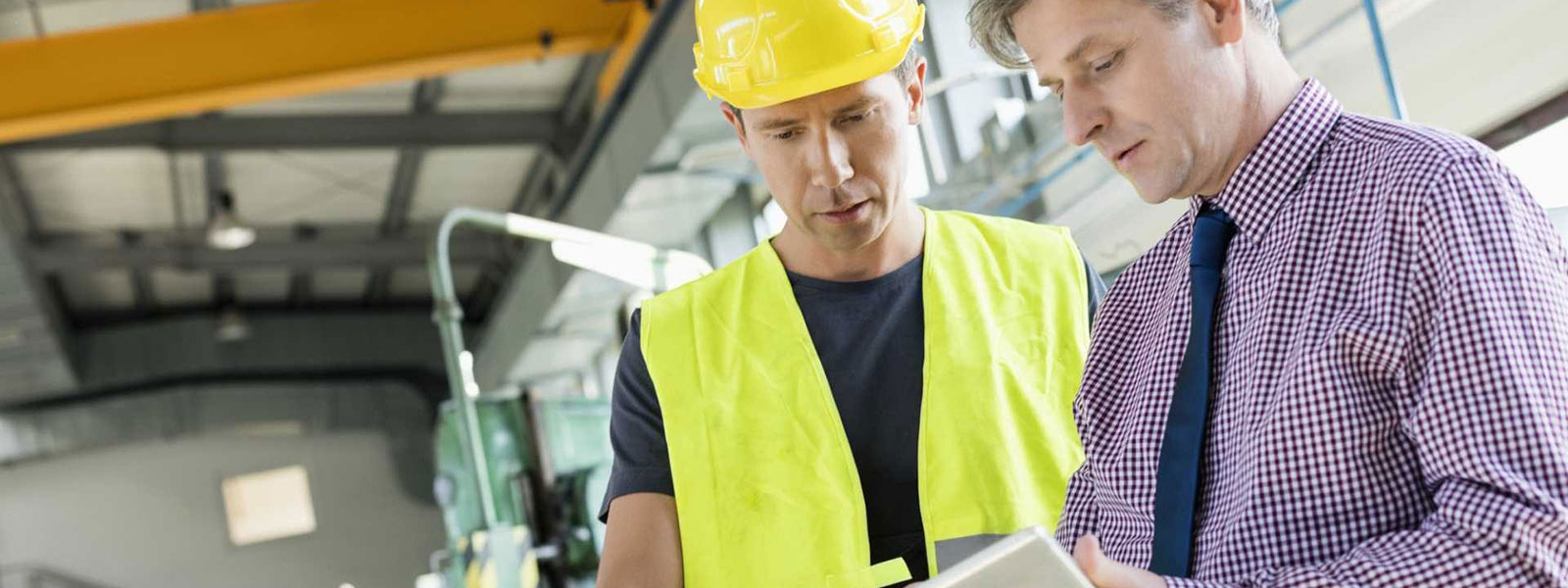
The importance of data analysis in manufacturing operations can’t be overstated. Over the years, manufacturers have used statistical process control (SPC) methods and tools to study historical data and reveal differences between comparable items: shifts, products, machines, processes, plants, lot codes, and more.
The foundational benefit of statistical methods is predicting future behavior from historical data. That’s why control charts, box-and-whisker plots, Pareto charts, and the like are so valuable: They indicate that if processes are not changed, then performance (positive or negative) will continue as it is.
Control charts are brilliant tools for assessing performance over time, and their related “control limits” are predictions of normal future behavior. The problem is that many SPC software products struggle to move beyond just data collection to offer truly insightful data analysis.
There’s a better way to fully utilize the data you already collect, provide thoughtful analysis that leads to valuable insights into how to improve your operations, and then leverage your valuable resources to achieve transformational results.
Stuck in the past? Lagging digital transformation is costly
For every area of manufacturing, both quality and time are valuable commodities. Perhaps that’s one reason real-time SPC solutions—which offer the benefit not just of improved product quality, but also of better process efficiency—are so attractive.
The challenge with most SPC solutions is that you can’t typically access and manipulate those data in useful ways. You might be able to review the data you collect on any given day, but how much time do you spend manipulating those data points to make them usable? Can you easily find the most important data as they are collected? Can you view your data in multiple ways, or compare data across production lines or sites?
To reveal trends and enable proactive, strategic analysis, quality pros are forced to export data into spreadsheets and run manual comparisons. In some cases, they are steered toward purchasing expensive add-on modules or external analysis programs for their legacy systems.
