All Features

Mike Richman
QDL always strives to bring you a look at the people and stories making the news in the world of quality. We succeeded admirably on the “people” side of things this week and threw in a fun story about the physics of the basketball to boot. Let’s take a closer look:
“Clarity First Book Review and…

Debashis Sarkar
The cheating at Kobe Steel shook not just Japan but the entire manufacturing world. As Kobe Steel CEO Hiroya Kawasaki revealed, about 500 companies had received its falsely certified products, which affected not only those companies but also its entire supply chain. However, the issue at Kobe was…

Jason Furness
In a previous article I wrote about the reasons why so many lean manufacturing, Six Sigma, and other improvement programs fail. In this article I’m going to expand on reason No. 1: the Academy Award Syndrome.
Academy Award Syndrome
The Academy Award Syndrome is where a program or project is…

Harish Jose
It’s not easy to find topics to write about, and even if I find good topics, it has to pass my threshold level. As I was meditating on this, I started to think about procrastination and ambiguity. So my column today is about the importance of “fuzzy concepts.” I am using the term in a loose sense…

Richard Harpster
Richard Harpster's op-ed is in response to a recent Quality Digest article and webinar discussing the benefits of the draft AIAG-VDA FMEA Handbook. As he points out at the end of this article, the AIAG has provided a means to solicit comments, pro or con, on the handbook. We encourage interested…

Chip Bell
Variation and defects. They are the bane of all manufacturing companies. They signal an absence of efficiency, a neglect of productivity, and a total disregard for cost effectiveness. Who is seen as the rescuing knight in shining armor? Sir Six Sigma!
Fundamentally, Six Sigma (always capitalized,…
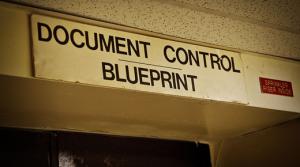
Mike Richman
During the Nov. 3, 2017, episode of QDL, we (figuratively) traveled the globe to bring you quality information. Let’s take a closer look:
“‘Made in Japan’ Falls from Grace Amid Scandals, Systematic Flaws in Manufacturing Industry” Kobe Steel is the latest Japanese manufacturer to admit to…
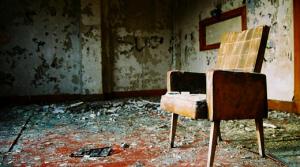
Scott A. Hindle, Donald J. Wheeler
In theory, a production process is always predictable. In practice, however, predictable operation is an achievement that has to be sustained, which is easier said than done. Predictable operation means that the process is doing the best that it can currently do—that it is operating with maximum…
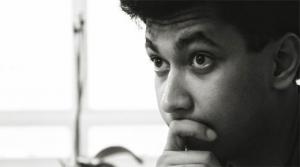
Harish Jose
Today I will look at epistemology at the gemba. Epistemology is the part of philosophy that deals with the theory of knowledge. It tries to answer the questions, “How do we know things, and what are the limits of our knowledge?” I have been learning about epistemology for a while now, and I find…
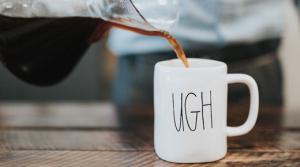
Matthew Barsalou
Quality tools can serve many purposes in problem solving. They may be used to assist in decision making, selecting quality improvement projects, and in performing root cause analysis. They provide useful structure to brainstorming sessions, for communicating information, and for sharing ideas with…

John Flaig
Story update 9/26/2017: The words "distribution of" were inadvertently left out of the last sentence of the second paragraph.
Some practitioners think that if data from a process have a “bell-shaped” histogram, then the system is experiencing only common cause variation (i.e., random variation).…

Mike Richman
QDL from Fri., Sept. 15, 2017, demonstrated that everywhere you look, you’ll find the positive effect of better quality. Here’s what we chatted about:
““U.S. Business Sectors Gain or Hold Steady in Public Esteem”
According to a recent Gallup survey, U.S. citizens’ outlook on a number of industries…

