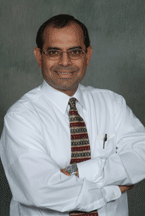
Between 1987 and 1992, the most successful implementation of Six Sigma didn’t require Black Belts or Green Belts. Instead, Six Sigma initiates received training in problem solving, team work, basic quality tools, and statistical tools. However, sense of urgency, dramatic improvement, and teamwork were mandatory requirements for everyone in the organization to practice. In addition, department managers conducted awareness trainings to ensure consistency between their expectations and skills learned. Besides, it was the best way to demonstrate their commitment to their troops.
While evolving into a mature define, measure, analyze, improve, and control (DMAIC) approach for standardizing the Six Sigma implementation process, training has become rote. Training slides are cheap, and anyone can teach Six Sigma. Training standards, content, and effectiveness vary among training providers. One Green Belt training program may include seven to 10 basic quality tools, while the other one may encompass the entire American Society for Quality body of knowledge, which is similar to Black Belt programs. As the number of providers of Six Sigma training grows, how can one ensure effectiveness and return on investment?
…
Add new comment