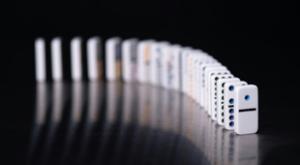
Wed, 02/14/2024 - 12:01
The FMEA (failure modes and effects analysis) turned 75 years old in 2024. However, a look at the literature may paint a different picture. Both the origin year of FMEAs and the name of the organization that developed FMEAs seem to vary among…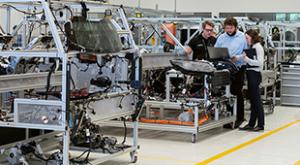
Mon, 01/22/2024 - 12:03
A root cause analysis (RCA) should be empirical; however, this can be difficult when dealing with human error. A typical human failure is a missed operation, such as when a process step isn’t carried out. This could mean a part wasn’t installed, a…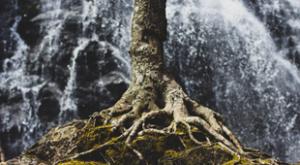
Mon, 01/16/2023 - 12:03
A root case analysis is performed to identify “what, how, and why something happened, thus preventing reoccurrence” (“Root Cause Analysis for Beginners.” Rooney, J. J. and Vanden Heuvel, L. N. Quality Progress 37, 2004, p. 45). This can be difficult…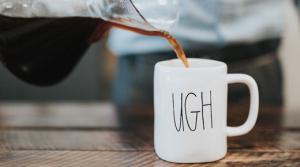
Mon, 10/23/2017 - 12:30
Quality tools can serve many purposes in problem solving. They may be used to assist in decision making, selecting quality improvement projects, and in performing root cause analysis. They provide useful structure to brainstorming sessions, for…
Mon, 06/26/2017 - 12:03
As you drive east on I-70 coming from the Rockies, there is a point where you seem to have stopped descending, but a sign says, “Trucks: Don’t be fooled. Four more miles of steep grades and sharp curves.” The message is that it would be premature to…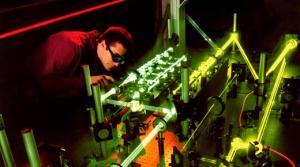
Wed, 06/07/2017 - 12:03
I
n part one of this two-part series, I described the need for empiricism in root cause analysis (RCA). Now, I’ll explain how to achieve empiricism when performing a RCA by combining the scientific method and graphical explorations of data.
The…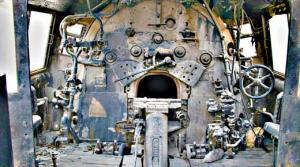
Tue, 06/06/2017 - 12:03
There are many reasons for performing a root cause analysis (RCA). These reasons include determining the cause of a failure in a product or a process as well for determining the root cause of the current level of performance when a product or…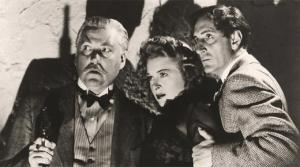
Thu, 04/27/2017 - 12:02
Although not a quality guru, the fictional detective Sherlock Holmes took a methodical approach to problem solving that can be useful when applied to root cause analysis (RCA) during the investigation of a product or process failure.
Sir Arthur… A Worksheet for Ishikawa DiagramsA Perkin tracker combines the benefits of brainstorming with an action-item tracking list
Wed, 03/30/2016 - 14:55
The start of a failure investigation may involve brainstorming, but empirical methods will be required to actually identify a problem's cause. Implementing an improvement action without a confirmed root cause risks a reoccurrence of the issue… Lean Six Sigma: 10 Objections and AnswersCan we stop calling it a fad now?
Tue, 10/13/2015 - 11:37
I gave a rather successful talk on communicating design of experiments (DoE) at the recent ENBIS 14 conference in Linz, Austria. Things went mostly well, but it’s also fair to say many attendees had one major criticism: I didn’t explain why one…