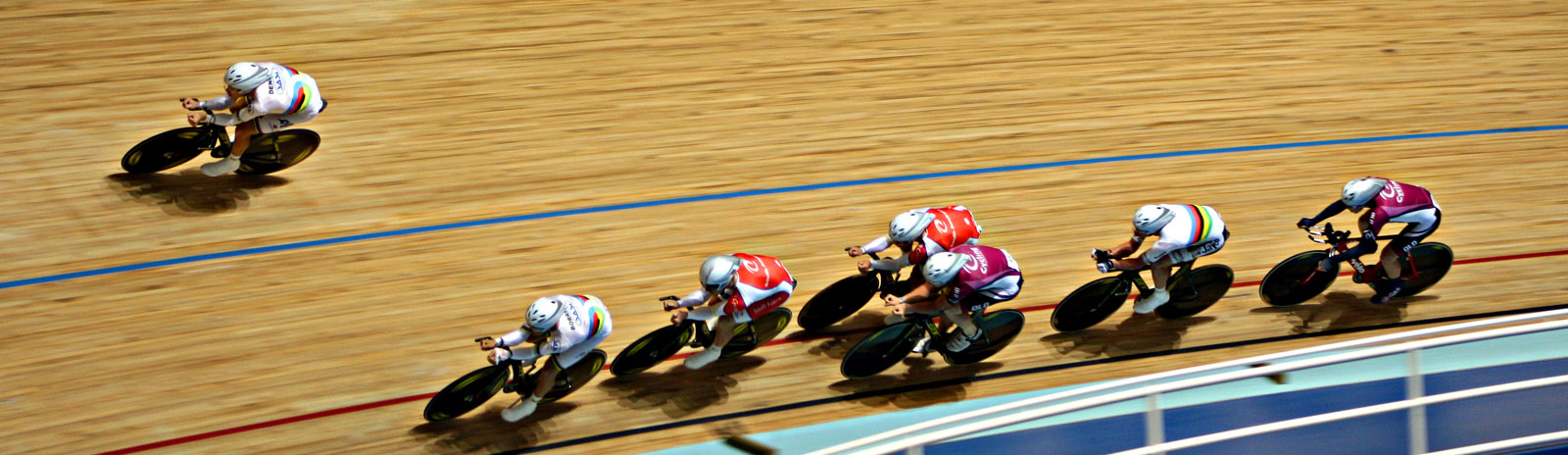
Strategy and Tactics. Credit: "The Catch" by cas_ks
It’s been 40 years since “If Japan Can, Why Can’t We?”, W. Edwards Deming, and total quality management. More than 33 years have passed since the release of the first iteration of ISO 9001 (remember checklists?). For four decades the importance of building quality into processes rather than trying to “inspect in” quality has been pounded into our little quality management brains. Proactive good, reactive bad. We get it.
Or do we?
Despite “risk management” or “risk-based thinking” becoming part of everyday quality parlance, quality on the ground is still largely reactionary. Tactical rather than strategic. In short, we still seem to be just “doing” quality rather than mastering it, i.e., we are using traditional quality processes and tools at only the shop-floor level rather than using next-generation enterprisewide quality tools throughout our entire organization.
When we talk about tactics vs. strategy in the quality world, we can think of strategy as the overall vision or goal of a company to, for instance, reduce waste, improve efficiency, make more product, make it better, make it faster, make it cheaper, and make it sustainable. Tactics are the specific analytical tools (such as statistical process control) and processes that we apply to discrete parts of our facility to achieve those goals: e.g., decrease variability of specific production equipment, rearrange production flow to make it more efficient, or employ more efficient production technologies that reduce scrap and waste.
Undeniably the first tool we employ at the shop-floor level is product inspection. As we get more sophisticated, those product inspections are analyzed using statistical process control (SPC) methods. At a granular level, we use data collection and statistical analysis software to examine how processes are performing, and from there make decisions on what actions to take to improve those processes. These SPC software tools are usually stand-alone but preferably, as we will see, should be enterprisewide.
It is at this tactical application of SPC where most companies stop. In fact, you could even say they get stuck, afraid of taking their data and tools to the next level. This is an example of what we mean by “doing” quality. It’s an important first step on a journey that ultimately leads to mastering quality.
“Organizations have lacked a strategic intent to their quality data,” says Eric Weisbrod, vice president of product management at InfinityQS. “By that I mean that their data are typically collected with quality compliance in mind. This is an important reason for quality data, I don’t want to diminish that, but there’s more to it. Their quality data can be used for much more.”
For example, says Weisbrod, data collected for net-weight compliance (MAV or T1T2) can also be used to determine how much product is being given away in overfill. From these existing data, an organization can see its average overfill (mean) and the variation (standard deviation) to see how much it can potentially reduce overfill and still remain within compliance. These tactical data collected to ensure compliance and avoiding underfill could help fulfill a company’s strategic goals of both reducing waste and lowering cost.
Net weight is one example, but the same applies to scrap, rework, and even process costs. Think of a lathe making shafts. If you can safely run to the “high side” of the shaft diameter, you can reduce the amount of time to machine a single shaft, reduce scrap, and increase the number of pieces each tool can cut.
“Most organizations are sitting on data like this but aren’t using it to improve their processes, which is a shame because it can result in a significant benefit to their bottom line,” says Weisbrod.
SPC at the strategic level
What if your CEO came into a meeting and asked, “Where are our biggest opportunities for quality improvement?”
No doubt, the guys closest to production are going to give answers like, “Well, we’ve got some pretty old filling equipment on our line, and we’ve reduced process variability about as far as we can go; that’s the best our equipment can do. The only way to improve process variability and minimize overfill on that line is to invest in new fillers.”
