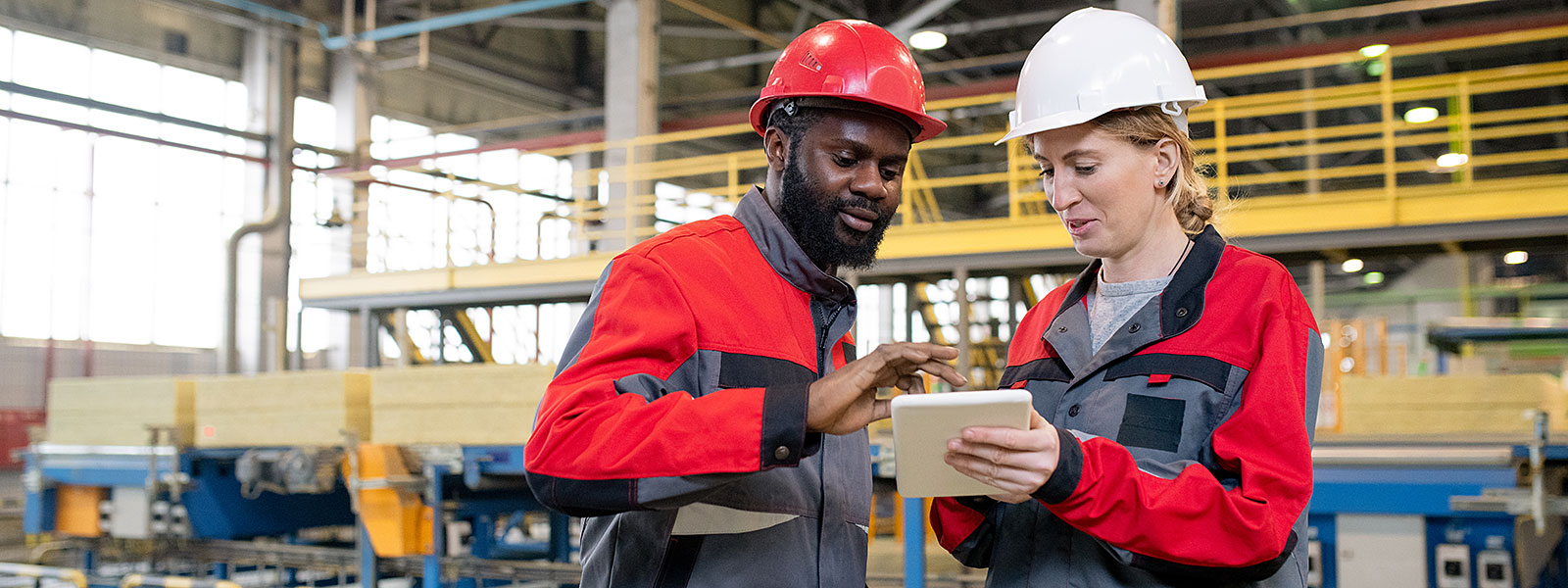
Before we get into a case study about how enterprisewide SPC software would work on both the shop floor and the C-suite, let’s talk about a long-held bias about “blue-collar” workers: That because they’ve traditionally been associated with manual labor, they should use manual tools; “white-collar” front-office workers, on the other hand, need the slick technology tools.
Imagine walking around the offices of a large manufacturing organization and finding salespeople managing customers’ information using a Rolodex. In a planning meeting, the CEO is using acetates on an overhead projector. In the procurement office, staff are issuing purchase orders using a Telex machine.
Now imagine walking the plant floor at that same manufacturer. The production supervisor is writing machine settings for the next shift on a board next to the machine. The quality engineer is writing the results of a critical quality check on a clipboard with a blunt pencil. A bunch of people stand around murmuring, scratching their heads, and wondering why a machine isn’t working properly.
In the first example, you might think you’d traveled back in time. The scenes are absurd. But the second example is a common reality.
In many manufacturing organizations, this level of disparity between the plant floor and the back office still exists. The office workers have all the technology they need, while the plant floor makes do with outdated methods and technology.
But the line is blurring—even being erased—and the change is bringing dramatic improvements. When it comes to technology usage, there is no longer a clear delineation between “white-collar” office workers and “blue-collar” plant workers. Regardless of their location, manufacturing professionals now all use (and require) modern information technology and applications to do their jobs effectively and keep up with today’s demands on manufacturing.
Digital transformation for the tools of the trade: Empowerment and engagement
In the traditions of the past century, white-collar tools of the trade focused on ”mental” work—reports, endless meetings, and planning and strategizing. And to support those functions, we adopted myriad enterprise applications with a dizzying array of acronyms: ERP, MES, CRM, BI, CMS, BPM, and many other TLAs!
