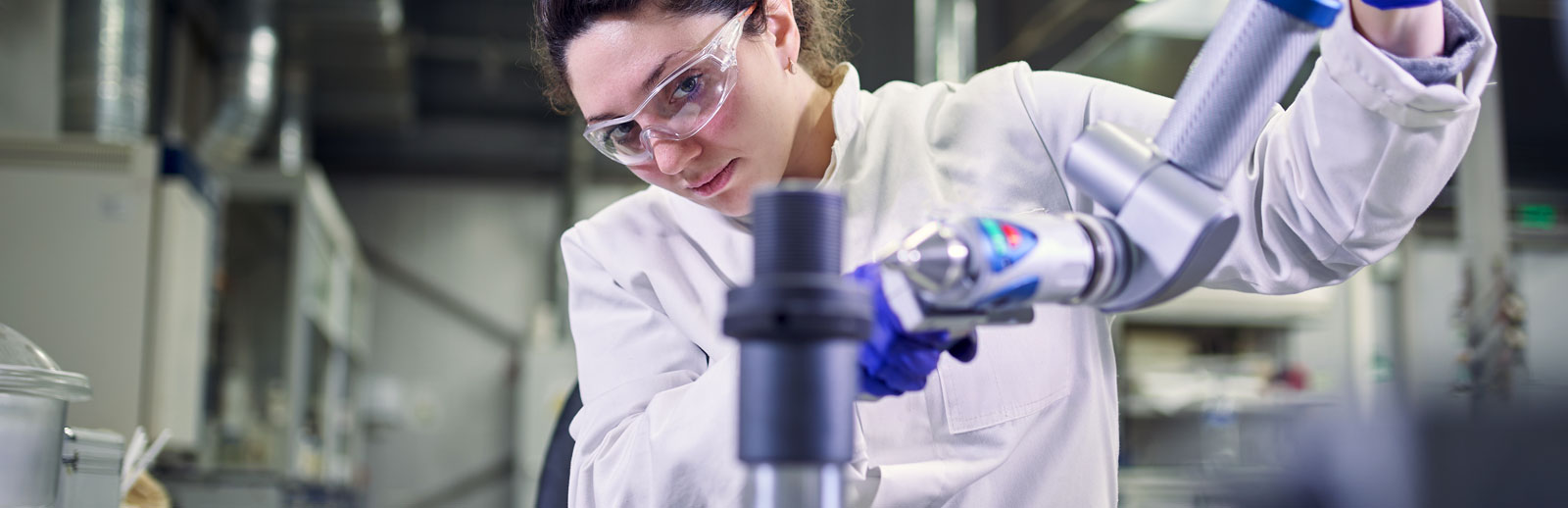
No matter which quality management methodology, technique, or fad du jour you chose during the past 40 years, from quality circles to TQM to Six Sigma, all had one thing in common: data. In manufacturing this eventually meant measurement data. Whether it was dimensional, time, temperature, frequency, pressure, or some other metric, somewhere in manufacturing somebody used measurement equipment to verify the quality characteristics of the part being manufactured. This person was typically a specialist either by profession or experience.
This specialization prevented the goal of modern quality, which is that quality is everyone’s job. How can a manufacturing employee be part of quality if they can’t measure their own work or verify the parts they’re assembling? And yet, that’s the way it’s been since the beginning of the Industrial Revolution. Assemblers assemble and testers test. Yes, eventually line workers got go/no go gauges, snap gauges, and some simple dimensional tools, but assembly complexity grew faster than the ability of the tools used by the average worker. It’s like giving a carpenter a stack of precut lumber, a box of nails, plans for a house… but no measure.
…
Add new comment