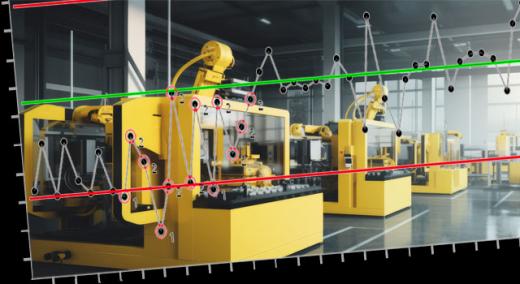
Today’s manufacturing systems have become more automated, data-driven, and sophisticated than ever before. Visit any modern shop floor and you’ll find a plethora of IT systems, HMIs, PLC data streams, machine controllers, engineering support, and other digital initiatives, all vying to improve manufacturing quality and efficiencies.
ADVERTISEMENT |
That begs these questions: With all this technology, is statistical process control (SPC) still relevant? Is SPC even needed anymore? Some believe manufacturing sophistication trumps SPC technologies that were invented 100 years ago. But is that true?
We the authors believe that SPC is indeed relevant today and can be a vitally important aid to manufacturing. (SPC can be used outside of manufacturing, and to great benefit, but we keep our focus on manufacturing.)
…
Comments
Over-Datafication
Thank-you...thank-you....thank-you for a great article addressing Over-Datafication ( a term I coined several years ago). I worked in the Pulp and Paper Industry for 47 years. It always amazed me that vendors of data collection systems often used ferquency of data as a selling point. "Wouldn't it be fantastic if we could get a measurement every 10 seconds instead of every 10 minutes?". Of course, this comes five years after they sold us the current system with "Wouldn't it be fantastic if we could get a measurement every 10 minutes instead of once per hour?" etc., ect., etc., ad nauseum. Over-Datafication occurs when the data is collected much faster than the process can change and the data becimes severely auto-correlated, making it useless for analysis of the "voice of the process". I once mentored a Six-Sigma Black Belt candidate doing a project in a pulp mill. He was taking automated data (temperature) of a process stream which needed to be controlled within a few degrees. The data collection frequency was every 30 seconds. However, the Control Chart based on this data turned out to be useless in helping the operators control the temperature of this process stream. It turned out that the data was very auto-correlated - the data were nowhere near independent of each other. We changed the data frequency to every half hour and the Control Chart became a great tool for the operators. Temperature variability was reduced over 50% and temperature excursions outside the specification limits became almost non-existant. Due to Over-Datafication, many industries are drowning in data, but starved of information. Data is useless if it cannot be turned intoo information. Note: Auto-correlated data makes Control Charting very difficult because the calculated upper and lower control limits become way too tight and most of the data is outside thos limits.
Over-Datafication
Thanks, Steve, for the valuable comments and the term (not heard it before). Hopefully our upcoming Part three will be a good one to put a bit more meat on the bone to your comments on how to use data in a way that makes sense, bring useful knowledge and information to the operation. Keep a look out for this one and let us know your thoughts/ideas to it.
Let's Reconnect
Scott, Let's reconnect: gandydancerz@hotmail.com
Of course it is
Even if it weren't (in manufacturing), it would still be in service, where volumes are lower and slower for the most part, and automation isn't as widely used. But of course it is still relevant, for the reasons you enumerated in this article.
I had a guy try to tell me a couple of years ago that his automated systems measure every part, and adjust the machine accordingly. I told him that that would be OK if the measurements were going into an algorithm like a control chart, so the automated adjustments wouldn't just constitute high-speed tampering and driving variation up quickly.
Add new comment