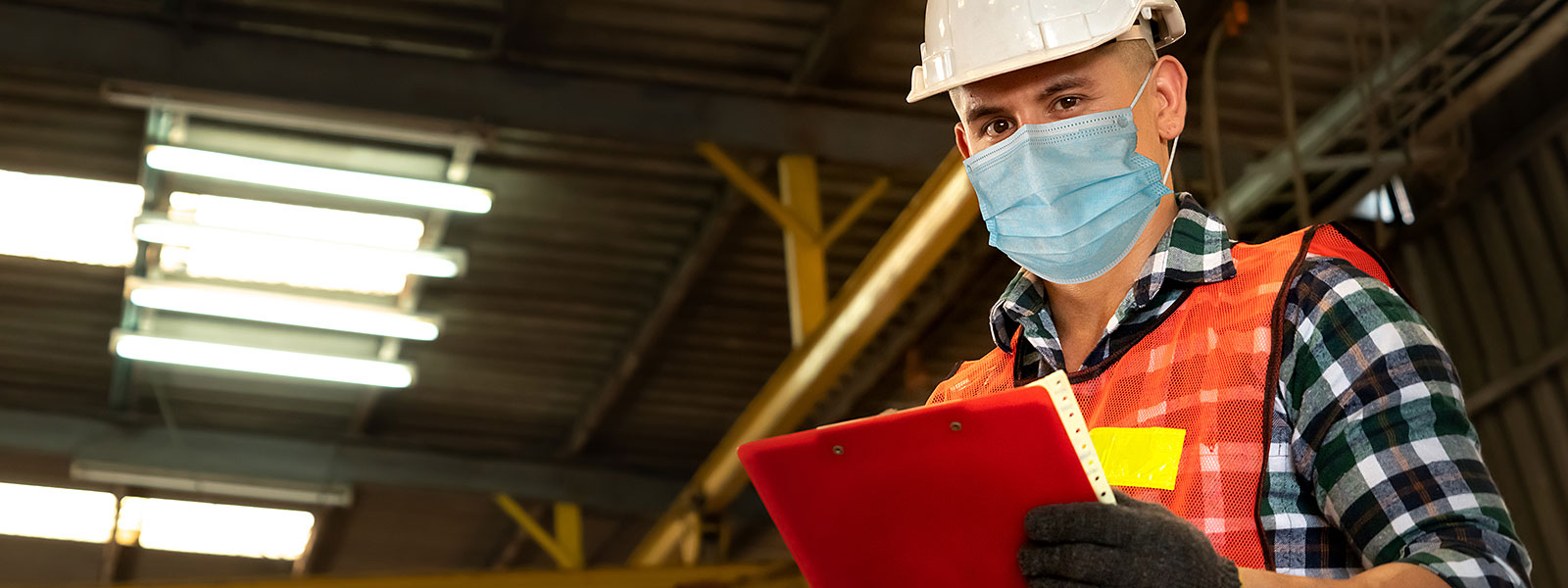
In recent months, we’ve learned that manufacturing during a global health crisis puts organizations under immense pressure to maintain operational efficiency while upholding product quality and employee safety.
Initially, organizations focused simply on taking the steps required to survive. However, as organizations around the globe have pivoted to overcome those initial challenges, manufacturers are taking the opportunity to explore how they will not just survive but become more resilient—even thrive—going forward.
Recent operational challenges have shined a light on existing process weaknesses and technology limitations. Manufacturers are taking their cue and proactively identifying opportunities to optimize processes, empower workers, and make operations across the organization more effective.
Enact, InfinityQS’ cloud-native quality intelligence platform, offers plant leadership a variety of ways to make their operations more effective. Here are six Enact benefits that can help your organization make critical shifts that are necessary for the future of manufacturing.
1. Focus on exceptions
When there’s an issue on your production line—a specification limit or statistical violation—you want your people to be able to respond quickly, resolve the issue, and move on. Right? Everyone on the plant floor doesn’t need to know about it. Just the operator on the line in question, the supervisor, and maybe the quality manager—the people who can take direct action.
At InfinityQS, we’ve advocated exception reporting for decades. We understand that software needs to tell you when there’s a problem—but if there’s not a problem, you’ll probably have better things to do. From the operator’s viewpoint, his regular job is not typing information into a quality system; it’s not looking at a bunch of charts; it’s certainly not digging into reports. His job is to measure the process regularly and then find out very quickly after he enters those data, “Do I need to respond to this? Do I need to adjust anything? Yes or no?” If the answer is no, then he can get on with his work.
That’s where exception-based reporting comes in. Focusing on exceptions is often a paradigm shift for manufacturers. Old habits die hard. But rather than forcing operators to sift through pages of data or shuffle through dozens of Paretos charts or box-and-whisker plots, we bring to their attention, or “surface,” only the issues that they need to care about. That way they can focus on performing the most important aspect of their job—manufacturing consistent, high-quality products for your company.
With Enact’s exception-based reporting, when a product or process demonstrates unexpected behavior like excessive variation, the appropriate people are notified. They are not inundated with extraneous information; they just receive notification of the exact issue.
Figure 1: Enact dashboards display relevant, role- and task-based information to help users stay focused on critical tasks.
