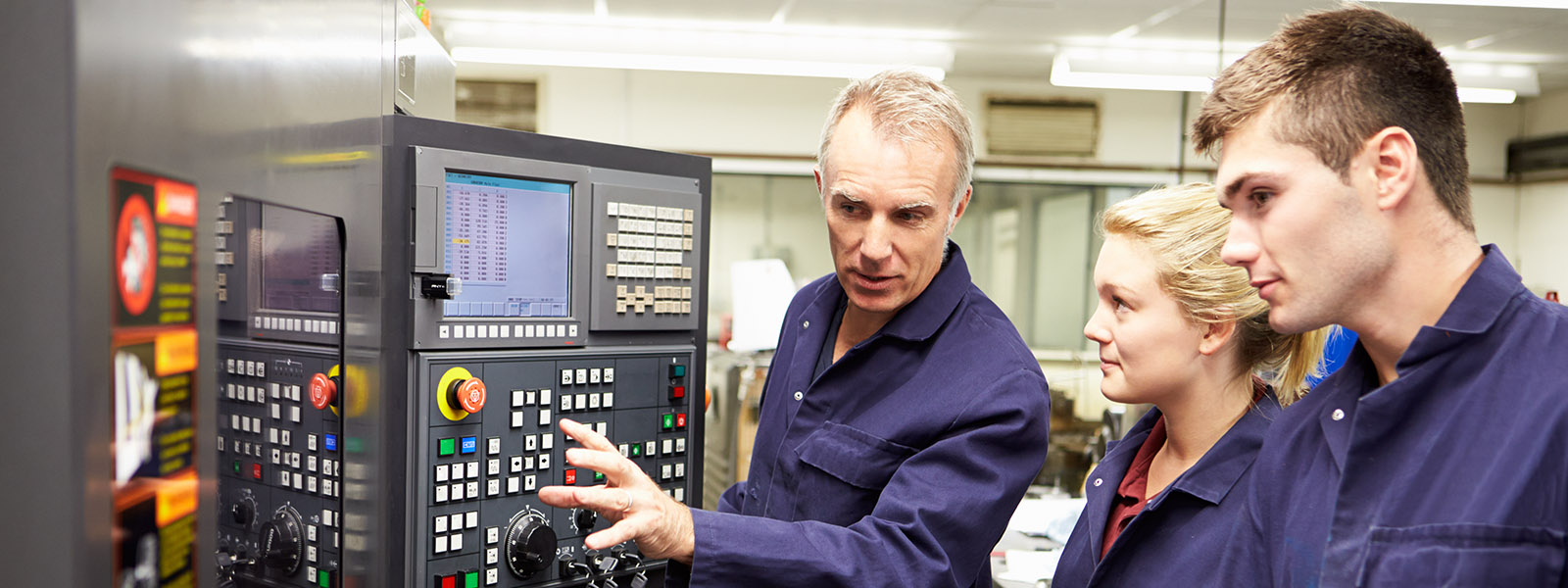
For many manufacturing quality professionals, the thought of updating their statistical process control (SPC) solution is like getting an extra birthday. Many quality experts know that modernizing the way they collect, analyze, and use data is a critical need for their organizations, now more than ever.
But it may not be easy to convince the rest of the stakeholders in a company to not only approve a new quality intelligence solution but also adopt and use it. Fortunately, InfinityQS understands the challenge. We’ve been helping organizations through this process for three decades, and we’ve learned one fundamental principle for success: Start with a proof of concept.
A phased approach
The term “proof of concept” is used across industries to describe an exercise to determine the feasibility of a concept, design, or assumption. At InfinityQS, we talk about using a proof of concept as the first phase in deploying our Enact quality intelligence platform. We find that starting with this focused, guided implementation on a single process enables stakeholders from all areas of the business to experience the features and capabilities of the solution—and see for themselves the value that it offers.
A well-planned and executed proof of concept will help your teams to learn the software, quickly see tangible results, and build a strong starting point for expanding the deployment across additional lines and plants.
Prove it!
Cloud technology is changing the quality management landscape. And although most of us understand how cloud software makes it possible to share and consume information from any mobile device from anywhere we are, it’s not instantly clear just how transformational that ability can be in a manufacturing setting.
During a proof of concept, an InfinityQS application engineer or an expert from one of our global network of service partners works closely with your internal team. That team should include stakeholders from all levels of the organization, including champions at the management level, quality professionals, and most important, operators. The direct involvement of these participants helps them form a solid foundational knowledge of how Enact works, gain confidence using the software, and build a business case for expanding Enact across your manufacturing operations.
