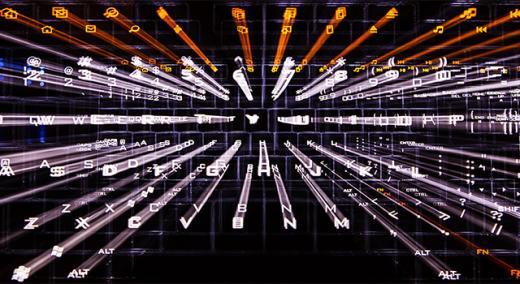
“Information Overload” Credit: James Marvin Phelps
Data overload has become a common malady. Modern data collection technologies and low-cost database storage have motivated companies to collect data on almost everything. The result? Data overload. Unfortunately, few companies leverage the information hidden away in those terabytes of data.
ADVERTISEMENT |
There are inherent challenges in managing large volumes of data, not the least of which is how to extract meaningful information from those data or calculate returns on investment for those systems. Invariably, some well-meaning person will ask for a control chart using data that are gathered in millisecond increments. That presents a series of problems. Building on Part 2, this article is written to reveal practical ways of creating meaningful control charts and analyses from mountains of data.
…
Comments
Another approach for charting temperature
Hi Doug,
I have been greatly enjoying your series of articles.
Another way to track the temperature data when 15 measurements form a subgroup is to use a 3-D X & MR chart. The standard deviation of the 15 readings is plotted on the bottom (S) chart, the average of the 15 on the top (X) chart, and the moving range of two consecutive averages (Xs) on the middle (MR) chart.
Take care and keep writing these interseting, and timely, articles!
Davis Bothe
Three-Way Chart
David Bothe!
Your suggestion refers to the so-called Three-Way Charts (invented by Dr. Wheeler).
SPC for High speed data
One may use CUSUM control on qualit attributes for which data collection is periodic usually in lab parameters. It can supplement PID conrol.
Elaborations for strategy 1?
As you write, the advice for strategy 1 are somewhat nonspecidic. Any further suggestions on how you could spot when a sampling plan is not "just right"?
"Just right"
Hi Robert, good question…
First of all, be clear on what you want to achieve, or which questions you are looking to answer. As an example, you might want to learn if the process remains stable and predictable when you change a raw material batch or supplier, or change to a different upstream feed tank, or change production shift …? Be clear that your sampling plan convinces you the question/s of interest can be answered.
I learnt from Donald Wheeler many years ago that “so long as you have signals you have enough data” … if you have signals (on your control chart) you have detected process changes that are worthy of investigation – investigate, learn what you can, and take action.
If your signals come from a chart looking like Figure 1 above you are probably sampling too fast. Use your knowledge of the process to “best guess” how quickly your process can change … (ask the shop floor what they think and get them involved). If you think, for example, that meaningful process changes cannot occur at a faster rate than every 10 minutes then don’t sample much quicker than this.
As Doug writes above, challenge your current sampling plan and adapt it to correct the weak points in it that you identify. You may not find a weak point today, but you may tomorrow. When you find the weak point adapt things accordingly.
Add new comment