It’s a clunky way to do business. It’s outdated and doesn’t address the needs of today’s fast-paced manufacturers. And those workarounds add up to extra time and work for quality managers, plant managers, IT staff, and executives.
Figure 1: Quality professionals spend hours manually importing data into spreadsheets and manipulating those data to compare different targets and tolerances.
Addressing the need: Better SPC analysis for proactive quality control
To get a real grip on quality data, it’s time to consider what you really need from analysis:
• The ability to quickly identify and solve issues that crop up on the production line—ideally before they cause wasted product
• A way to quickly access, analyze, and communicate data in response to executive, customer, or auditor requests
• Insight to determine how to make production run as smoothly and efficiently as possible, and as close to full capacity as possible
To meet these requirements, your quality intelligence solution should enable you to easily find exactly the data you want, from any time period you specify. And it should let you view your data in multiple ways, comparing products, production lines, or even sites across the entire enterprise. Most important, you should be able to make these comparisons without manually juggling multiple spreadsheets.
The key to this level of analysis is centralized and standardized data. The problem is that although many systems claim to use a “centralized database,” their underlying database technology isn’t up to the task of truly unifying your data in a way that enables extensive and complex comparisons.
A truly centralized unified data repository (UDR) automates and standardizes data storage. As a result, all your data are available—and easy to work with. No more exporting and importing data into offline products just to compile reports. With software such as InfinityQS’ Enact as your UDR, you can create dashboards that allow you to quickly create charts, graphs, and reports from your SPC data.
Figure 2: Being able to instantly see detailed comparative information in a single view makes it quick and easy to prioritize actions and drive improvement.
Modern SPC analysis for modern manufacturing
InfinityQS quality intelligence solutions are built on a unified, centralized data repository that enables the following:
• Both real-time and historical analysis
• Comparisons across products, lines, sites, and more
• Big-picture analysis, with the ability to dive into details
• Complex data analysis in response to almost any query, from directly within the software
In fact, Enact goes so as far as to filter dashboard data according to role and responsibilities, so you are automatically alerted to the information that matters most to you at any given moment. Want to see more details? No problem: You can drill down for a more granular view at any time. There’s no need to export data or manually flip through charts or spreadsheets.
This increased flexibility in the way you view quality data can return valuable time to your operations and quality teams:
• Say goodbye to digging through data or walking the shop floor to find the information you need
• Run analyses and comparisons of any and all data, right from within Enact
• Gain the ability to catch out-of-spec processes immediately and pinpoint variances that occur even when processes are in-spec
When your SPC system automatically digitizes and stores data in a centralized, unified way, you maintain access to all your information, no matter when or where you need it. The benefits of this instant access extend far beyond the plant floor, saving time and effort across myriad tasks:
Save time in audits: With the ability to easily locate and access data from any day and time, without sorting through piles of paper or multiple spreadsheets, audit prep becomes much less agonizing. It can take days to retrieve papers from cold storage—but only minutes to pull up data that have been collected and stored automatically and digitally.
Improve traceability: InfinityQS solutions enable you to see process quality from any point in time, coupled with details about raw materials, shifts, and operators, and specific lines, equipment, and processes. Everyone can access the same data, so communications become easier and more efficient.
Respond immediately to customer requests: With flexible, dynamic reporting, you’ll be able to easily provide exactly the information that a customer requests, helping to focus and streamline the information-return process and head off costly delays and distractions.
Phased implementation for successful digital transformation
Making the switch away from manual data processes doesn’t need to be an all-or-nothing scenario. In fact, at InfinityQS, our SPC experts suggest that you start by implementing your new system on just one data-collection process and a handful of products in a focused proof of concept (PoC). A PoC will deliver a noticeable impact and provide measurable validation for a more comprehensive rollout. Starting in this way enables you to get used to your new procedure and gives you the bandwidth to explore its limits and possibilities without too much stress.
Then, once you gain true insight into your production data and begin to see the benefits, it becomes easier to see how even more data can offer more and bigger benefits. When you expect this type of worldview change, you can plan and account for it in your implementation timeline and budget.
Our software products are here for exactly what manufacturers need: to analyze data, identify differences in performance, and share that information with users so that corrective actions can be put in place to improve overall performance and quality. In short, our solutions offer manufacturers the ability to transform quality performance across shifts, production lines, plants, regions—and across the whole enterprise.
As manufacturing looks toward the future, organizations need to support agile operations and not just manage quality but master it. InfinityQS provides solutions to empower workers with information and insights no matter where they are, optimize operations and productivity, and adapt to rapid changes. Please visit our website to learn more about our Enact Quality Intelligence platform.
Add new comment