That’s important because Enact truly is a new way of approaching quality management. This award-winning quality intelligence platform speeds and simplifies real-time quality data collection, reporting, and analysis. Whether your company operates one manufacturing site or sites in multiple locations, Enact can help you meet your most pressing goals—reducing scrap and waste, improving product quality and process performance, and maintaining compliance—with an easy-to-use visual interface, complete mobility, flexibility, and power.
Proof of concept works
The way a proof of concept works is simply this: Start small. Focus on a small sample of parts that are subject to the same data collection routine. Sounds sensible, right?
For most organizations, that means selecting a single filling operation or a packaging operation, for example. Our team starts with a questionnaire that helps us understand your goals and the results you would like to obtain during your proof of concept. We also gather information about the process and the parts produced that we’ll be focusing on during this phase. Next, you’ll work with your application engineer to achieve your desired results. During just a few guided sessions, you’ll build your first process model, begin collecting data, and learn about the data analysis features Enact offers.
During the course of the project, involvement from operators is essential. You and your assigned InfinityQS expert will review production data collected by your operators in Enact. During guided sessions, you’ll also discuss feedback from your team and make adjustments to your initial deployment and to prepare for your phased expansion.
Process model
The first feature in Enact we’d like you to get familiar with is the process model. It’s a new concept in the quality manufacturing software world, and it’s important for customers to get a handle on what it is (and how it’s used) in order to get the most from Enact. Everything starts with the process model. Here’s an example of a rudimentary process model:
The process model is a powerful and useful tool that allows you to build a process out in step-by-step fashion. It’s expandable, helps you visualize your processes, and centralizes and simplifies the ways in which you manage your operations. Above all, the process model helps you better understand your processes.
In addition, the process model forces you to think about the nuts and bolts of your manufacturing processes and how it all fits into Enact. You define the components or ingredients of the finished product and the steps that go into creating the product, from raw materials to finished item.
Building your process model is an important part of the proof-of-concept phase, as it is the basis for expanding your Enact deployment. The idea is that once you get the hang of that first process model and the accompanying data collections, you can reuse that process model to rapidly expand to similar production processes.
Data collection
You’ll begin collecting data early on in the proof-of-concept project. During your first guided session, you’ll see how easy it is to design a data collection routine in Enact. After creating your first data collection, it’s time to put Enact into the hands of your operators to begin collecting production data.
Collecting data is an important milestone in your journey with Enact, but it’s only the beginning. Enact is about more than just collecting data. It’s about gaining insights from analyzing the data and acting on those insights to drive transformation within your organization. Achieving a solid data collection foundation isn’t the finish line; it’s the starting line.
Dashboards
Dashboards are the primary tool for all Enact users, from operators to senior management, and the administrators of Enact. As Eric Weisbrod mentions in his process model blog, “Enact delivers what we call prioritized, or tailored, content. It’s [precisely] the information that the user needs to see, without all the other extraneous stuff that can be distracting.”
Notifications that are pertinent to each user, data collection reminders, and customizable reports allow dashboards to present the most effective information to your users. The best part is that it doesn’t require creating hundreds of dashboards. Once configured, a dashboard can be used across your organization. A filling operator, quality technician, and packaging operator could all use the exact same dashboard and see exactly what they need from it.
Demonstrate value
One of the outcomes of your proof of concept is that you can analyze your results and immediately realize the value Enact can bring to your manufacturing operations. You’ll see exactly what Enact can do for you firsthand.
The findings you collect from your proof of concept—overfill, reduced waste, reduced scrap, whatever it may be—can be presented to stakeholders in your organization to show them how Enact not only can make your operators’ jobs easier, but also save you money and hone your processes to perfection.
Where to now?
Repeat and expand. After your proof of concept is complete, it’s on to a pilot, where you will deploy Enact to other production areas. During the pilot phase, you’ll continue to expand on your deployment, using additional functionality, such as gauges and automated data collection, and continue planning for your full production rollout.
A proof of concept will help you align your teams and demonstrate the value of your quality intelligence deployment. It’s a time- and cost-effective exercise that will help you ensure rapid adoption as well as a solid return on your quality investment. And that’s an important thing we all can agree on: We all want to see that the money we spend for quality and improvement is well spent.
At InfinityQS, we understand that we continue to face challenging and tumultuous times ahead. But we face them together. As manufacturers look to the future, we are here to help your organization in innovative and practical ways. Please visit our website to learn more about our Enact quality intelligence platform.
Add new comment