Eston Martz
The Six Sigma quality improvement methodology has lasted for decades because it gets results. Companies in every country around the world, and in every industry, have used this logical, step-by-step method to improve the quality of their processes, products, and services. And they’ve saved…

Eston Martz
Six Sigma is a quality improvement method that businesses have used for decades—because it gets results. A Six Sigma project follows a clearly defined series of steps, and companies in every industry in every country around the world have used this method to resolve problems. Along the way, they’…

Dr T Burns
I had humble, that is, poor, beginnings. I didn’t even know the taste of real ice cream until later in life. One of the first impacts I felt of the luxury that technology brings was the diode my father bought for me to replace the cat’s whisker on my crystal radio. My high school was lovingly…
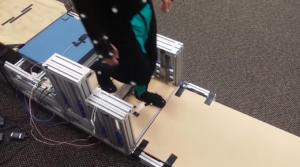
Dirk Dusharme @ Quality Digest
Our August 11, 2017, episode of QDL looked at the role of technology in after-market service, stairs that help you up, Fidget Cubes, and more.
“Climbing Stairs Just Got Easier With Energy-Recycling Steps”
These stairs actually help you go up.
“The Curious Case of the Fidget Cube”
How a product…

Ken Levine, Satish Nargundkar
Completing the define phase of a lean Six Sigma (LSS) project is a critical part of any project, although it’s often underestimated in practice. The define phase of the define, measure, analyze, improve, control (DMAIC) process typically includes three elements. The first is selecting a specific,…

Mike Richman
The June 30, 2017, episode of QDL offered a wrinkle in time, of sorts: not only orbiting debris and medieval medicine, but moments in the here and now such as our interview with Keith Bevan of the Coordinate Metrology Society and the UK’s National Physical Laboratory, and an on-the-go version of…

Douglas C. Fair
Plant-floor quality issues tend to focus on a company’s technical resources. When products fall out of spec, alarms sound and all hands are immediately on deck to fix things. Despite large technology investments to monitor and adjust production processes, manufacturers are still bedeviled by…

Matthew Barsalou, Robert Perkin
As you drive east on I-70 coming from the Rockies, there is a point where you seem to have stopped descending, but a sign says, “Trucks: Don’t be fooled. Four more miles of steep grades and sharp curves.” The message is that it would be premature to relax at this point, and vigilant driving is…

Steve Daum
I have daily conversations with manufacturer plant managers, quality managers, engineers, supervisors, and plant production workers about challenges when using statistical process control (SPC). Of the mistakes I witness in the application of SPC, I’d like to share the five most prevalent; they…
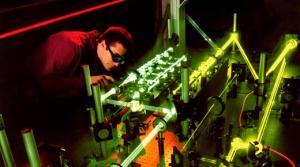
Matthew Barsalou
I
n part one of this two-part series, I described the need for empiricism in root cause analysis (RCA). Now, I’ll explain how to achieve empiricism when performing a RCA by combining the scientific method and graphical explorations of data.
The statistician John Tukey believed data should be…
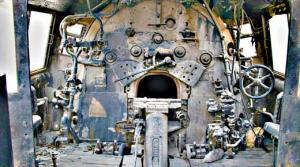
Matthew Barsalou
There are many reasons for performing a root cause analysis (RCA). These reasons include determining the cause of a failure in a product or a process as well for determining the root cause of the current level of performance when a product or process has been selected for improvement.
There are…
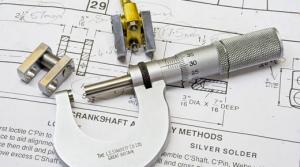
Stefan H. Steiner, R. Jock MacKay
In his February 2017 Quality Digest column, “Don’t We Need Good Measurements?” Donald J. Wheeler recommends that a measurement system contributing up to 80 percent of the overall variation (on the variance scale) is good enough to detect persistent mean shifts when using a process behavior (…

Harish Jose
I have been reading a lot these days about Western philosophy. The most recent book, All Life is Problem Solving (Routledge, 2001), is by Karl Popper, one of the great philosophers of the 20th century. This is a collection of Popper’s writings. One of the great teachings from Popper is the concept…