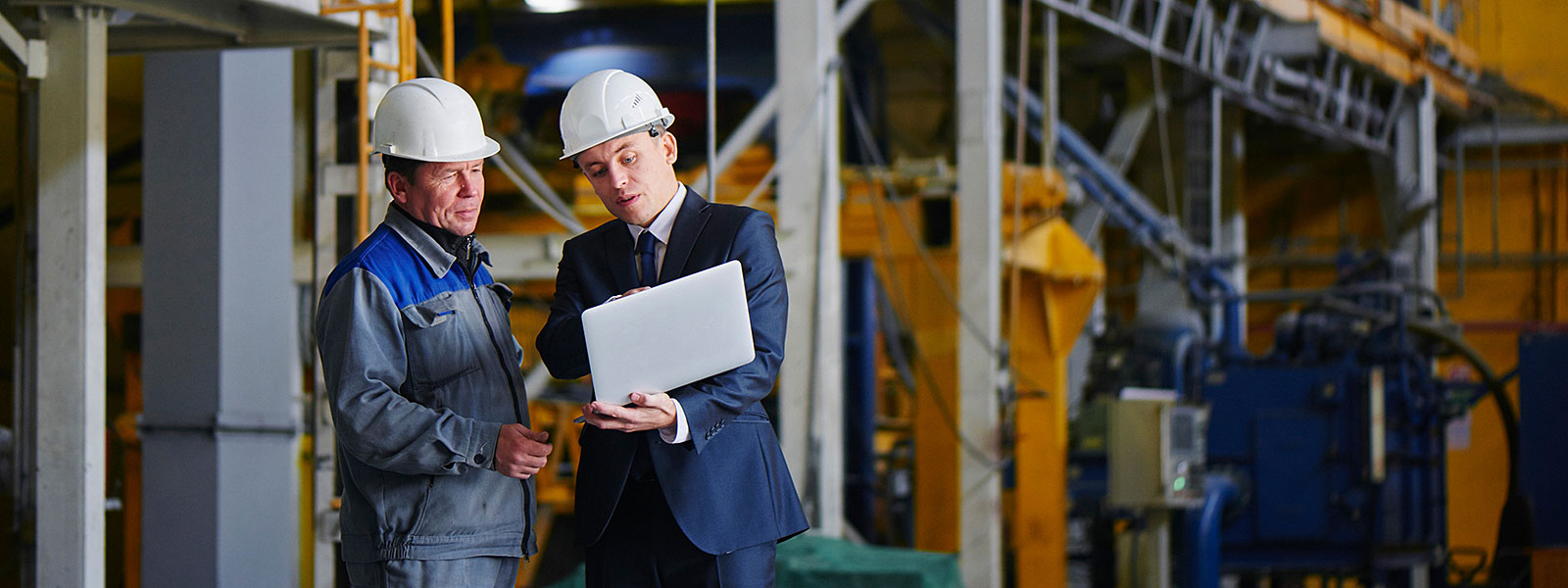
The idea of digital transformation can be scary. The growth of technology is outpacing a comfortable pace of adoption for many manufacturers. But remaining content with the status quo often means being left behind. Digital transformation has become an imperative to give manufacturing organizations the flexibility and agility required to overcome business disruptions and adapt to rapidly changing and demanding global markets.
Digital transformation of quality management is a process that depends on something you already have: quality data. Your quality management system is key to optimizing all your quality operations, including supplier and materials management, production processes, quality checks, packaging, and shipping.
InfinityQS calls this holistic approach “manufacturing optimization.” It starts with improving the way you use data to answer the strategic, big-picture questions that truly matter to your business.
Limits of the status quo
The barriers to transformation are often a result of operational and resource challenges that typically boil down to one thing: everyone’s plate is already full. Whether managing and maintaining servers and IT projects, or running day-to-day production, no one has the time to take on new transformation projects.
And transformation projects are perceived as being large-scale, costly, and complex. Many organizations are concerned that such projects will compete with budget constraints—and take scarce resources away from other projects.
However, consider the costs you incur by sticking with your existing methods and systems. When InfinityQS consults with manufactures about how they answer strategic questions about production or companywide concerns, we start by asking them to explain, “How would you do that today?”
The responses often involve a long string of labor-intensive tasks that require exporting data to spreadsheets, transforming disparate data to a standardized format, and performing numerous manual manipulations and calculations. Often the result is still, “We don’t have a way to answer that for the entire organization.”
Those time-consuming processes aren’t working anymore, and they are severely limiting your ability to be agile and responsive. Switching to a cost-effective, flexible software-as-a-service (SaaS) solution empowers manufacturing optimization and agility. With a SaaS product like InfinityQS’ Enact quality intelligence platform, you can be nimble in making strategic, data-driven decisions. And you can respond more quickly to market dynamics.
Simplifying answers to the big questions
That starter question, “How would you do that today?” might seem a bit nebulous. Let’s get more specific. The four big-picture problems we commonly discuss are:
• How do you identify your biggest opportunities for process and product quality improvement?
• Once you’ve identified those opportunities, how do you prioritize your resources to address them?
• How do you know people are collecting the data they are supposed to collect?
• How do you know what your biggest challenges are?
These are all tough questions for people to answer because they require an enterprisewide view of quality data and assurance of consistency in data collection and analysis. Luckily, Enact can help answer these questions because it is a platform that provides the necessary visibility and consistency.
Identifying opportunities
The first question we ask, “How do you identify your biggest opportunities for process and product quality improvement?” is the starting point for all the questions that follow. It requires having access to all the data from across your organization as well as the ability to effectively analyze those data.
