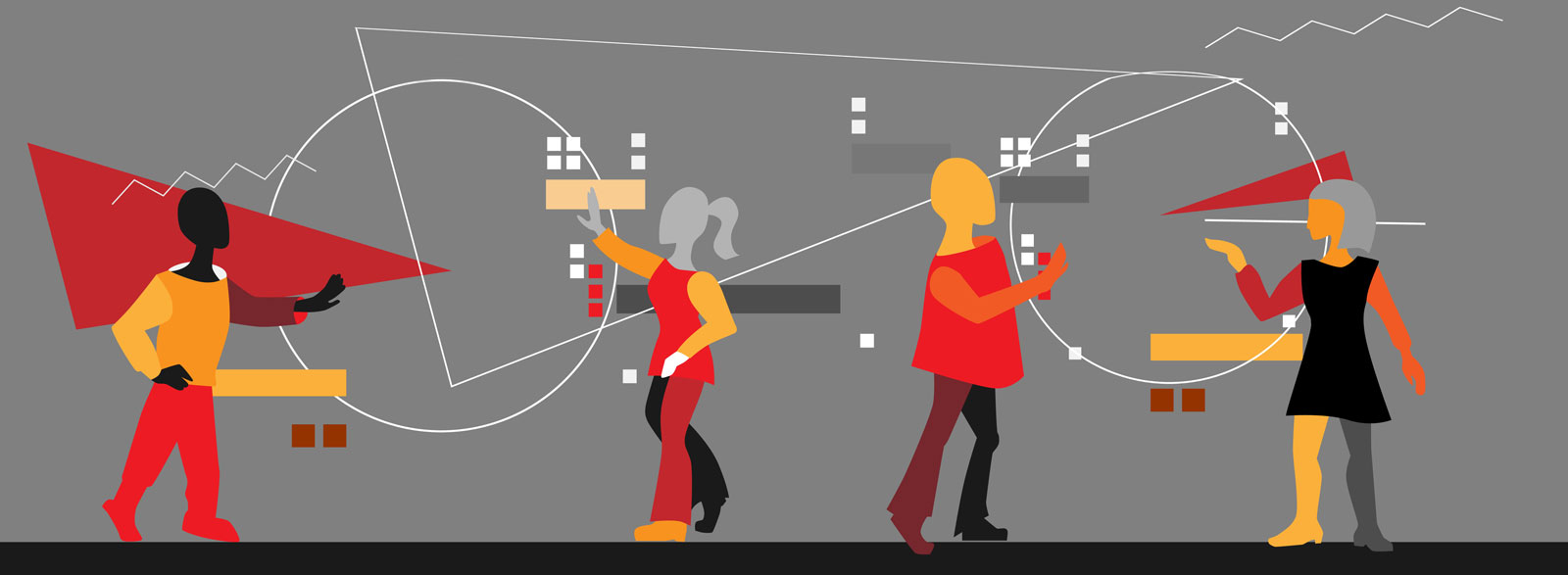
Product development (PD) is the life blood of a company’s success and is the process for innovation. Today, product life cycles are shrinking due to an ever-increasing number of competitive and disruptive products coming to market quicker.
To stay in business, a company’s PD needs to become more effective, more productive, and faster. Product development systems can no longer take years or months to deliver something that the customer will hopefully still want. Planning, design and development, testing, and release can no longer rely on the currently widely practiced sequential phase-gate waterfall methods developed years ago.
To continue to meet the fast-changing and high-pressure demand for lowering costs and delivering products to market, companies must change their new-product introduction process. They need to become lean and agile with an advanced product quality planning and control plan (APQP). And for the automotive sector, the Lean Agile APQP system will reduce product development time, increase an organization’s design and development skills, meet customer requirements, and improve the engineering staff’s morale. It’s changing the way PD is done to deliver production part approval process (PPAP) requirements and meet customer needs more quickly and effectively than traditional methods. It is the way to effectively innovate and capture market share and new customers.
The lean-agile approach has enabled tech companies (e.g., hardware and software), government agencies, aerospace and aircraft manufacturers, school systems, and petrochemical industries to successfully develop, design, test, and release products and services more quickly and effectively than other traditional waterfall methods. Lean Agile APQP refines the core elements of agile product development and adapts it to meet the needs of hardware and software sectors. In fact, Omnex has developed The Lean Agile APQP system to help its clients cut concept-to-delivery times in half, allowing for more innovation and more product offerings.