That statement is no doubt true. And it is also true that something needs to be done. But, that is just addressing a discrete need—outdated production equipment is limiting quality. Hidden behind that tactic is a larger opportunity that could be addressed at the strategic level—reduce waste and increase product profit margins. This is the difference between doing quality vs. mastering it.
What the CEO is really asking is not how to just improve product characteristics to meet customer specifications, but also how we address enterprisewide strategic goals to:
• Optimize man, machine, and materials
• Improve overall company performance while looking at cost, efficiency, productivity, waste, and yield
• Protect the brand by ensuring product safety
• Avoid risk in all aspects of the company
• Identify opportunities for improvement (think risks/opportunities from ISO QMS standards)
• Build a sustainable organization
And that is the tension between tactics and strategy. The CEO speaks strategy; the shop floor speaks tactics. The shop floor needs to keep production moving, producing products as quickly and mistake-free as possible. The CEO needs to look at the organization as a whole and how any action, taken anywhere in the company, benefits all stakeholders. There is often a disconnect, a lack of translation or collaboration, between the two.
There is a language that all can understand
So how do you develop a strategic approach to quality? The irony is that both strategists and tacticians may already be speaking a common language—the language of quality—and using a common tool, SPC. The problem is companies are too often using SPC—usually some sort of stand-alone SPC software—only at the tactical level to address discrete shop-floor issues. These tools are often not useful, or even configurable, to address strategic issues. With the right enterprisewide SPC software, you can use SPC tools and embrace the same core disciplines at the strategic level that we are all already familiar with at the tactical level—reduce variability, reduce volatility, reduce unpredictability.
The only difference is which tools are used and in what order. Generally speaking, a tactical approach focuses on real-time problem solving, and the process is usually to collect data, act on those data, analyze the results, and repeat. A strategic approach focuses on the long term and usually requires that you collect data, analyze the data, and then act on the data, repeat.
Goal of this series
Our goal in this Mastering Quality series of articles is to get readers to connect the dots between strategic and tactical uses for the same underlying data, using the appropriate SPC tools. If you are using SPC on the shop floor, you may already be generating data that can be analyzed and utilized strategically if you have the right software. With the right enterprise SPC software, the output of your nuts-and-bolts shop-floor SPC analysis becomes the input for your corporate strategic SPC analysis.
A case study will move us from a shop-floor, discrete problem-solving application using a familiar SPC tool and show how the output of that application will then serve as the input to more tools that help us address our strategic goals. This is the same tool set, the same enterprise SPC software, used differently.
We aren’t saying viewing quality strategically from an enterprise perspective is easy. It isn’t. While it is easy to identify a discrete problem and address it, it is very difficult, overwhelming even, to try to look at the entire enterprise unless, of course, you have an SPC solution that is built for the enterprise. Even with enterprise SPC software, you shouldn’t try to take on enterprise quality all at once. It’s better and more cost-effective to start small, learn, and apply lessons learned as you grow your approach.
The overall goal for any company is to move the entire enterprise from being reactive to proactive, unpredictable to predictable, and from analyzing data offline, after-the-fact, to utilizing real-time data in the here and now. This is the fundamental yet critical difference between doing quality and mastering it.
In the next couple of articles we will examine the difference between using SPC tactically and using it strategically.
Comments
Applicable to Healthcare
Hi Dirk, you bring up some great points. You mention manufacturing but these are also very applicable to Healthcare. Most healthcare projects tend to be tactical in nature and so when management talks strategy these are not seen as in alignment to the strategy. Many times it is simply because the projects are not aligned to the bottom line so they are not counted.
Jim
SPC in HMLV environment
Good Day.
What the arpoch shoul'd be to use SPC in High-mix/Low-volume environment?
Wht data shoul'd be collected?
Which tools are best to use?
Thanks.
Regards
RE: SPC in HMLV environment
The approaches used in a high-mix, low-volume (HMLV) environment aren’t that different than other environments. First off, compliance to specification limits is always the biggest driver because that determines whether your products can be sold or if they require rework or, even worse, need to be scrapped. Here, exception reporting and using things like specification limit violations and Pareto charts work the same to understand where your biggest opportunities are.
You asked what data should be collected and the short answer is, “You should measure those elements of your products and processes that have a significant impact on your product quality.” While that’s a very general answer, it is applicable in any situation and any industry. You shouldn’t be measuring things just for the sake of measuring, so making sure those measurements are impactful is important.
When most people think ‘SPC,’ they think of control charts and then the question turns to how to apply control charts in a HMLV environment. The biggest differentiator in the approaches used depends on how low the volume is. If you make small production runs of the same products, you can use previous production runs to understand process variation and use traditional SPC tools like Xbar-s, IX-MS, etc. If your production volumes are VERY low (e.g. satellites, where maybe only one is made!), you can utilize data transformations like deviation from target, short run transformations, etc. to combine data from similar processes to analyze variation on one chart. While these methods are available, they are often not required and therefore not commonly used. Here is an example of a short run Xbar-s chart:
https://www.infinityqs.com/statistical-process-control/spc-chart-guide/xbar-and-s-chart/short-run-xbar-s-chart-example
One tool we really like to understand variation is a Box-and-Whisker chart. Box-and-Whisker charts allow you to not only group and analyze data in different ways, but provide a visualization that makes it more intuitive to understand the differences in the performance of your products and processes. Here’s an example of how a Box-and-Whisker chart was used to identify process variation. While this example isn’t HMLV, the principles still apply and it provides a good example of the visual power of Box-and-Whisker charts:
https://www.infinityqs.com/resources/success-stories/uncover-cost-savings-by-examining-in-spec-spc-data
Eric
Add new comment