In your average manufacturing environment, there are lots of machines and data collection devices as well as personnel capturing data manually, and each data source speaks its own unique language. Enact can hear what each source is saying, translate it into a common language (or format), and store everything in one place. From this centralized repository, built-in analytics enable you to aggregate, roll up, and slice and dice your data in many useful ways.
With Enact, you can look at large swaths of time and thereby uncover trends and potential problems down the road. As an example, let’s look at one of the newest additions to Enact: bubble charts.
What makes Enact bubble charts such an important tool for you? They are the intersection of the two fundamental questions most manufacturers ask of any quality intelligence platform:
• Are we collecting all the data we’re supposed to be collecting?
• Are our measurements “good,” that is, do the measurements meet specifications?
How are you answering those questions today?
Bubble charts provide the answers in a quick snapshot. Here is a bubble chart that shows the percentage of on-time data collections and expected yield for all critical features across 11 manufacturing sites:
Figure 1: Sample enact bubble chart
In this example, which sites needs help with its data collection? Which sites are struggling with yield? You can see how beneficial it is to be able to instantly identify where to start your quality improvement efforts.
Prioritizing resources
Our next question was, “Once you’ve identified improvement opportunities, how do you prioritize your resources to address them?”
We address this need with Enact’s stream-grading feature. Stream grading provides a unique way to roll up and interpret performance across products, processes, and sites. It’s a great tool for quality professionals who are ready to dig deeper into data than they ever have before—but need an effective way to prioritize their efforts.
As you can see in the graphic below, stream grading is color-coded and extremely easy to read and use, enabling you to know not only where to prioritize your resources, but also what level of effort is likely required.
Figure 2: Sample enact site summary tile
This site summary tile shows each critical feature in its own column and a row for each site. You can sort the columns by performance and then click on an individual cell to drill down and learn more about the individual processes and parts that resulted in that grade. You can quickly learn which facility or production process needs prioritized attention.
How would you do that today?
Data collection in the crosshairs
Let’s shift gears from process and product improvement to another fundamental question: “How do you know people are collecting the data they are supposed to collect?”
How are you finding that out today?
Companies almost invariably respond by asking, “Can’t you just give me a list of all the data collections that people did today? Then I can see how many they missed.” The response to that is, “Yes, but how do you know how many should have happened?”
The answer to this line of questioning is timed data collections. If you look at most data collection forms (whether paper or electronic), there is typically a column for “time” that specifies a check at 8 a.m., 9 a.m., and so on. If that’s the case, you already have implied timed data collections and you’re relying on operators to correctly fill in the forms that you provide, on time, and according to your specifications. Do you imagine that those forms are accurate?
Timed data collections ensure that data are collected when they should be. (Was that 8 a.m. check really performed at 8, or was it 8:17?) They also provide a visual countdown, so operators don’t worry about when the next collection is due. Timed data collections ensure that operators can focus on doing what they do best—running your production line—and are alerted when it’s time to perform a data collection.
Timed data collections give quality personnel and management peace of mind because they know that data are being collected consistently, correctly, and on time. When a collection is missed, the appropriate people are notified, reasons are entered to explain the miscue (there are perfectly legitimate reasons for missing data collections, and you want to know about them), and you’ve got a clear list of how many data collections were on-time, missed, and late.
Meeting challenges
Our final question is: “How do you know what your biggest challenges are?”
To pursue this question, let’s consider that a manufacturer sees the answers from our previous question and says, “I want to know why we are missing timed data collections.” That sounds like an excellent opportunity for a Pareto chart, which can show how many times each line missed checks and the reasons they missed them.
That’s an example of exception-based reporting.
Consider how you answer similar questions today:
• Where am I having the most spec-limit violations?
• Why am I having those spec-limit violations?
• Where and why am I having the most statistical violations?
Now, to all those questions, add “...across all of our production lines at all of our sites.”
The power of exception-based reporting is that it enables you to ask questions you never would have asked before—because the answers seemed nearly impossible to find.
Focusing on exceptions is a paradigm shift for manufacturers. Exception-based reporting in Enact takes place on role-based dashboards. Instead of looking for information in a wall of control charts—and likely missing what’s important—the dashboard surfaces meaningful information that’s relevant to that user’s role and tasks.
Dashboards enable the kind of analysis that manufacturers can really appreciate. You can make valuable comparisons with a dashboard in a few clicks of the mouse. And that can only be better for your operations. Rather than slogging through compilations and calculations once a quarter to see how everyone is doing, isn’t it better to just know how everyone is doing all the time?
Figure 3: Sample Enact exception-based reporting dashboard
Your dashboard in Enact can show you statistical violations and missed data checks—two very different things, with different actions to take—side by side on your dashboard. It’s a one-stop-shop, one place to look, providing big time savings and greater efficiency.
Overcoming barriers and moving toward transformation
The good news? The answer we usually give to, “How would you do that today?” is, “We can help you with that.”
With a tool like Enact, you can achieve greater levels of real-time operational visibility. And with that increased visibility, you can see past all the gaps or blind spots within production and quality operations. Your decision-making becomes better informed based on accurate, reliable data.
Then, you can begin to transform your enterprise by optimizing your manufacturing operations—without disruption or overuse of your resources. Enact breaks through the barriers and enables a very different approach to transformation.
As manufacturing looks toward the future, organizations need to support agile operations and not just manage quality but master it. InfinityQS provides solutions to empower workers with information and insights no matter where they are, optimize operations and productivity, and adapt to rapid changes. Please visit our website to learn more about our Enact Quality Intelligence platform.
Add new comment