2. Promote accountability with event workflows
In manufacturing, the term “workflow” describes a sequence of processes from initiation to completion. An event workflow in Enact provides rules and guidance for responding to:
• Data violations, including manufacturing limits (e.g., specification, reasonable limits, net content control limits), statistical violations, and so on
• Timing violations such as missed or late data collections and checklists
You define the events, and the workflows then enable operators, quality engineers, supervisors, and others to respond consistently and effectively to process- and quality-related events.
Workflows also capture valuable contextual information that can be used by anyone in your organization to better manage or prevent similar events in the future. It’s a great use of technology to strengthen any team or organization.
And it’s a great way to ensure that your people are doing the things you need them to do in response to issues. Accountability through workflows keeps everyone on the same page.
3. Enjoy the benefits of centralized quality management
In years past, you could get away with not having centralized management for your quality efforts. Every plant operated autonomously—and any changes, improvements, or best practices happened in silos—but no longer.
A thriving future for manufacturing requires manufacturers to be nimble and responsive. That means you must examine what’s happening in real time in your plants, come to a decision on what to do about it (or not do), and implement your decision. Quickly.
To do that, you need centralized data, and a cloud-based quality management solution makes that possible. All data from all products, lines, and sites are stored and standardized in a centralized, secure unified data repository. Likewise, when you need to make a change—for example, disseminate information, implement a best practice, or provide instructions—you apply that change in the centralized software. Once.
You don’t have to train everyone to do everything. Your people don’t need to know how to reconfigure your quality software when something changes. You can make quick decisions about a new part, quality check, or configuration and enable it centrally. A few administrators. One action. Everyone sees it on the plant floor. Done.
This reduces the burden on your plant personnel and your time-starved operators (who really shouldn’t be doing this sort of thing anyway) and makes you more agile. Let's say upper management decides to make a new product; call it Product A. An administrator enters all the information for Product A into the software, and all the operators instantly see that Product A is now available to select when they start their shift. Congratulations! Product A was so successful, we’re making a Product B!
Now your operators can concentrate on what they do best: making your high-quality, consistently manufactured products. A centralized team means you don’t need administrators at each site; overall, that’s a more effective way to configure and maintain a centralized system.
4. Cross-train employees to boost flexibility
How do you simplify end-user training so that it’s easy for employees to be quickly cross-trained and thus more flexible? Start with a system that enables consistency.
In Enact dashboards provide a consistent, visual interface. As we’ve already noted, the centrally configured interface saves time for both users and the person configuring the system. When everyone uses the same dashboards, you are guaranteed that they are all using the same analysis and metrics as well.
In addition, although the dashboards are configured to look the same, their contents may change depending on which user is viewing them and what they’re currently responsible for.
So, if you want to cross-train an operator to manage line 2 in addition to line 1, no problem. The dashboard will evoke the same muscle memory, even though the information the operator will deal with may be different. The important thing is that when she’s responsible for line 1, she will see line 1 data, notifications, and alerts.
And how is this making your employees more flexible? Well, when the operator for line 1 is away from the plant floor, the operator from line 2 can quickly and easily cover. When an employee is ill, you can rest assured that the duties of that employee are fulfilled by another. And so on. There’s nothing for the fill-in operator to interpret; simple, consistent, exception-based reporting takes the guesswork out of the information he sees.
You can see how in times of uncertainty Enact can virtually expand your workforce to cover all your lines.
5. Eliminate time-consuming ‘data pulls’
In site-level quality departments, the folks who address “putting out fires” with customers also tend to be the data-pullers. When a customer, regional executive, or auditor needs a specific report, they pull and cull what they need from whatever system is in use, export it to a spreadsheet, format it, and then send it out—probably with an explanation to aid the recipient in interpreting the data. Painful. Time-consuming.
With access to Enact, supervisors and management can see whatever they need to see right in the software, with just a few mouse clicks. They have data right at their fingertips... all the time. Whenever they need it.
Imagine how great that will be. When supervisors or corporate management need data, they have no need to knock on anyone’s door or walk down to the plant floor.
Everyone gets to focus on what they do best, resting in the knowledge that the information is there whenever they want to see it. Operators take care of the lines; corporate can take care of corporate. Efficient. Burden lifted.
6. Get the benefits of an electronic system in more places
In some manufacturing facilities, workstations on the plant floor are in enclosures that protect them from extreme temperature, moisture, dust, or caustic elements. The enclosures sometimes cost three, four, or five times what the technology housed inside costs. That’s crazy when you think about it.
As a result, the number of instances of quality software is limited to the number of enclosures you want to pay for. Other limitations may arise if you need to add an ethernet cable for a dedicated computer.
With a mobile system like Enact, these issues disappear. Because Enact is browser-based, all you need are wireless access points. Now you can have as many devices as you need. Tablets are typically much cheaper than dedicated PCs, and they can either be kept in protective cases or simply removed from the area for cleaning.
Recovery doesn’t mean going back to the way things were before
The history of manufacturing is filled with stories of disruption and adaptation. Today, manufacturers clearly understand that their futures depend not on restoring business as it was, but on building a resilient operation that is prepared for the next disruption.
That’s a goal worth striving for. Why not make your manufacturing organization the best it can be?
As manufacturing looks toward the future, organizations need to support agile operations and not just manage quality but master it. InfinityQS provides solutions to empower workers with information and insights no matter where they are, optimize operations and productivity, and adapt to rapid changes. Please visit our website to learn more about our Enact Quality Intelligence platform.
Add new comment