During the past four months, an Omnex team of experienced automotive new-model launch and product development personnel have studied the issues facing their customers who are using current waterfall product-development methods. What they found was a process that took too long and was rife with missed customer requirements, chronic late delivery, and uncertain quality.
Studying similar industries and other commercial sectors, the team recognized the benefits of using lean/agile methods to cut waste, highlight product development progress, and engage development teams to deliver higher-quality products faster and at lower costs. The team then went about adapting the process for specific applications in the automotive industry. The resulting Lean Agile APQP system addresses the phase-gate issues with the traditional APQP waterfall method while delivering well-established PPAP requirements.
Lean Agile APQP will revolutionize how product development is conducted. It will positively impact the innovation cycle essential to a company’s existence and advance traditional automotive PD to a new level of productivity. Lean Agile APQP will keep auto suppliers and OEMs competitive in today’s disruptive product-introduction environment.
![]() Figure 1: LAMDA |
Lean Agile APQP is a system that incorporates lean principles in the workflows, work products, program control methods, and the roles and responsibilities of management in a new PD process. The method can be described as integrated, cross-functional teams working in a transparent product-development environment. Short, iterative development cycles apply look, ask, model, discuss, act LAMDA (figure 1) and a set-based approach with a product delivery focus that is based on customer feedback and process improvement. It’s analogous to the methods used by the Wright brothers in developing propelled flight.
Small teams, clear communication, continual incremental delivery of product, and PPAP requirements stack up and create a final product that gets to market faster and hits its target.
The system takes the approach of first identifying and closing knowledge gaps around targets, capability limits, trade-offs, and ideas, and uses two- to four-week work windows to close those gaps before laying down a design. Applying the LAMDA model to continually learn and close gaps, the teams build tests to learn the trade-offs and limits vs. the requirements to identify the design space. In this way, LAMDA will ensure that success is planned for in the eventual design.
This results in designs that do not have to be reworked in later stages, which saves engineering costs, time, and harmful impacts on morale. It is well-documented that 65–75 percent of engineering capacity—also known as costs—is spent performing rework. Most of that rework happens late in projects, where the time delays can’t be made up, which lengthens the time to market. Similar to compounding interest on excess spending, additional rework gets piled on the more the market moves during the product development cycle (figure 2).
A series of reviews that integrate the different teams’ learnings at particular points in the development cycle align the learning cycles to decisions that need to be made and that can be made at those points. These integration events are when any additional needed knowledge is identified and set any further actions in place to gain that knowledge to make the next series of decisions.
Work task boards are integral to the agile sprinting method. These types of tools make the work to be done during the sprint visible to the entire team. With team leaders assisting the team to simply track work progress on a daily basis, everyone can see the progress and issues facing the team. The sprint produces product deliverables on an incremental basis and provides for a retrospective look back for the team to review how well it performed during the sprint, identifying any opportunities for improvement that can be applied in the next sprint. The results improve overall team performance from the continual process improvements that are made from sprint to sprint.
Existing knowledge in the company is reused to further build out trade-off curves, and limit diagrams that are linked in decision and causal maps. This makes the work visible and ties the system together to accelerate decision-making. It also narrows the design space so that success is ensured. What makes this valuable is that the planning has positive results, all before a drawing is released.
Leadership and management’s roles are as active leaders and teachers. They are integrated in the process, which requires their active participation in breaking operational barriers for the teams, supporting a mentoring relationship of expertise to drive knowledge acquisition, retention, application, and reuse in central knowledge-capture methods. This also ties them to the decision-based scheduling for the integrated program-review points. Such active involvement of leadership aligns them to the continual improvement actions that the teams identify during the sprint retrospectives, which in turn leads to companywide process improvements.
Adapted by other highly successful and innovative companies, the Lean Agile APQP system is what industry needs to be competitive. More details and information are available, and Omnex is ready to train, consult, and implement the Lean Agile APQP system across industries, government, and community organizations. Omnex will be offering a series of high-energy courses on Lean Agile APQP that will take your product development and leadership teams into a new era of innovation and cost-effective product development. These immersive courses will demonstrate the benefits of Lean Agile APQP, teach the process, and provide insights on how to implement this game-changing process in your organization.
For additional free resources, whitepapers, or webinars please feel free to enter your contact information below. Omnex would be happy to send you relevant information based on your industry and area of interest. (You can fill out the form below.)
Add new comment