Blue-collar tools of the trade were based on manual labor—a pair of greasy overalls, a wrench, a can-do attitude, and maybe a lunch pail. Get your orders for the day and hit the plant floor. Let the white collars worry about where the company is going and how it’s going to get there.
As manufacturing has evolved, so has the front line—the plant floor. Operators work with highly automated and finely tuned equipment in today’s manufacturing environment. They remain on the plant floor, fixing machines when something goes wrong, monitoring and adjusting processes, performing quality checks—you know, essentially the pulse of the operation. But they increasingly do their work with digitally enabled quality control technologies.
Most plant-floor workers have been adapting to a digital environment over time, climbing up the ladder and advancing their skills. The wrench has been replaced with a tablet, the overalls now a crisp uniform. Many manufacturing professionals straddle the line between the office and the plant floor, working with human-machine interfaces as well as supervisory control and data acquisition systems and the like. They know the difference between ERP and MES as well (or maybe better) than their bosses.
But here’s the rub: They still don’t have access to anywhere near the same information technology capabilities as their back-office colleagues.
Modern manufacturing professionals need the right modern manufacturing tools
Imagine a quality manager in a queue to buy lunch. He can bring up social media and see what his friends ate for dinner last night halfway around the world. Yet he can’t see what the quality performance of line 3 was during shift 2, unless he goes and takes a look at that clipboard!
There was once a concern that if you introduced technology to blue-collar workers, you would then have to teach them how to use a mouse and a keyboard, and they would all be just a bit intimidated by it. That’s not the case, probably never was. Today's workers in every role are extremely technology literate. They have grown up with technology and are therefore more familiar and comfortable with it. And they often have an aptitude for learning to work with new technology, be it hardware or software.
In their personal lives, the world is at their fingertips. Do they want to know the football score? No problem. They just pull out their smartphone and open the app that gives them their sports information. They might share it with friends via social media, comment on it, and then while they’re at it, see what the rest of the family is doing on their trip to Australia, checking out photos and messages from them. They’re an aware workforce—socially, technically, and professionally. And technology, rather than being an alien thing, is just the opposite. Try taking a smartphone away from a younger worker, and she will act and feel like she’s had a limb removed.
Technology in the workplace, for these shades-of-blue workers, is no longer a hurdle to overcome; it’s an expectation—both for them and for the organizations that employ them. It’s a bit strange to them when technology is not available to enable their work and empower them to be engaged.
Where is this going?
So, let’s look at this from the manufacturers’ perspective. If you’ve got people who are more adept at the technology and more inclined to use the information it provides them to make better decisions, then what you have is a knowledge worker. If you have these people in your employ, why would you want to hold them back by not giving them the tools they need to shine or flourish in their roles?
Think about it. You’ve got this wonderfully technology-literate person who uses IT in all aspects of his life. But when he comes to work, he has to write things down with pencil on paper and try to extract some meaning from it without the right tools? It no longer makes any sense.
Can you feel the sands shifting? Manufacturing is moving away from blue- and white-collar designations and blurring the lines between “types” of workers to one, indivisible knowledge worker, not only capable of handling technology, but also expecting it and asking for it.
Modern manufacturing with intelligent quality solutions
Are you considered a blue-collar or white-collar worker? Do you work with your hands or your mind? Are you the brains of the operation or the brawn? Good news: If you feel that you are neither, or both, or that these terms no longer apply, then you are not alone. You are a modern manufacturing professional.
What we do here at InfinityQS—quality intelligence with statistical process control (SPC) software—is right in the middle of this profound change. InfinityQS quality solutions, powered by our industry-leading SPC engine, deliver unparalleled visibility into your processes and intelligence to lead you on the path to continuous improvement.
With our solutions, manufacturers gain strategic insights to make data-driven decisions that improve product quality, decrease costs and risk, and meet compliance requirements. InfinityQS enables today’s manufacturers to convert quality from a problem into a competitive advantage.
It’s time to embrace the future. Welcome engaged, savvy workers into your manufacturing world, give them the tools they need to do their jobs—and watch your business transform for the better.
In the next article we’ll see a case study of how a comprehensive, enterprisewide SPC software gives both the shop-floor quality manager and the corporate quality professional in the C suite the tools they need for data collection and analysis to grapple with the issues that matter most to each of them.
As manufacturing looks toward the future, organizations need to support agile operations and not just manage quality but master it. InfinityQS provides solutions to empower workers with information and insights no matter where they are, optimize operations and productivity, and adapt to rapid changes. Please visit our website to learn more about our Enact Quality Intelligence platform.
Add new comment