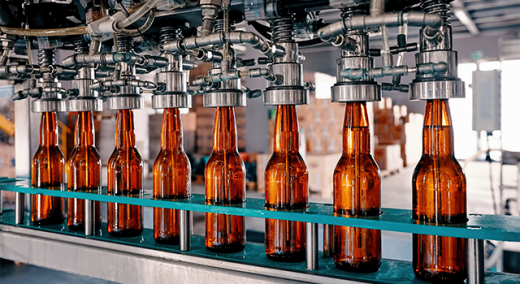
Parts 1, 2, and 3 of our series on statistical process control (SPC) have shown how data can be thoughtfully used to enable learning and improvement—and consequently, better product quality and lower production costs. Another area of SPC to tap into is that of measurement methods. How do we ensure that the measurement data we get provide us with accurate process and product insight? Read on to see how SPC techniques play this key role as well as generating actionable and profitable insights from your data.
ADVERTISEMENT |
Measurement consistency
Standard samples are routinely measured as part of measurement monitoring programs, and an essential property of such samples is that they don’t change over time. (If the standard sample is of value 10 on Day 1, it retains the value 10 on days 2, 3, 4... and so on.) A commonly used standard is a reference weight, because reference weights don’t change unless they are damaged or poorly handled.
…
Comments
Measurement Data and Getting the Basics Right Part 4
Hi Scott,
Have done done similar many times and especially the application on making margarine, engine manufacturing, and bio-medical labs.
As mentioned earlier in my comments, I wish those U/LCL lines were reflecting the Voice of the Process and be dotted and not full lines.
Secondly, I find the placement of the Histogram to the right of the Control Chart is valuable for understanding the distribution but then on it, placing the U/LSL and seeing where the Control Cart readings fall into the Voice of the Customer.
Mike
Measurement Data and Getting the Basics Right Part 4
Hi Scott,
Have done done similar many times and especially the application on making margarine, engine manufacturing, and bio-medical labs.
As mentioned earlier in my comments, I wish those U/LCL lines were reflecting the Voice of the Process and be dotted and not full lines.
Secondly, I find the placement of the Histogram to the right of the Control Chart is valuable for understanding the distribution but then on it, placing the U/LSL and seeing where the Control Cart readings fall into the Voice of the Customer.
Mike
Mike
Thanks for the comments and happy to hear you have successfully applied the ideas discussed above in your work.
Dotted/dashed lines .... In all these years I'd never paid much attention to the process limits being solid or dashed. I see in Shewhart's 1931 and 1939 books they are dashed. My main focus, or concern, has tended to be that the two voices (process & customer) are understood, i.e. why they are different and what they represent.
Add new comment